Induction furnaces and arc furnaces are both widely used in metallurgical processes, but they differ significantly in their heating mechanisms, applications, and capabilities. Induction furnaces use electromagnetic induction to generate heat within the metal itself, making them suitable for melting metals with low carbon content and producing high-quality alloys. They are often used for small-sized steel castings and have seen improvements in metallurgical capabilities over time. On the other hand, arc furnaces rely on an electric arc between electrodes and the metal to generate heat, making them more versatile for larger-scale operations and a wider range of steel grades. Arc furnaces generally have better metallurgical functions but are less suitable for melting low-carbon alloys due to the risk of carbon contamination from graphite electrodes.
Key Points Explained:
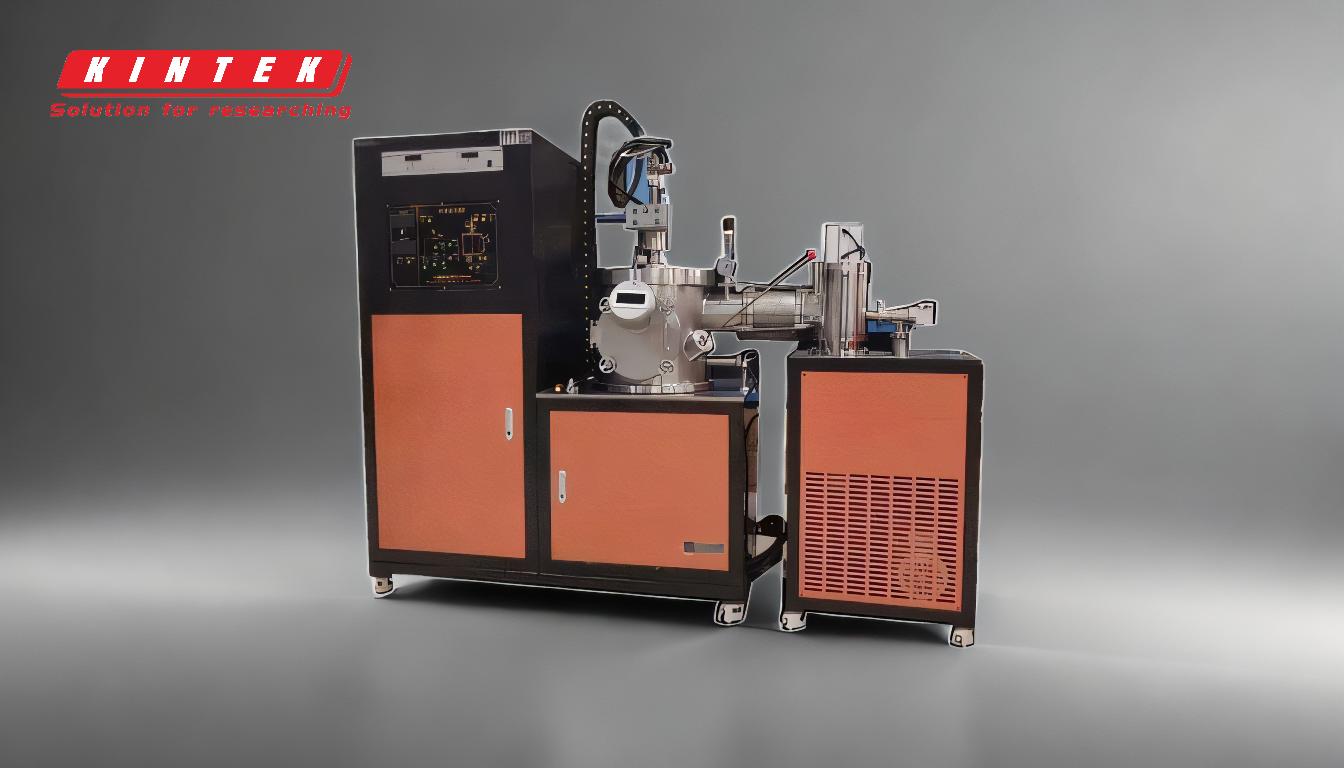
-
Heating Mechanism:
- Induction Furnace: Uses electromagnetic induction to generate heat directly within the metal. This method does not require contact with the metal, reducing contamination risks.
- Arc Furnace: Uses an electric arc formed between graphite electrodes and the metal to generate heat. This method involves direct contact with the metal, which can introduce carbon contamination.
-
Applications:
- Induction Furnace: Typically used for refining steel grades with general metallurgical quality requirements, especially for small-sized steel castings. It is also capable of producing high-quality low-alloy steels, high-alloy steels, and super low-carbon stainless steels.
- Arc Furnace: More versatile and commonly used for larger-scale operations. It can handle a wider range of steel grades but is less suitable for melting low-carbon alloys due to the risk of carbon contamination.
-
Metallurgical Capabilities:
- Induction Furnace: Historically, its metallurgical function was considered inferior to that of arc furnaces. However, advancements in equipment and refractories since the 1980s have significantly improved its capabilities, allowing for the production of high-quality alloys.
- Arc Furnace: Generally has better metallurgical functions and is more effective for refining a broader range of steel grades. However, it is less effective for producing low-carbon alloys due to the potential for carbon contamination from the electrodes.
-
Carbon Contamination:
- Induction Furnace: Does not require graphite electrodes, eliminating the risk of carbon contamination. This makes it ideal for melting steel and alloys with very low carbon content.
- Arc Furnace: Uses graphite electrodes, which can introduce carbon into the melt, making it less suitable for low-carbon alloys.
-
Design Considerations:
- Induction Furnace: Requires careful design of the magnetic field layout, especially for non-magnetic materials like aluminum. The inductor design must consider magnetic flux leakage and inter-turn distance to ensure efficient heating.
- Arc Furnace: Design focuses on the electrode configuration and the arc stability to ensure consistent heating and melting of the metal.
-
Operational Scale:
- Induction Furnace: More suited for smaller-scale operations and specialized applications requiring high-purity alloys.
- Arc Furnace: Better suited for larger-scale industrial operations where a wide range of steel grades are processed.
In summary, the choice between an induction furnace and an arc furnace depends on the specific metallurgical requirements, the scale of operation, and the need for minimizing carbon contamination. Induction furnaces are ideal for specialized, small-scale applications requiring high-purity alloys, while arc furnaces are more versatile and suitable for larger-scale operations with a broader range of steel grades.
Summary Table:
Feature | Induction Furnace | Arc Furnace |
---|---|---|
Heating Mechanism | Electromagnetic induction heats metal directly, reducing contamination risks. | Electric arc between electrodes and metal, which can introduce carbon. |
Applications | Ideal for small-scale operations, low-carbon alloys, and high-purity steel grades. | Versatile for larger-scale operations and a wide range of steel grades. |
Metallurgical Capabilities | Improved capabilities for producing high-quality alloys since the 1980s. | Better for refining a broad range of steel grades but less effective for low-carbon alloys. |
Carbon Contamination | No graphite electrodes, eliminating carbon contamination risks. | Graphite electrodes may introduce carbon, making it less suitable for low-carbon alloys. |
Operational Scale | Best for small-scale, specialized applications. | Suitable for large-scale industrial operations. |
Need help choosing the right furnace for your metallurgical process? Contact our experts today for personalized advice!