Electron beam evaporation and ion sputtering systems are both physical vapor deposition (PVD) techniques used to create thin films, but they differ significantly in their mechanisms, operational parameters, and applications. Electron beam evaporation uses a focused electron beam to heat and vaporize high-temperature materials, resulting in a high deposition rate and suitability for applications like solar panels and glass. Sputtering, on the other hand, involves bombarding a target material with energetic ions to eject atoms, which then deposit onto a substrate. Sputtering operates at lower temperatures, provides better adhesion and film homogeneity, and is ideal for complex substrates and high-purity thin films. Each method has distinct advantages depending on the specific requirements of the project.
Key Points Explained:
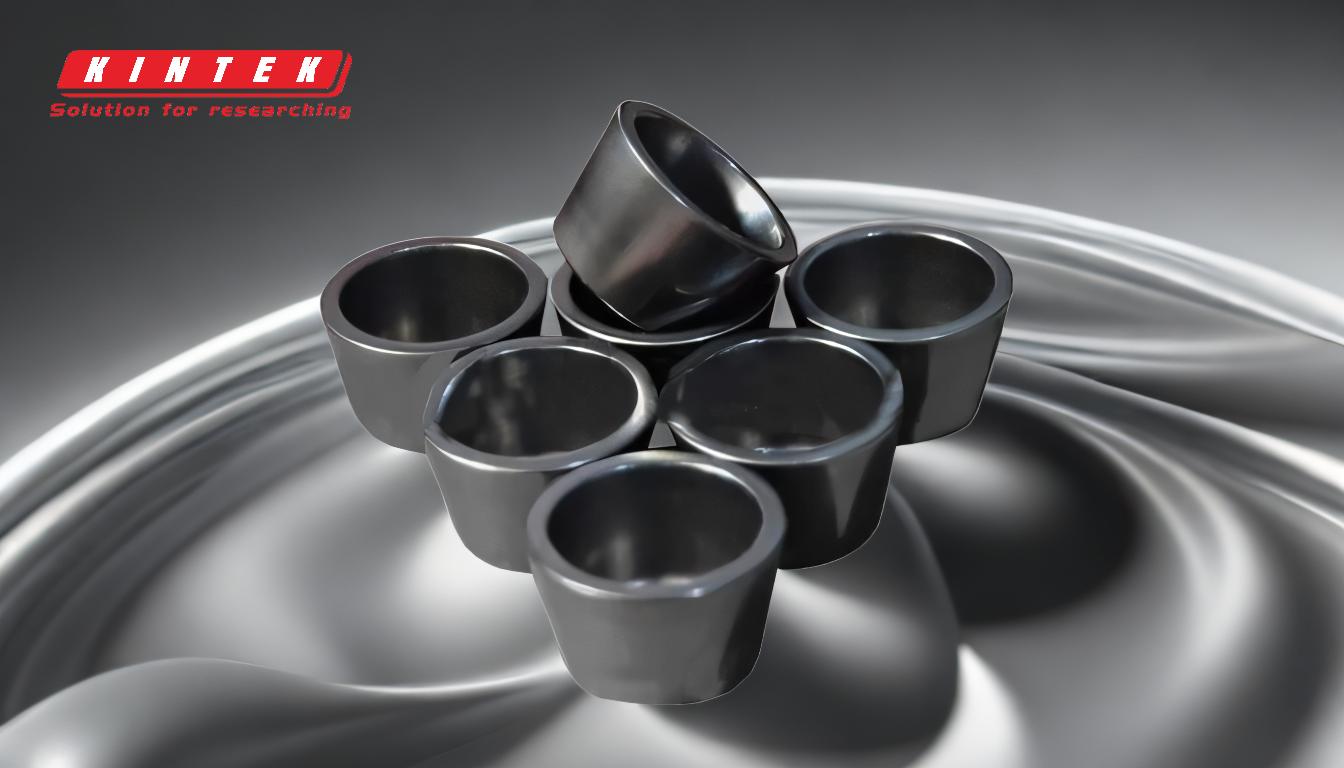
-
Mechanism of Deposition:
- Electron Beam Evaporation: Uses a focused electron beam to heat and vaporize the source material. The vaporized material condenses on the substrate to form a thin film.
- Ion Sputtering: Involves bombarding a target material with energetic ions (typically argon) in a plasma environment. The collision ejects atoms from the target, which then deposit onto the substrate.
-
Operational Environment:
- Electron Beam Evaporation: Requires a high vacuum environment to minimize contamination and ensure efficient vaporization.
- Ion Sputtering: Operates in a lower vacuum environment and often within a closed magnetic field to enhance ionization and deposition efficiency.
-
Deposition Rate:
- Electron Beam Evaporation: Offers a higher deposition rate, making it suitable for applications requiring rapid film formation.
- Ion Sputtering: Generally has a lower deposition rate, especially for dielectric materials, but provides better control over film properties.
-
Adhesion and Film Quality:
- Electron Beam Evaporation: Produces films with lower adhesion and less homogeneity, which may require post-deposition treatments.
- Ion Sputtering: Provides better adhesion, higher film homogeneity, and smaller grain sizes, resulting in higher-quality thin films.
-
Temperature Requirements:
- Electron Beam Evaporation: Requires high temperatures to vaporize the source material, which can limit its use with temperature-sensitive substrates.
- Ion Sputtering: Operates at lower temperatures, making it suitable for temperature-sensitive materials and complex substrates.
-
Scalability and Automation:
- Electron Beam Evaporation: Less scalable and harder to automate due to its reliance on high vacuum and precise electron beam control.
- Ion Sputtering: More scalable and easier to automate, making it ideal for large-scale production and industrial applications.
-
Applications:
- Electron Beam Evaporation: Commonly used in applications like solar panels, glass coatings, and optical films due to its high deposition rate.
- Ion Sputtering: Preferred for electrical and optical production, high-purity thin films, and coatings on complex substrates due to its superior film quality and adhesion.
-
Energy of Deposited Species:
- Electron Beam Evaporation: Produces lower-energy vapor species, which can result in less dense films.
- Ion Sputtering: Ejects higher-energy atoms, leading to denser and more adherent films.
-
Gas Absorption:
- Electron Beam Evaporation: Less prone to gas absorption due to the high vacuum environment.
- Ion Sputtering: More likely to absorb gases, which can affect film properties but also allows for reactive sputtering to create compound films.
-
Directionality of Atomized Particles:
- Electron Beam Evaporation: Produces a more dispersed vapor stream, which can lead to less directional deposition.
- Ion Sputtering: Ejects particles in a more directional manner, improving coverage on complex geometries.
In summary, the choice between electron beam evaporation and ion sputtering depends on the specific requirements of the project, such as deposition rate, film quality, substrate complexity, and scalability. Each method has its unique advantages and limitations, making them suitable for different applications in thin film deposition.
Summary Table:
Aspect | Electron Beam Evaporation | Ion Sputtering |
---|---|---|
Mechanism | Focused electron beam heats and vaporizes materials. | Energetic ions bombard target material to eject atoms. |
Operational Environment | High vacuum required. | Lower vacuum, often with a magnetic field. |
Deposition Rate | Higher deposition rate. | Lower deposition rate, better control over film properties. |
Adhesion & Film Quality | Lower adhesion, less homogeneity. | Better adhesion, higher homogeneity, smaller grain sizes. |
Temperature | High temperatures required, less suitable for sensitive substrates. | Lower temperatures, ideal for sensitive materials and complex substrates. |
Scalability | Less scalable, harder to automate. | More scalable, easier to automate for large-scale production. |
Applications | Solar panels, glass coatings, optical films. | Electrical/optical production, high-purity films, complex substrates. |
Energy of Deposited Atoms | Lower-energy vapor species, less dense films. | Higher-energy atoms, denser and more adherent films. |
Gas Absorption | Less prone to gas absorption. | More likely to absorb gases, enabling reactive sputtering. |
Directionality | Dispersed vapor stream, less directional. | More directional, better coverage on complex geometries. |
Need help choosing the right PVD technique for your project? Contact our experts today for personalized guidance!