The deposition rate of Low-Pressure Chemical Vapor Deposition (LPCVD) is influenced by several factors, including the process parameters and the materials being deposited. While the provided references do not directly specify the exact deposition rate of LPCVD, they offer insights into the general principles and influencing factors of deposition processes, which can be extrapolated to understand LPCVD. The deposition rate in LPCVD is typically controlled by parameters such as temperature, pressure, gas flow rates, and the chemical reactions involved. These factors collectively determine the efficiency and uniformity of the deposition process.
Key Points Explained:
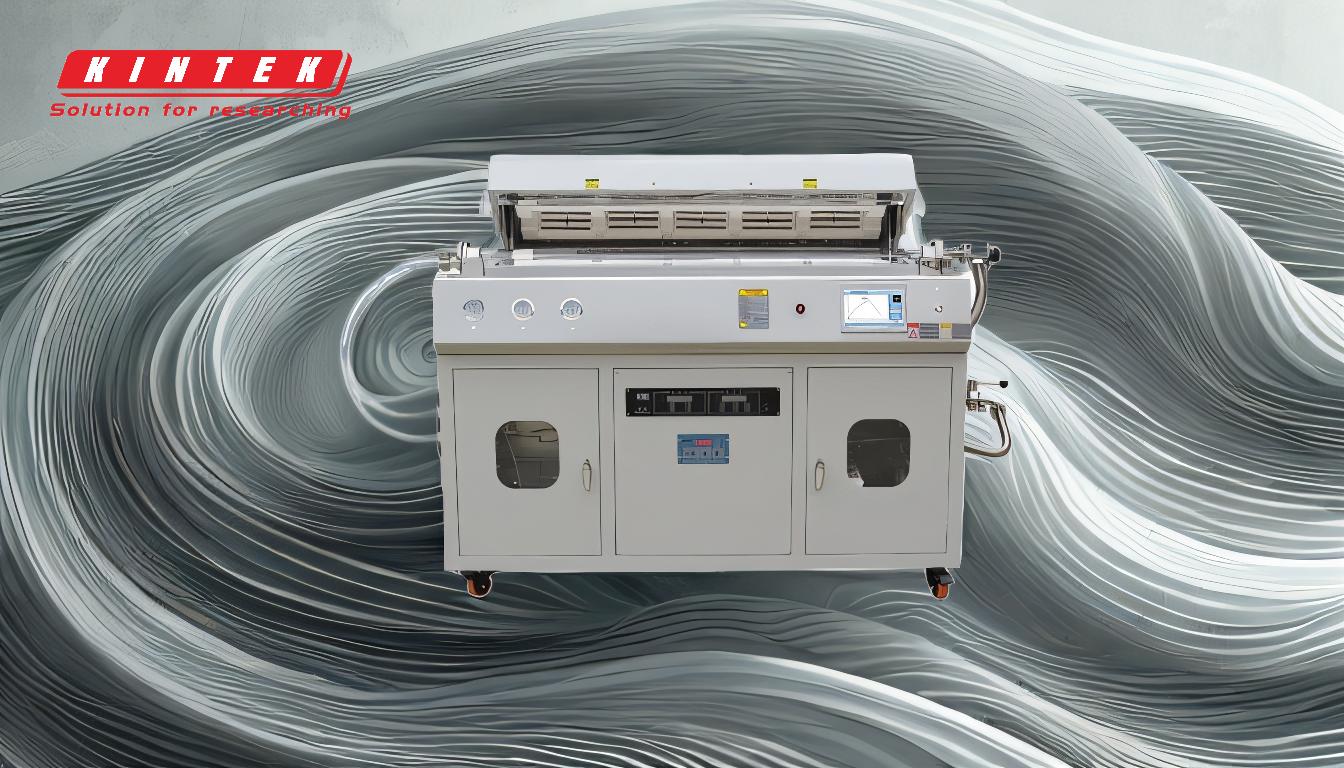
-
Influence of Process Parameters on Deposition Rate:
- The deposition rate in LPCVD is highly dependent on process parameters such as temperature, pressure, and gas flow rates. Higher temperatures generally increase the reaction rates, leading to faster deposition. Similarly, optimal pressure and gas flow rates ensure efficient transport of reactants to the substrate surface, enhancing the deposition rate.
-
Material-Specific Deposition Rates:
- LPCVD is used to deposit a variety of materials, including polysilicon, silicon dioxide, and silicon nitride. Each material has its own unique deposition rate due to differences in chemical reactivity and the specific conditions required for deposition. For example, polysilicon deposition typically occurs at higher temperatures compared to silicon dioxide.
-
Comparison with Other Deposition Techniques:
- Unlike Physical Vapor Deposition (PVD), which relies on physical processes like sputtering, LPCVD is a chemical process. This means that the deposition rate in LPCVD is more influenced by chemical reaction kinetics rather than physical factors such as target material properties or beam energy, as seen in PVD.
-
Uniformity and Thickness Control:
- The uniformity of the deposited film and its thickness are critical in LPCVD processes. Factors such as the target-substrate distance and the size of the erosion zone (in sputtering) can affect thickness uniformity. In LPCVD, maintaining uniform gas flow and temperature distribution across the substrate is essential for achieving consistent film thickness and quality.
-
Practical Applications and Considerations:
- LPCVD is widely used in semiconductor manufacturing for depositing gate contacts, planarization layers, and dielectric films. The deposition rate must be carefully controlled to meet the specific requirements of each application, ensuring that the films have the desired properties and performance.
By understanding these key points, one can appreciate the complexity and precision required in controlling the deposition rate in LPCVD processes. The interplay of chemical reactions, process parameters, and material properties all contribute to the efficiency and effectiveness of the deposition process.
Summary Table:
Factor | Impact on Deposition Rate |
---|---|
Temperature | Higher temperatures increase reaction rates, leading to faster deposition. |
Pressure | Optimal pressure ensures efficient reactant transport, enhancing deposition rate. |
Gas Flow Rates | Proper gas flow rates improve reactant delivery, boosting deposition efficiency. |
Material Properties | Different materials (e.g., polysilicon, silicon dioxide) have unique deposition rates. |
Chemical Reaction Kinetics | LPCVD relies on chemical reactions, making kinetics a key driver of deposition rate. |
Need precise control over your LPCVD process? Contact our experts today for tailored solutions!