Evaporation and deposition are two distinct processes used in thin-film fabrication, each with unique mechanisms and applications. Evaporation involves heating a material to its vaporization point, creating a vapor stream that condenses on a substrate to form a thin film. Deposition, on the other hand, encompasses a broader range of techniques, including physical vapor deposition (PVD) and chemical vapor deposition (CVD), where materials are transferred to a substrate through physical or chemical processes. The key differences lie in the mechanisms, materials used, and the resulting film properties, making each method suitable for specific applications in industries like semiconductors, optics, and coatings.
Key Points Explained:
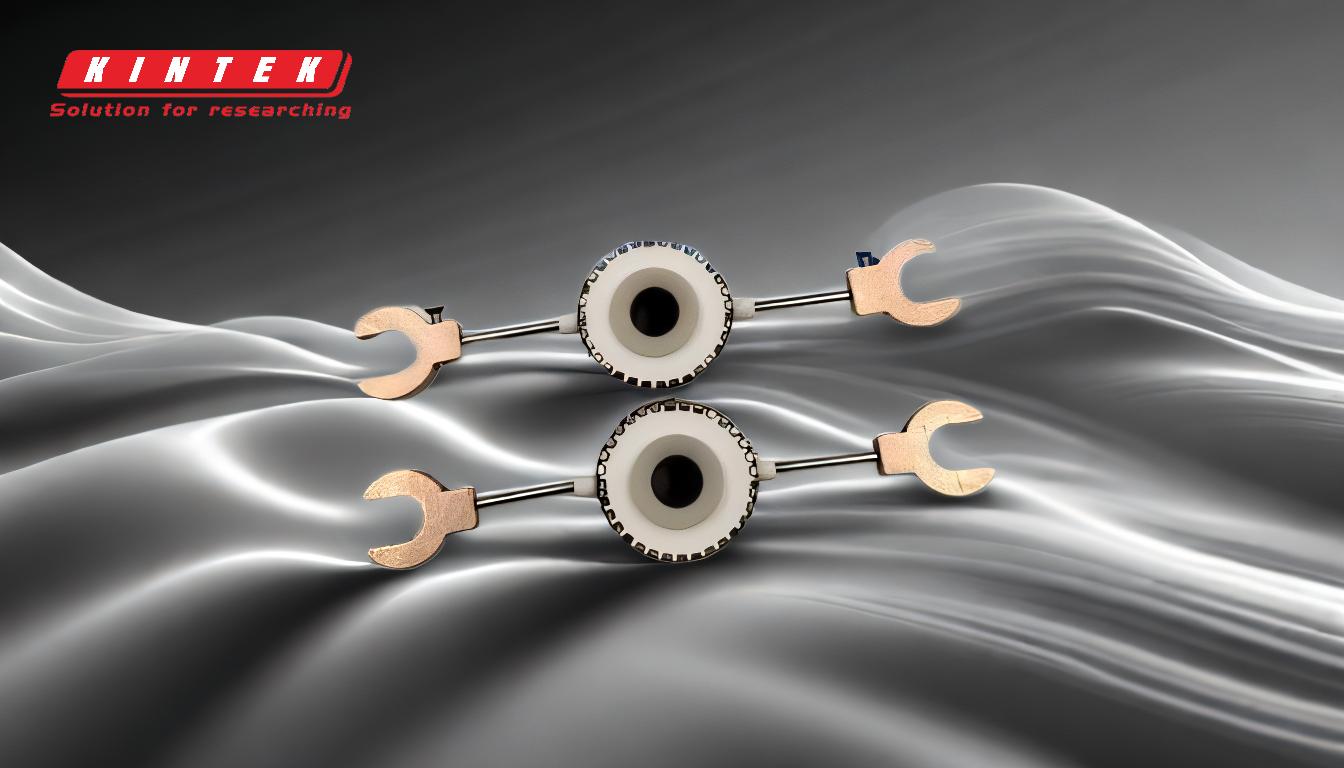
-
Mechanism of Evaporation:
- Evaporation involves heating a material until it vaporizes, creating a vapor stream that condenses on a cooler substrate.
- This process is typically used in physical vapor deposition (PVD) techniques, where the material is heated above its melting point to generate vapors.
- Thermal evaporation, for example, produces a robust vapor stream, enabling high deposition rates with short run times.
-
Mechanism of Deposition:
- Deposition is a broader term that includes both physical and chemical processes.
- Physical vapor deposition (PVD) involves the physical transfer of material, such as through sputtering or evaporation, where atoms or clusters are ejected and deposited on a substrate.
- Chemical vapor deposition (CVD) involves gaseous molecules reacting or decomposing on a hot surface to form stable solid products, which are then deposited on the substrate.
-
Material Transfer:
- In evaporation, the material is transferred purely through physical means, relying on the vaporization and condensation of the material.
- In deposition, especially in CVD, the material transfer involves chemical reactions, where gaseous precursors react on the substrate surface to form the desired film.
-
Deposition Rates:
- Evaporation techniques, such as thermal evaporation, generally offer higher deposition rates due to the robust vapor stream produced.
- Sputtering, a type of PVD, ejects single atoms or clusters at a time, resulting in lower deposition rates compared to evaporation.
-
Material and Process Variability:
- CVD processes are typically restricted to two active gases, limiting the types of materials that can be deposited.
- PVD methods, including evaporation and sputtering, offer more variability and can be used with a wider range of materials.
-
Applications:
- Evaporation is often used in applications requiring high-purity films, such as in the semiconductor industry.
- Deposition techniques, particularly CVD, are used in applications where complex chemical reactions are needed, such as in the production of graphene or other advanced materials.
Understanding these differences helps in selecting the appropriate method for specific applications, ensuring optimal film quality and performance.
Summary Table:
Aspect | Evaporation | Deposition |
---|---|---|
Mechanism | Heating material to vaporization point, condensing on a substrate. | Broader process including PVD (sputtering, evaporation) and CVD (chemical reactions). |
Material Transfer | Pure physical transfer via vaporization and condensation. | Physical (PVD) or chemical (CVD) transfer, involving reactions on the substrate. |
Deposition Rate | High deposition rates due to robust vapor streams. | Lower rates in sputtering; CVD rates depend on reaction kinetics. |
Material Variability | Works with a wide range of materials. | CVD limited to specific gases; PVD offers more material flexibility. |
Applications | High-purity films in semiconductors, optics, and coatings. | CVD for complex materials like graphene; PVD for versatile thin-film applications. |
Need help choosing the right thin-film fabrication method? Contact our experts today for tailored solutions!