Mechanical presses and hydraulic presses are both widely used in manufacturing and industrial applications, but they operate on fundamentally different principles and are suited for different tasks. A mechanical press uses a motor-driven flywheel and a mechanical linkage to generate force, making it faster and more suitable for high-speed operations like stamping and punching. In contrast, a hydraulic press relies on fluid pressure to generate force, offering greater control over force and speed, which makes it ideal for tasks requiring precision, such as deep drawing or forming complex shapes. The choice between the two depends on factors like production speed, force requirements, and the type of material being processed.
Key Points Explained:
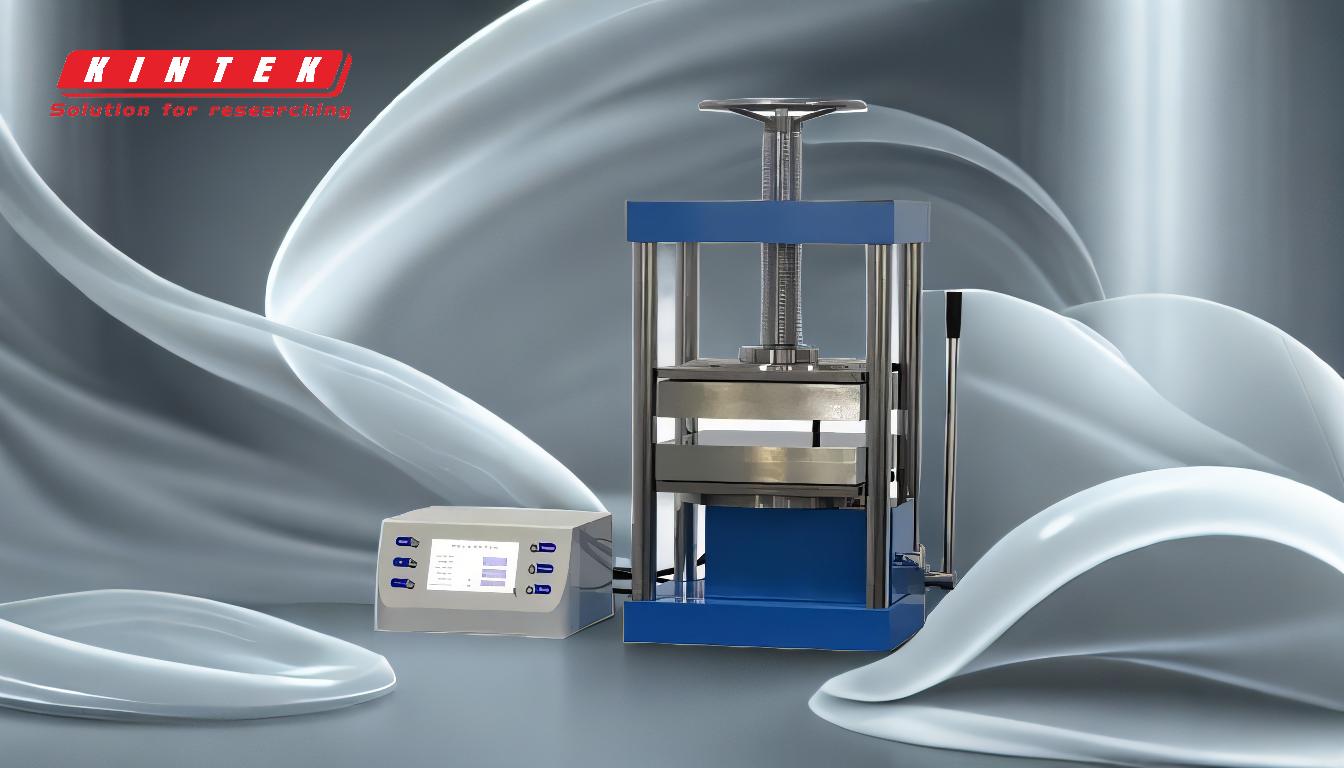
-
Operating Principle:
- Mechanical Press: Operates using a motor-driven flywheel that stores rotational energy. This energy is transferred through a mechanical linkage (such as a crank or eccentric gear) to the ram, which applies force to the workpiece. The force is generated quickly and is consistent with each stroke.
- Hydraulic Press: Uses hydraulic fluid to generate force. A pump moves the fluid into a cylinder, which then pushes a piston to apply force to the ram. The force can be precisely controlled by adjusting the fluid pressure, allowing for variable speed and force during the operation.
-
Speed and Efficiency:
- Mechanical Press: Known for its high-speed operation, making it ideal for repetitive tasks like stamping, blanking, and punching. The consistent stroke rate ensures high productivity in mass production environments.
- Hydraulic Press: Generally slower than mechanical presses due to the time required to build and release hydraulic pressure. However, this slower speed allows for better control over the forming process, which is crucial for precision tasks.
-
Force and Control:
- Mechanical Press: Delivers a fixed amount of force per stroke, which is determined by the mechanical setup. While this is efficient for high-speed operations, it offers less flexibility in adjusting force during the process.
- Hydraulic Press: Provides variable force and speed control, making it suitable for applications requiring deep drawing, molding, or forming complex shapes. The ability to adjust force dynamically ensures better results for delicate or intricate work.
-
Applications:
- Mechanical Press: Commonly used in industries requiring high-volume production, such as automotive manufacturing for stamping metal parts or electronics for punching components.
- Hydraulic Press: Preferred for applications needing precision and versatility, such as forging, laminating, or forming large metal sheets. It is also used in laboratories for material testing.
-
Maintenance and Durability:
- Mechanical Press: Requires regular maintenance of mechanical components like gears, belts, and linkages. However, its robust design makes it durable for high-speed, high-volume operations.
- Hydraulic Press: Maintenance focuses on the hydraulic system, including seals, pumps, and fluid levels. While hydraulic systems can be more complex, they are generally reliable when properly maintained.
-
Cost Considerations:
- Mechanical Press: Typically has a lower initial cost and is more cost-effective for high-speed, high-volume production. However, the cost of maintenance and potential downtime can add up over time.
- Hydraulic Press: Often has a higher initial cost due to the complexity of the hydraulic system. However, its versatility and precision can lead to cost savings in applications requiring fewer but more complex operations.
-
Energy Efficiency:
- Mechanical Press: Generally more energy-efficient for high-speed operations, as the flywheel stores and releases energy efficiently with each stroke.
- Hydraulic Press: Can be less energy-efficient due to the constant need to maintain hydraulic pressure, especially during idle times. However, modern hydraulic systems are designed to minimize energy loss.
In summary, the choice between a mechanical press and a hydraulic press depends on the specific requirements of the task, including production speed, force control, and material type. Mechanical presses excel in high-speed, repetitive operations, while hydraulic presses offer greater flexibility and precision for complex forming tasks.
Summary Table:
Aspect | Mechanical Press | Hydraulic Press |
---|---|---|
Operating Principle | Uses a motor-driven flywheel and mechanical linkage for force generation. | Relies on hydraulic fluid pressure to generate force. |
Speed | High-speed, ideal for repetitive tasks like stamping and punching. | Slower, but offers better control for precision tasks. |
Force Control | Fixed force per stroke, less flexibility. | Variable force and speed control, ideal for complex shapes. |
Applications | High-volume production (e.g., automotive stamping). | Precision tasks (e.g., deep drawing, material testing). |
Maintenance | Regular maintenance of mechanical components. | Focus on hydraulic system (seals, pumps, fluid levels). |
Cost | Lower initial cost, cost-effective for high-speed operations. | Higher initial cost, but versatile for complex tasks. |
Energy Efficiency | More efficient for high-speed operations. | Less efficient due to constant hydraulic pressure maintenance. |
Need help choosing the right press for your application? Contact our experts today for personalized advice!