The deposition rate in sputtering refers to the speed at which target material is ejected and deposited onto a substrate, forming a thin film. It is influenced by several factors, including the physical properties of the target material (e.g., mass, sputtering yield), the energy of incident ions, the type of power source (DC or RF), chamber pressure, and the kinetic energy of emitted particles. These factors collectively determine the sputtering yield, which is the number of target atoms ejected per incident ion. Precise control of these parameters ensures consistent deposition rates, which are critical for achieving uniform and high-quality thin films.
Key Points Explained:
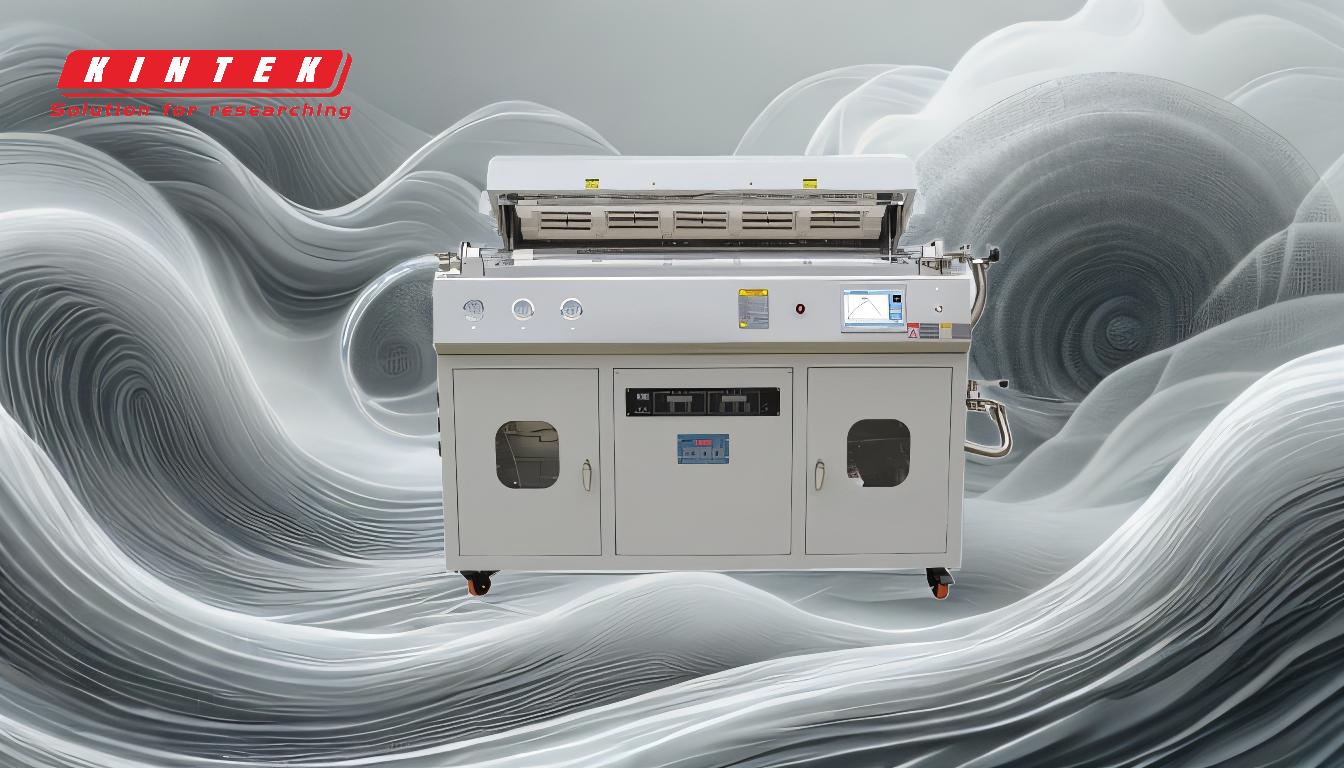
-
Definition of Deposition Rate in Sputtering:
- The deposition rate is the rate at which target material is ejected and deposited onto a substrate during the sputtering process.
- It is typically measured in nanometers per second (nm/s) or angstroms per second (Å/s).
-
Factors Influencing Deposition Rate:
-
Physical Properties of the Target Material:
- The mass of the target atoms and the sputtering yield (number of atoms ejected per incident ion) significantly affect the deposition rate.
- Different materials have varying sputtering yields due to differences in atomic bonding and structure.
-
Incident Ion Energy:
- Higher ion energy increases the sputtering yield, leading to a higher deposition rate.
- However, excessively high energy can damage the target or substrate.
-
Type of Power Source:
- DC sputtering is commonly used for conductive materials, while RF sputtering is suitable for insulating materials.
- The choice of power source affects the deposition rate, material compatibility, and cost.
-
Chamber Pressure:
- Optimal chamber pressure improves the uniformity and coverage of the deposited film.
- Too high or too low pressure can negatively impact the deposition rate and film quality.
-
Kinetic Energy of Emitted Particles:
- The kinetic energy determines the direction and adhesion of particles on the substrate.
- Higher kinetic energy can enhance surface mobility, improving film quality but may also increase stress in the film.
-
Physical Properties of the Target Material:
-
Sputtering Yield:
- The sputtering yield is a critical parameter that directly influences the deposition rate.
- It depends on the mass of the ions, the angle of incidence, and the energy of the incident ions.
- For example, heavier target atoms typically have higher sputtering yields compared to lighter atoms under the same conditions.
-
Control of Deposition Rate:
-
Current and Beam Energy:
- Adjusting the current and beam energy allows precise control over the deposition rate.
- Higher current or beam energy generally increases the deposition rate but must be balanced to avoid damaging the target or substrate.
-
Cycle Time and Power:
- The thickness of the deposited film can be controlled by adjusting the cycle time and the power applied to the target.
- Longer cycle times or higher power levels result in thicker films.
-
Current and Beam Energy:
-
Practical Considerations for Equipment and Consumable Purchasers:
-
Material Compatibility:
- Ensure the sputtering system is compatible with the target material and substrate.
- For example, RF sputtering is necessary for insulating materials, while DC sputtering is suitable for conductive materials.
-
System Configuration:
- Choose a system with adjustable parameters (e.g., power, pressure, ion energy) to achieve the desired deposition rate and film quality.
-
Cost and Efficiency:
- Consider the cost of consumables (e.g., target materials) and the energy efficiency of the system.
- Systems with precise control over deposition parameters can reduce material waste and operational costs.
-
Material Compatibility:
By understanding and optimizing these factors, equipment and consumable purchasers can select the right sputtering system and parameters to achieve consistent and high-quality thin film deposition.
Summary Table:
Factor | Impact on Deposition Rate |
---|---|
Target Material | Mass and sputtering yield affect rate; heavier atoms typically have higher yields. |
Incident Ion Energy | Higher energy increases yield but excessive energy can damage target or substrate. |
Power Source | DC for conductive materials; RF for insulating materials. Affects rate and compatibility. |
Chamber Pressure | Optimal pressure ensures uniform deposition; too high/low pressures reduce quality. |
Kinetic Energy of Particles | Higher energy improves film quality but may increase stress. |
Optimize your sputtering process for high-quality thin films—contact our experts today!