Deposition methods in fabrication are critical processes used to create thin films or layers of material on a substrate, particularly in the semiconductor and electronics industries. These methods are broadly categorized into Physical Vapor Deposition (PVD) and Chemical Vapor Deposition (CVD), each with specialized techniques tailored to specific applications. PVD techniques, such as evaporation and sputtering, involve physically transferring material from a source to a substrate, often under vacuum conditions. CVD techniques, on the other hand, rely on chemical reactions to deposit materials from a gas phase onto the substrate. Advanced variants like Plasma-Enhanced CVD (PECVD) and Atomic Layer Deposition (ALD) offer enhanced control over film properties and thickness. These methods are essential for producing high-performance materials and devices, such as semiconductors, optical coatings, and functional coatings.
Key Points Explained:
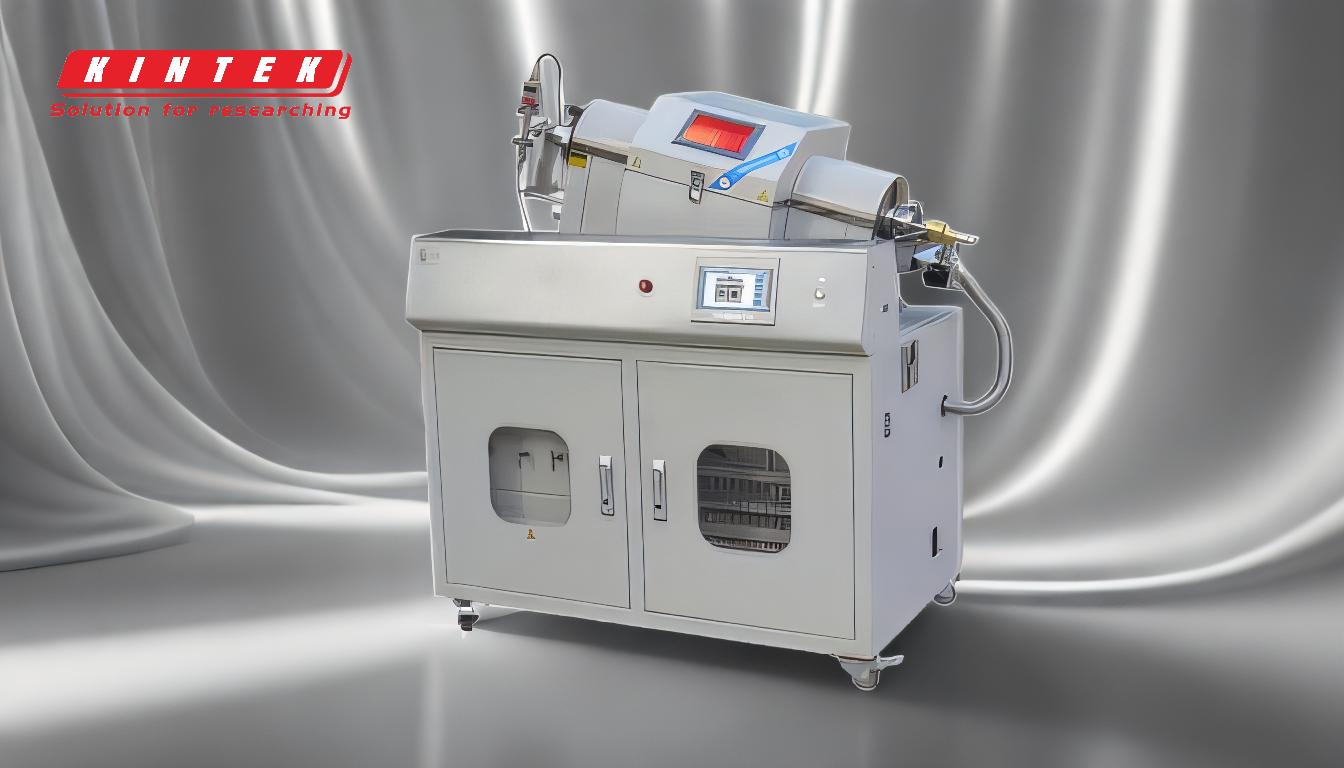
-
Overview of Deposition Methods in Fabrication
- Deposition methods are used to create thin films or layers of material on a substrate, which is a fundamental step in semiconductor manufacturing and other high-tech industries.
- These methods are broadly classified into Physical Vapor Deposition (PVD) and Chemical Vapor Deposition (CVD), each with distinct mechanisms and applications.
-
Physical Vapor Deposition (PVD)
- PVD involves the physical transfer of material from a source to a substrate, typically under vacuum conditions.
- Common PVD techniques include:
- Evaporation: The target material is heated until it evaporates, and the vapor condenses on the substrate to form a thin film.
- Sputtering: A plasma or gaseous atoms are used to dislodge atoms from a target material, which then deposit onto the substrate.
- Cathodic Arc Deposition: High-energy arcs vaporize material from a cathode, which then deposits onto the substrate.
- Pulsed Laser Deposition: A laser ablates material from a target, creating a plume that deposits onto the substrate.
- PVD is widely used for applications requiring high purity and precise control over film properties, such as in optical coatings and microelectronics.
-
Chemical Vapor Deposition (CVD)
- CVD relies on chemical reactions to deposit materials from a gas phase onto a substrate.
- Key CVD techniques include:
- Low Pressure CVD (LPCVD): Operates at reduced pressures to improve film uniformity and quality.
- Plasma-Enhanced CVD (PECVD): Uses plasma to enhance chemical reactions, enabling deposition at lower temperatures.
- Atomic Layer Deposition (ALD): Deposits materials one atomic layer at a time, offering exceptional control over film thickness and uniformity.
- Atmospheric Pressure CVD (APCVD): Operates at ambient pressure, suitable for high-throughput applications.
- CVD is essential for depositing materials like silicon dioxide, silicon nitride, and metals in semiconductor devices.
-
Specialized Deposition Techniques
- Epitaxial Deposition (Epi): Used to grow crystalline layers on a substrate, maintaining the same crystal structure. This is critical for high-performance semiconductor devices.
- Diamond-Like Carbon (DLC): A specialized coating technique used to deposit hard, wear-resistant carbon films.
- Sol-Gel Deposition: A non-vacuum technique where a solution is applied to a substrate and then solidified to form a thin film.
-
Applications of Deposition Methods
- Semiconductor Manufacturing: Deposition methods are used to create conductive, insulating, and semiconducting layers in integrated circuits.
- Optical Coatings: PVD and CVD are used to deposit anti-reflective, reflective, and protective coatings on lenses and mirrors.
- Functional Coatings: Techniques like thermal spraying and electrochemical deposition are used to apply protective and functional coatings to industrial components.
-
Advantages of Deposition Methods
- Precision: Techniques like ALD and PECVD offer atomic-level control over film thickness and composition.
- Versatility: A wide range of materials, including metals, ceramics, and polymers, can be deposited using these methods.
- Scalability: Many deposition techniques, such as CVD and PVD, are scalable for high-volume manufacturing.
-
Challenges and Considerations
- Cost: Advanced techniques like ALD and PECVD can be expensive due to the need for specialized equipment and high-purity materials.
- Complexity: Some methods, such as epitaxial deposition, require precise control over process parameters like temperature and pressure.
- Material Compatibility: Not all materials can be deposited using every technique, requiring careful selection based on the application.
-
Future Trends in Deposition Technology
- Nanotechnology: Deposition methods are increasingly being used to fabricate nanostructured materials for advanced electronics and energy applications.
- Sustainability: Research is focused on developing eco-friendly deposition techniques that minimize waste and energy consumption.
- Hybrid Techniques: Combining PVD and CVD methods to leverage the strengths of both approaches is an emerging trend.
By understanding the various deposition methods and their applications, equipment and consumable purchasers can make informed decisions about the best techniques and materials for their specific needs.
Summary Table:
Category | Key Techniques | Applications |
---|---|---|
Physical Vapor Deposition (PVD) | Evaporation, Sputtering, Cathodic Arc Deposition, Pulsed Laser Deposition | Optical coatings, microelectronics, high-purity films |
Chemical Vapor Deposition (CVD) | LPCVD, PECVD, ALD, APCVD | Semiconductor devices, silicon dioxide, silicon nitride, metal films |
Specialized Techniques | Epitaxial Deposition, Diamond-Like Carbon (DLC), Sol-Gel Deposition | High-performance semiconductors, wear-resistant coatings, non-vacuum thin films |
Advantages | Precision, Versatility, Scalability | High-performance materials, scalable manufacturing |
Challenges | Cost, Complexity, Material Compatibility | Specialized equipment, precise control, material selection |
Need help choosing the right deposition method for your application? Contact our experts today!