CVD (Chemical Vapor Deposition) and LPCVD (Low Pressure Chemical Vapor Deposition) are both techniques used for thin film deposition, but they differ significantly in their operational conditions and outcomes. CVD typically operates at atmospheric or near-atmospheric pressure and higher temperatures, making it suitable for a wide range of materials and complex geometries. LPCVD, on the other hand, operates at reduced pressures, which enhances film uniformity and reduces unwanted gas-phase reactions. This makes LPCVD particularly advantageous in semiconductor manufacturing where precise and uniform thin films are critical. Both methods have their unique advantages and are chosen based on the specific requirements of the application.
Key Points Explained:
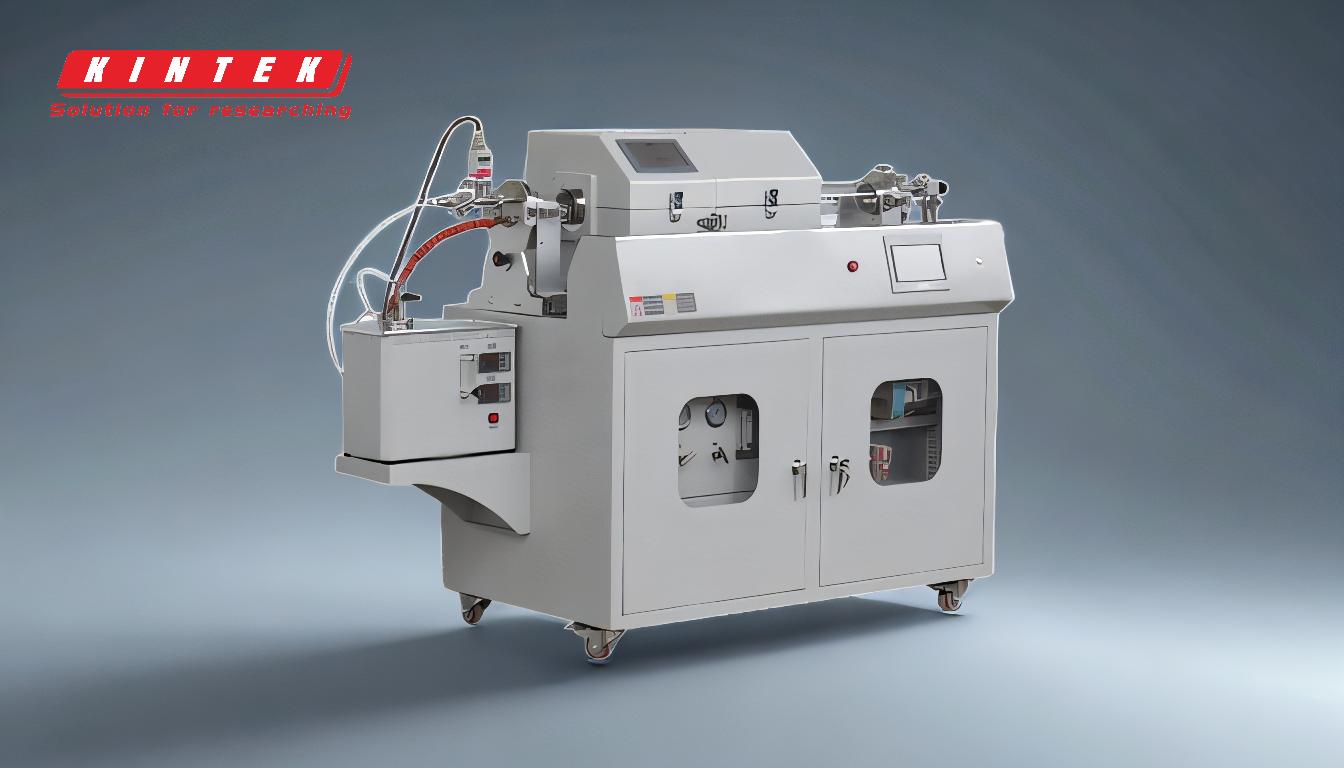
-
Operational Pressure:
- CVD: Operates at atmospheric or near-atmospheric pressure. This can lead to a higher likelihood of gas-phase reactions, which might affect the purity and uniformity of the deposited film.
- LPCVD: Operates at pressures below atmospheric pressure, typically around 133 Pa. The reduced pressure minimizes unwanted gas-phase reactions and enhances the uniformity and quality of the film.
-
Temperature Requirements:
- CVD: Generally requires higher temperatures, often between 450°C to 1050°C. These high temperatures can be beneficial for certain chemical reactions but may also introduce impurities and require more energy.
- LPCVD: Can operate at lower temperatures due to the reduced pressure, which decreases the activation energy needed for the deposition process. This is particularly useful for temperature-sensitive substrates.
-
Film Uniformity and Quality:
- CVD: While CVD can produce high-quality films, the uniformity might be compromised due to the higher pressure and temperature, leading to potential impurities and less uniform thickness.
- LPCVD: The lower pressure in LPCVD increases the gas diffusion coefficient and mean free path, resulting in more uniform film deposition, better resistivity uniformity, and improved trench coverage.
-
Application Suitability:
- CVD: Suitable for a wide range of materials and complex geometries due to its ability to coat virtually any surface and create strong chemical and metallurgical bonds. It is often used in applications where thick coatings are required.
- LPCVD: Particularly advantageous in the semiconductor industry where precise and uniform thin films are critical. The method's ability to suppress self-doping and reduce particle pollution makes it ideal for high-precision applications.
-
Economic and Practical Considerations:
- CVD: Often more economical for large-scale applications due to high deposition rates and the ability to produce thick coatings. However, it may require post-coating finishing and heat treating for certain materials.
- LPCVD: While it may have lower deposition rates compared to CVD, the improved film quality and uniformity can lead to better overall performance and yield in high-precision applications, potentially offsetting the initial cost differences.
In summary, while both CVD and LPCVD are valuable techniques for thin film deposition, the choice between them depends on the specific requirements of the application, including the need for film uniformity, operational temperature, and the nature of the substrate. LPCVD's advantages in producing high-quality, uniform films make it particularly suitable for the semiconductor industry, whereas CVD's versatility and high deposition rates make it a preferred choice for a broader range of applications.
Summary Table:
Aspect | CVD | LPCVD |
---|---|---|
Operational Pressure | Atmospheric or near-atmospheric pressure | Reduced pressure (typically ~133 Pa) |
Temperature | Higher (450°C to 1050°C) | Lower (due to reduced pressure) |
Film Uniformity | May have impurities and less uniform thickness | Enhanced uniformity and quality |
Application Suitability | Broad range of materials and complex geometries | Ideal for semiconductor manufacturing |
Economic Considerations | Economical for large-scale applications | Better performance and yield in high-precision applications |
Need help choosing between CVD and LPCVD for your application? Contact our experts today!