The primary difference between AC (RF) and DC sputtering lies in the type of power source used and the materials they are suited for. DC sputtering uses a Direct Current power source, making it ideal for conductive materials like pure metals, offering high deposition rates and cost-efficiency for large substrates. In contrast, RF sputtering uses an Alternating Current power source, typically at 13.56 MHz, and is suitable for both conductive and non-conductive materials, especially dielectric targets. RF sputtering has a lower deposition rate, is more expensive, and is better suited for smaller substrates. Additionally, RF sputtering involves a two-cycle process of polarization and reverse polarization, while DC sputtering accelerates positively charged gas ions toward the target for deposition.
Key Points Explained:
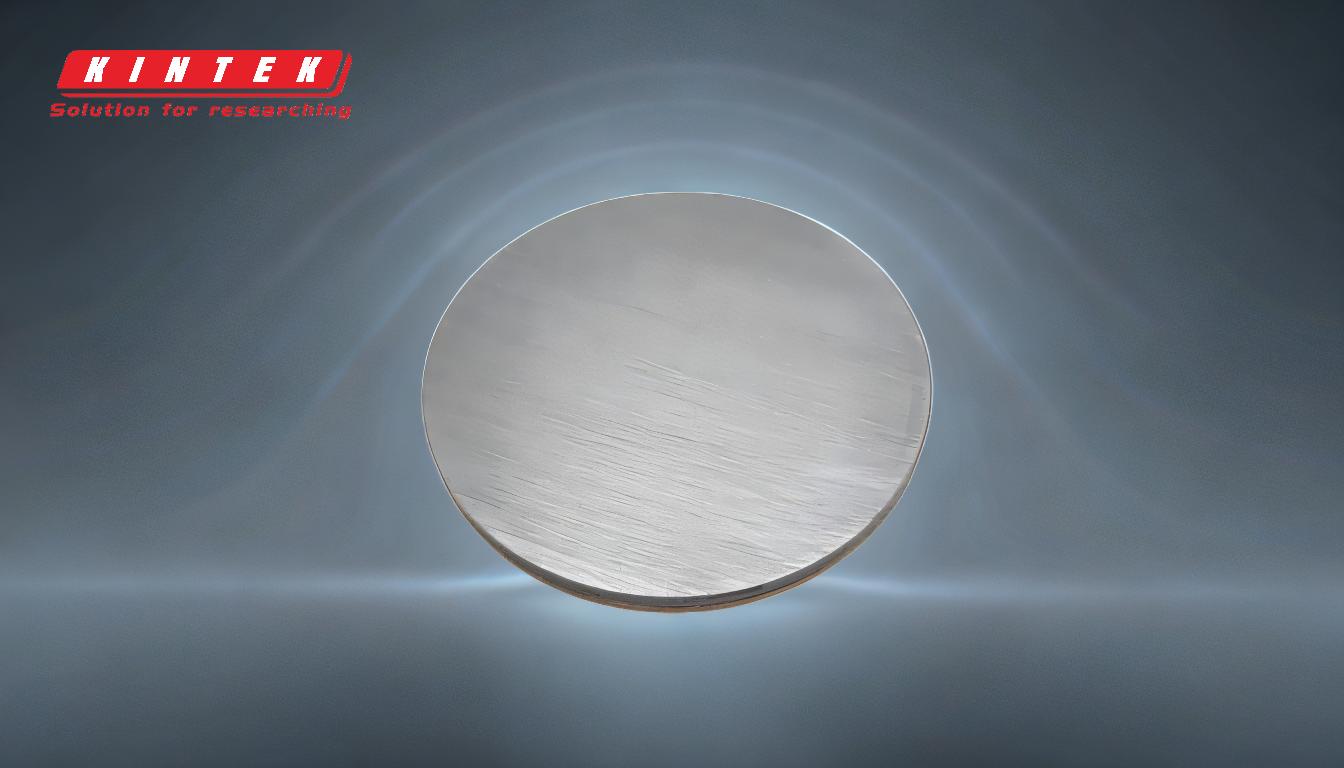
-
Power Source:
- DC Sputtering: Uses a Direct Current (DC) power source. This method is straightforward and effective for conductive materials, as it relies on a constant current flow.
- RF Sputtering: Uses an Alternating Current (AC) power source, typically at 13.56 MHz. The alternating polarity allows the method to handle both conductive and non-conductive materials.
-
Material Suitability:
- DC Sputtering: Best suited for conductive materials like pure metals (e.g., Iron, Copper, Nickel). It is not effective for non-conductive materials because the constant current cannot neutralize the charge buildup on the target surface.
- RF Sputtering: Suitable for both conductive and non-conductive materials, especially dielectric targets. The alternating current neutralizes the charge buildup on the target surface, making it versatile for a broader range of materials.
-
Deposition Rate:
- DC Sputtering: Offers a high deposition rate, making it efficient for large-scale production and large substrates.
- RF Sputtering: Has a lower deposition rate compared to DC sputtering, which can be a limiting factor for large-scale applications but is acceptable for smaller substrates.
-
Cost and Efficiency:
- DC Sputtering: More cost-effective and economical, especially for processing large quantities of large substrates.
- RF Sputtering: More expensive due to the complexity of the AC power source and the lower sputter yield, making it more suitable for smaller substrate sizes.
-
Process Mechanism:
- DC Sputtering: Accelerates positively charged gas ions toward the target, ejecting atoms that deposit on the substrates. This process is straightforward and efficient for conductive materials.
- RF Sputtering: Involves a two-cycle process of polarization and reverse polarization. During one half-cycle, electrons neutralize positive ions on the target surface, and during the other half-cycle, target atoms are sputtered and deposited on the substrate. This alternating process allows RF sputtering to handle non-conductive materials effectively.
-
Applications:
- DC Sputtering: Ideal for applications requiring high deposition rates and large-scale production, such as in the manufacturing of metal coatings and conductive layers.
- RF Sputtering: Suitable for applications involving both conductive and non-conductive materials, such as in the deposition of dielectric films and specialized coatings on smaller substrates.
By understanding these key differences, equipment and consumable purchasers can make informed decisions based on the specific requirements of their projects, whether they prioritize cost-efficiency, material versatility, or deposition rate.
Summary Table:
Aspect | DC Sputtering | RF Sputtering |
---|---|---|
Power Source | Direct Current (DC) | Alternating Current (AC), typically at 13.56 MHz |
Material Suitability | Best for conductive materials (e.g., pure metals) | Suitable for both conductive and non-conductive materials (e.g., dielectric films) |
Deposition Rate | High deposition rate, ideal for large-scale production | Lower deposition rate, better for smaller substrates |
Cost and Efficiency | Cost-effective for large substrates and high-volume production | More expensive, suitable for smaller substrates |
Process Mechanism | Accelerates positively charged gas ions toward the target | Two-cycle process: polarization and reverse polarization |
Applications | Metal coatings, conductive layers, large-scale production | Dielectric films, specialized coatings, smaller substrates |
Need help selecting the right sputtering method for your project? Contact our experts today for personalized guidance!