Chemical Vapor Deposition (CVD) and Plasma-Enhanced Chemical Vapor Deposition (PECVD) are both techniques used to deposit thin films onto substrates, but they differ significantly in their mechanisms, temperature requirements, and applications. CVD relies on thermal energy to drive chemical reactions, typically requiring high temperatures, which can limit its use with heat-sensitive materials. In contrast, PECVD uses plasma to activate the chemical reactions, enabling deposition at much lower temperatures. This makes PECVD more versatile for applications involving substrates with low thermal resistance, such as in semiconductor manufacturing. Additionally, PECVD offers enhanced deposition rates and better control over film properties compared to traditional CVD.
Key Points Explained:
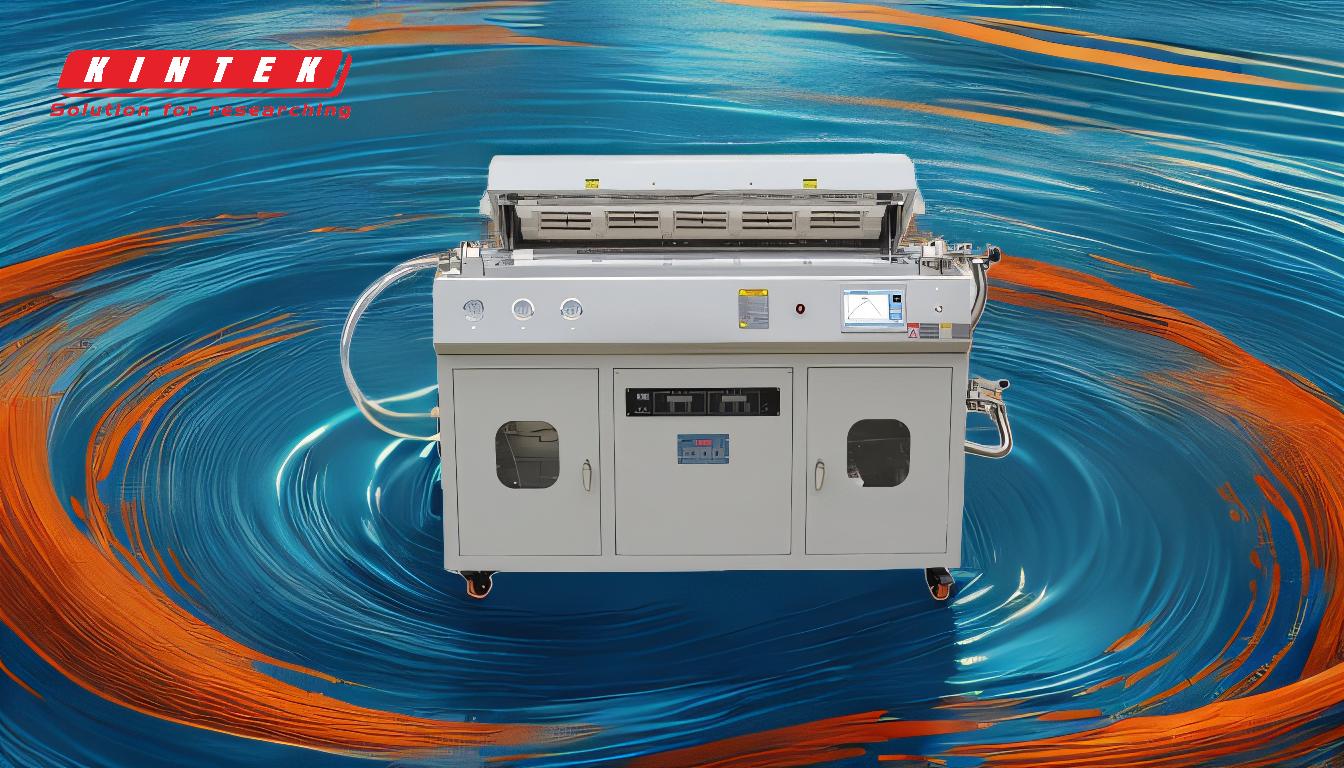
-
Mechanism of Deposition:
- CVD: In CVD, the deposition process is driven by thermal energy. The substrate or reactor is heated to high temperatures, which provides the energy needed to break chemical bonds in the reactant gases, leading to the formation of a thin film on the substrate.
- PECVD: PECVD, on the other hand, uses plasma to activate the reactant gases. The plasma contains high-energy electrons and ions that can break chemical bonds at much lower temperatures, eliminating the need for high thermal energy.
-
Temperature Requirements:
- CVD: Traditional CVD processes typically require high temperatures, often exceeding 500°C, to achieve the necessary chemical reactions. This can be a limitation when working with heat-sensitive materials.
- PECVD: PECVD can proceed at much lower temperatures, often below 300°C, making it suitable for substrates that cannot withstand high temperatures, such as certain polymers or pre-fabricated electronic components.
-
Applications:
- CVD: CVD is commonly used in applications where high-temperature processing is acceptable, such as in the production of high-purity materials, coatings for tools, and some semiconductor applications.
- PECVD: PECVD is particularly advantageous in semiconductor manufacturing, where it is used to deposit dielectric films at low temperatures, ensuring compatibility with temperature-sensitive materials and processes.
-
Deposition Rates and Film Quality:
- CVD: While CVD can produce high-quality films, the high temperatures involved can sometimes lead to the formation of corrosive by-products or impurities in the film.
- PECVD: PECVD offers enhanced deposition rates and better control over film properties, such as density and uniformity, due to the use of plasma. This results in higher-quality films with fewer impurities.
-
Energy Efficiency:
- CVD: The high-temperature requirements of CVD make it less energy-efficient compared to PECVD, especially for large-scale or continuous processes.
- PECVD: By utilizing plasma, PECVD reduces the overall energy consumption of the deposition process, making it more efficient and cost-effective for many applications.
In summary, while both CVD and PECVD are valuable techniques for thin film deposition, PECVD offers distinct advantages in terms of lower temperature processing, enhanced deposition rates, and better film quality, particularly for applications involving heat-sensitive materials.
Summary Table:
Aspect | CVD | PECVD |
---|---|---|
Mechanism | Relies on thermal energy to drive chemical reactions. | Uses plasma to activate chemical reactions at lower temperatures. |
Temperature | Requires high temperatures (>500°C). | Operates at lower temperatures (<300°C). |
Applications | High-purity materials, tool coatings, and some semiconductors. | Semiconductor manufacturing, temperature-sensitive materials. |
Deposition Rates | Slower due to high-temperature requirements. | Faster due to plasma activation. |
Film Quality | High-quality films but may have impurities. | Higher-quality films with better control over density and uniformity. |
Energy Efficiency | Less energy-efficient due to high temperatures. | More energy-efficient and cost-effective. |
Ready to optimize your thin film deposition process? Contact our experts today for tailored solutions!