A muffle furnace is a specialized heating device designed for high-temperature applications, capable of operating up to 1800°C. Its construction involves a ceramic inner chamber, typically made of alumina, which can withstand extreme heat and resist chemical corrosion. The furnace is insulated to minimize heat loss and ensure energy efficiency. Key components include the muffle (ceramic chamber), heating elements, insulation materials (fiber or refractory brick), and safety features like gas-tight doors. These furnaces are widely used in laboratories and industrial settings for processes such as annealing, sintering, and hardening. The design prioritizes durability, safety, and precise temperature control.
Key Points Explained:
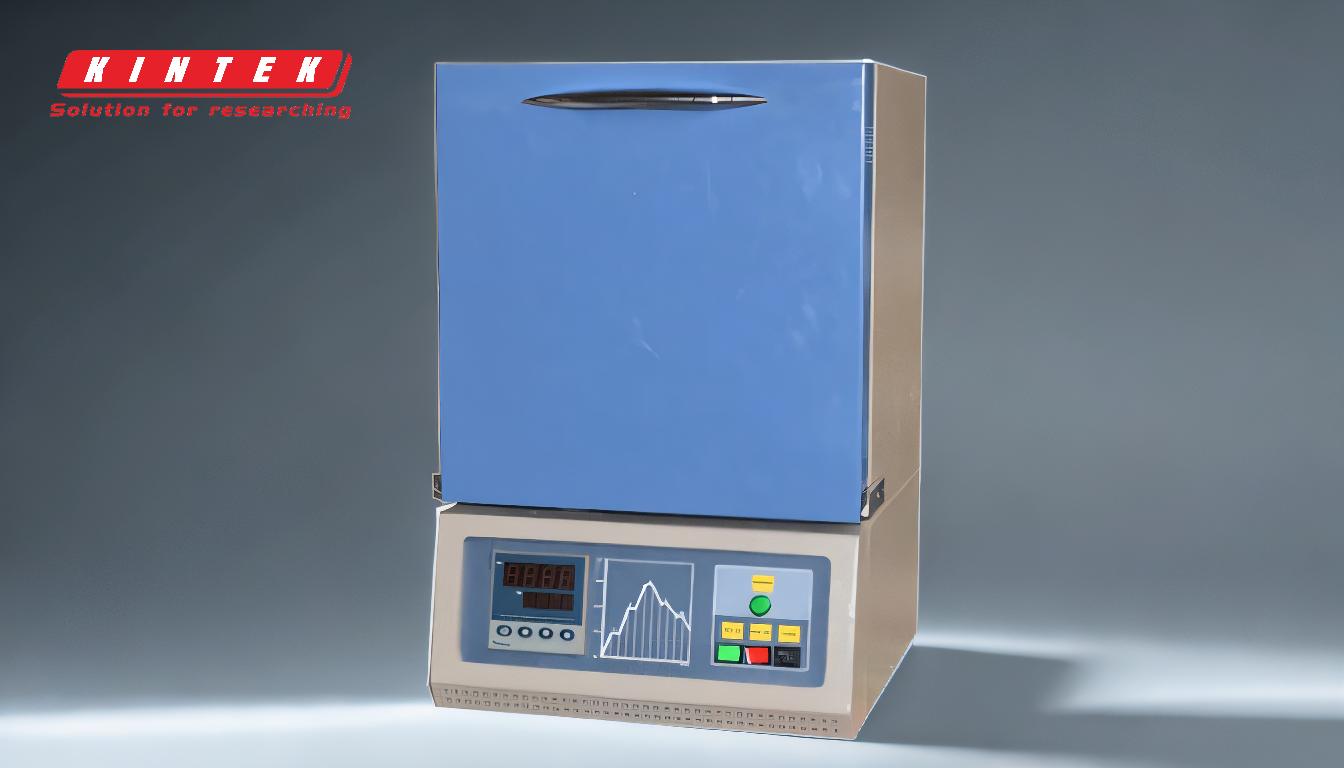
-
Ceramic Inner Chamber
- The muffle, or inner chamber, is typically made of ceramic materials like alumina.
- Ceramic is chosen for its ability to withstand high temperatures (up to 1800°C) without melting or degrading.
- It is also resistant to chemical corrosion, ensuring durability and effective heat transfer to the materials being processed.
- This design ensures the furnace can handle extreme conditions while maintaining structural integrity.
-
Insulation Materials
- The furnace is insulated to prevent heat loss and improve energy efficiency.
- Two common insulation materials are used:
- Fiber Material: Lightweight, soft, and excellent heat preservation properties.
- Refractory Brick Material: Heavier, harder, and provides general heat preservation.
- The choice of insulation depends on the specific application and desired thermal performance.
-
Heating Elements
- Heating elements are strategically placed to ensure uniform temperature distribution within the chamber.
- These elements are designed to operate at high temperatures without degrading, ensuring consistent performance.
-
Safety Features
- Modern muffle furnaces are equipped with safety features to prevent accidents.
- Gas-tight doors allow for quick loading and unloading of samples while maintaining a positive pressure inside the chamber.
- This design minimizes the risk of exposure to harmful gases or sudden temperature changes.
-
Types and Applications
- Muffle furnaces are commonly available in box-type designs.
- They are used for various high-temperature processes, including:
- Hardening
- Annealing
- Brazing
- Sintering
- Stress relief
- These furnaces can operate in both air and controlled atmospheres, making them versatile for laboratory and industrial use.
-
Design Considerations
- The design prioritizes durability, safety, and precise temperature control.
- The use of high-quality materials and advanced insulation ensures long-term reliability.
- Safety features and user-friendly designs make them suitable for a wide range of applications.
In summary, the design and construction of a muffle furnace focus on high-temperature resistance, energy efficiency, and safety. The use of ceramic materials, advanced insulation, and robust safety features ensures that these furnaces meet the demands of both laboratory and industrial environments.
Summary Table:
Component | Description |
---|---|
Ceramic Inner Chamber | Made of alumina, withstands up to 1800°C, resists corrosion, ensures durability. |
Insulation Materials | Fiber (lightweight, soft) or refractory brick (heavy, hard) for heat retention. |
Heating Elements | Strategically placed for uniform temperature distribution and consistent performance. |
Safety Features | Gas-tight doors, positive pressure design to prevent accidents and gas exposure. |
Applications | Annealing, sintering, hardening, brazing, and stress relief in labs and industries. |
Interested in a muffle furnace for your lab or industry? Contact us today to learn more!