CVD (Chemical Vapor Deposition) and sputtering (a type of Physical Vapor Deposition, PVD) are both techniques used to deposit thin films onto substrates, but they differ significantly in their mechanisms, processes, and applications. CVD relies on chemical reactions between gaseous precursors to form thin films, while sputtering uses physical processes to vaporize and deposit material onto a substrate. CVD operates at higher temperatures and can coat complex geometries due to its non-line-of-sight nature, whereas sputtering is a lower-temperature process, making it suitable for temperature-sensitive materials. Additionally, CVD coatings generally exhibit superior adhesion due to chemical bonding, while sputtering is more limited in its applications but offers precise control over film composition and thickness.
Key Points Explained:
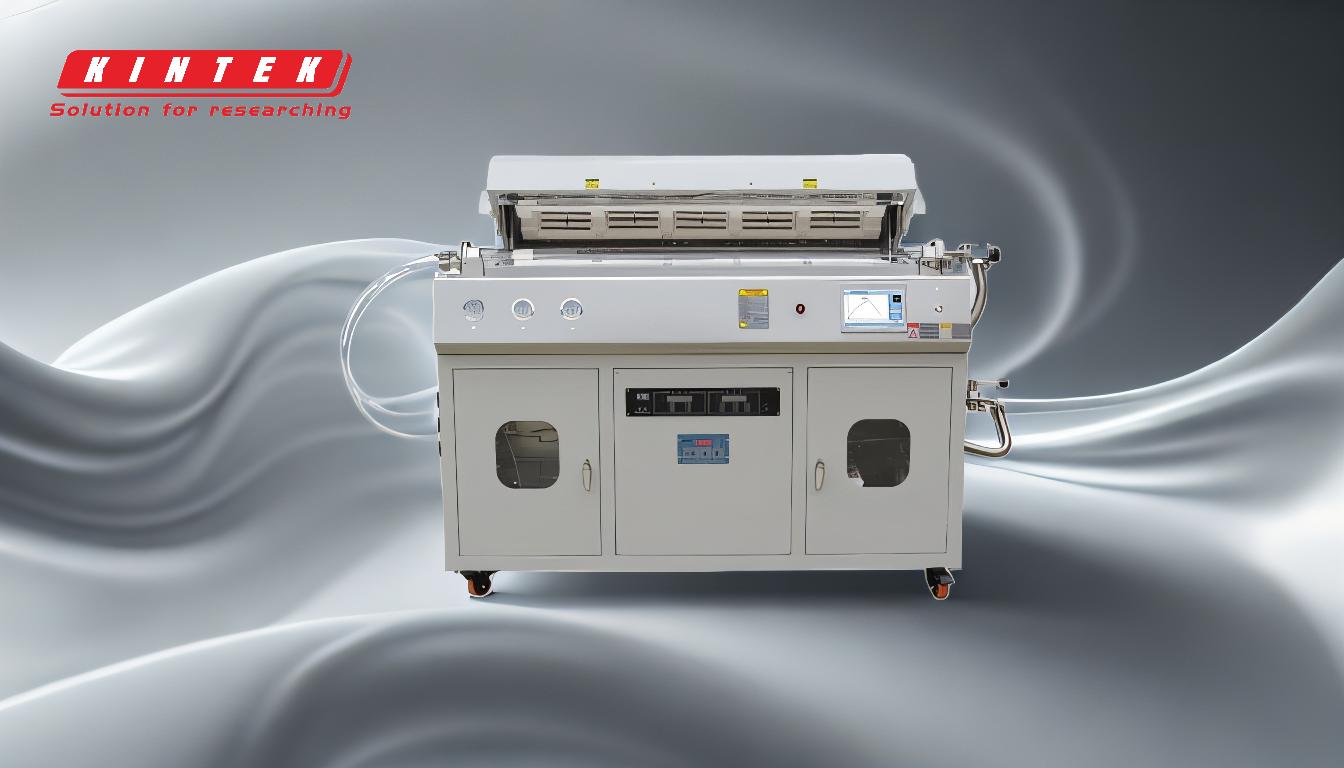
-
Mechanism of Deposition:
- CVD: Involves chemical reactions between gaseous precursors at the substrate surface to form a thin solid film. The process is driven by chemical reactions, often requiring high temperatures to activate the reactions.
- Sputtering: A physical process where atoms are ejected from a solid target material due to bombardment by high-energy ions. The ejected atoms then deposit onto the substrate to form a thin film. This process does not involve chemical reactions.
-
Temperature Requirements:
- CVD: Typically operates at higher temperatures, which can limit its use with temperature-sensitive materials. The high temperatures are necessary to activate the chemical reactions.
- Sputtering: Operates at relatively lower temperatures, making it suitable for substrates that cannot withstand high temperatures, such as plastics or certain semiconductors.
-
Coating Uniformity and Coverage:
- CVD: A non-line-of-sight process, meaning it can coat complex geometries, including threads, blind holes, and interior surfaces. This is because the gaseous precursors can reach and react on any exposed surface.
- Sputtering: A line-of-sight process, meaning it can only coat surfaces directly exposed to the sputtering target. This limits its ability to coat complex or hidden geometries uniformly.
-
Adhesion and Bonding:
- CVD: Coatings are chemically bonded to the substrate during the reaction, resulting in superior adhesion. This makes CVD coatings highly durable and resistant to delamination.
- Sputtering: Coatings are physically deposited onto the substrate, which may result in weaker adhesion compared to CVD. However, sputtering can still produce high-quality films with good adhesion, especially when combined with additional surface treatments.
-
Applications and Material Compatibility:
- CVD: Widely used in industries for creating organic and inorganic films on metals, semiconductors, and other materials. It is particularly useful for applications requiring high-purity films and complex geometries.
- Sputtering: More limited in its applications but is highly versatile for depositing a wide range of materials, including metals, alloys, and ceramics. It is often used in the production of optical coatings, semiconductor devices, and decorative finishes.
-
Process Complexity and Control:
- CVD: Generally more complex due to the need for precise control over gas flow, temperature, and chemical reactions. The process can be more challenging to scale up for large-scale production.
- Sputtering: Offers precise control over film composition and thickness, making it suitable for applications requiring high precision. The process is relatively simpler and easier to scale for industrial applications.
-
Environmental and Safety Considerations:
- CVD: Often involves the use of hazardous gases and high temperatures, requiring stringent safety measures and environmental controls.
- Sputtering: Typically involves fewer hazardous materials and operates at lower temperatures, making it a safer and more environmentally friendly option in many cases.
In summary, while both CVD and sputtering are essential techniques for thin film deposition, they are suited to different applications based on their unique characteristics. CVD excels in creating high-purity, chemically bonded films on complex geometries, whereas sputtering offers precise control and is better suited for temperature-sensitive materials and simpler geometries.
Summary Table:
Aspect | CVD | Sputtering |
---|---|---|
Mechanism | Chemical reactions between gaseous precursors | Physical process of ejecting atoms from a target |
Temperature | High temperatures required | Lower temperatures, suitable for sensitive materials |
Coating Uniformity | Non-line-of-sight, coats complex geometries | Line-of-sight, limited to exposed surfaces |
Adhesion | Superior due to chemical bonding | Physically deposited, may require additional treatments |
Applications | High-purity films, complex geometries | Optical coatings, semiconductors, decorative finishes |
Process Complexity | Complex, requires precise control | Simpler, easier to scale |
Safety | Involves hazardous gases and high temperatures | Fewer hazards, more environmentally friendly |
Need help choosing the right thin film deposition technique? Contact our experts today!