CVD (Chemical Vapor Deposition) and PVD (Physical Vapor Deposition) are two widely used techniques for depositing thin films or coatings onto substrates, but they differ significantly in their processes, materials, and applications. CVD involves chemical reactions between gaseous precursors and the substrate, resulting in thicker, rougher coatings that can be applied to a wide range of materials. PVD, on the other hand, uses physical vaporization of solid materials, producing thinner, smoother, and more durable coatings. The choice between CVD and PVD depends on factors such as coating thickness, temperature tolerance, and the specific requirements of the application.
Key Points Explained:
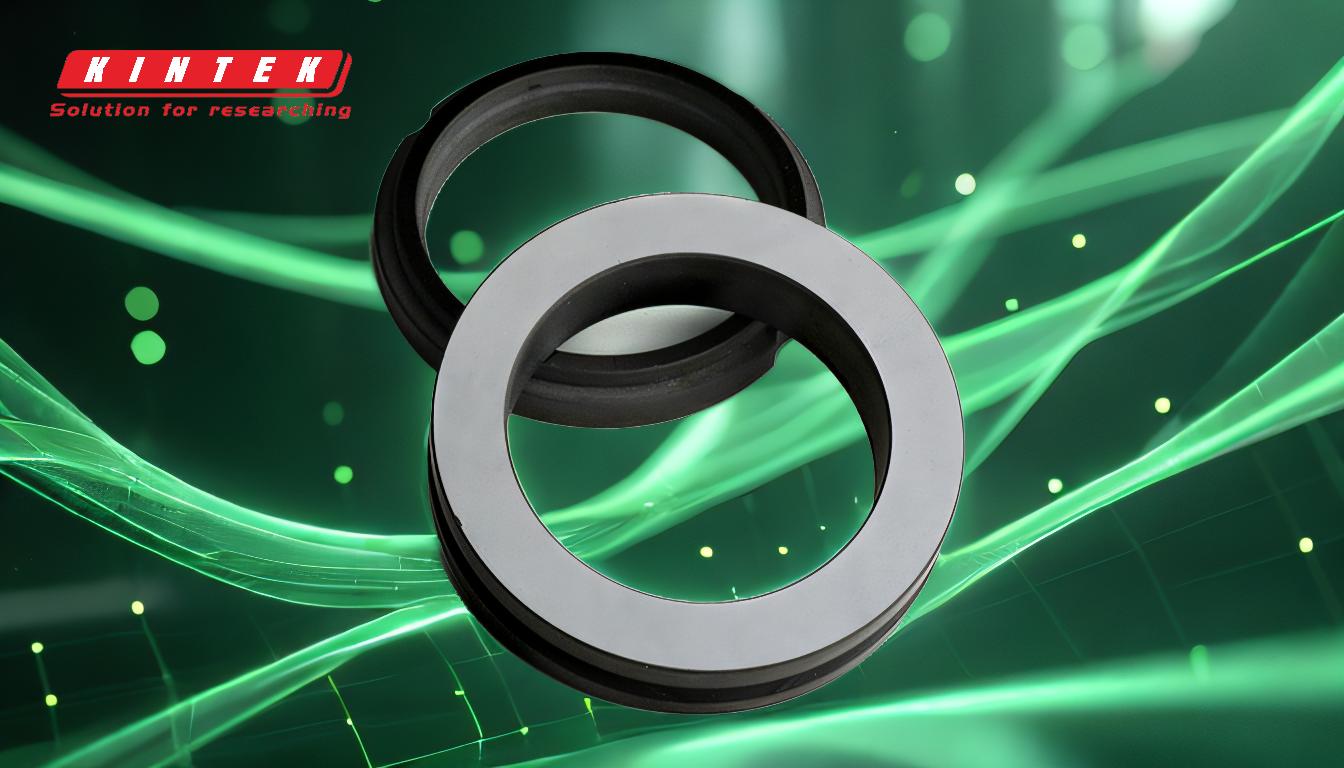
-
Deposition Process:
- CVD: CVD relies on chemical reactions between gaseous precursors and the substrate. The gases react at high temperatures (450°C to 1050°C) to form a solid coating on the substrate. This process is multidirectional, meaning the coating can be applied uniformly on complex geometries.
- PVD: PVD involves the physical vaporization of solid materials, which are then deposited onto the substrate. This process is line-of-sight, meaning the material is deposited directly onto the substrate without chemical interaction. PVD operates at lower temperatures (250°C to 450°C).
-
Coating Materials:
- CVD: CVD uses gaseous materials as precursors. These gases react chemically to form the coating, which can be thicker (10~20μm) and rougher compared to PVD coatings.
- PVD: PVD uses solid materials that are vaporized and then condensed onto the substrate. The resulting coatings are thinner (3~5μm), smoother, and more durable.
-
Temperature Requirements:
- CVD: CVD requires high temperatures (450°C to 1050°C) to facilitate the chemical reactions necessary for deposition. This high-temperature process can lead to tensile stress and fine cracks in the coating.
- PVD: PVD operates at lower temperatures (250°C to 450°C), which minimizes the risk of thermal damage to the substrate. The lower temperature also results in compressive stress during cooling, enhancing the coating's durability.
-
Coating Properties:
- CVD: CVD coatings are generally thicker and rougher, making them suitable for applications where a robust, wear-resistant surface is needed. However, the high processing temperature can limit the types of substrates that can be coated.
- PVD: PVD coatings are thinner, smoother, and more uniform, making them ideal for applications requiring precision and durability. The lower processing temperature allows for a wider range of substrate materials.
-
Applications:
- CVD: CVD is commonly used in applications requiring thick, wear-resistant coatings, such as in the semiconductor industry, cutting tools, and wear-resistant components.
- PVD: PVD is often used in applications requiring thin, durable, and smooth coatings, such as in the aerospace industry, medical devices, and decorative finishes.
-
Stress and Crack Formation:
- CVD: The high temperatures in CVD can lead to tensile stress and fine cracks in the coating, which may affect its performance in certain applications.
- PVD: PVD coatings typically have compressive stress, which enhances their durability and resistance to cracking.
In summary, the choice between CVD and PVD depends on the specific requirements of the application, including the desired coating thickness, temperature tolerance, and the types of materials involved. Both techniques have their unique advantages and limitations, making them suitable for different industrial applications.
Summary Table:
Aspect | CVD | PVD |
---|---|---|
Deposition Process | Chemical reactions between gases and substrate at high temperatures. | Physical vaporization of solid materials at lower temperatures. |
Coating Materials | Gaseous precursors; thicker (10~20μm), rougher coatings. | Solid materials; thinner (3~5μm), smoother, and more durable coatings. |
Temperature | High (450°C to 1050°C); may cause tensile stress and cracks. | Lower (250°C to 450°C); minimizes thermal damage and enhances durability. |
Coating Properties | Thicker, rougher, wear-resistant; limited by high-temperature tolerance. | Thinner, smoother, uniform; suitable for precision and durability. |
Applications | Semiconductor, cutting tools, wear-resistant components. | Aerospace, medical devices, decorative finishes. |
Stress Formation | Tensile stress; fine cracks may occur. | Compressive stress; enhances durability and crack resistance. |
Still unsure which coating technique is right for your application? Contact our experts today for personalized advice!