Evaporation and electron beam lithography are two distinct processes used in thin-film deposition and microfabrication, respectively. Evaporation, specifically electron beam evaporation, is a physical vapor deposition (PVD) technique where a high-energy electron beam heats and vaporizes a target material, which then condenses onto a substrate to form a thin film. Electron beam lithography, on the other hand, is a nanofabrication technique that uses a focused electron beam to pattern a resist material, enabling the creation of extremely fine features on a substrate. While both processes involve electron beams, their purposes, mechanisms, and applications differ significantly.
Key Points Explained:
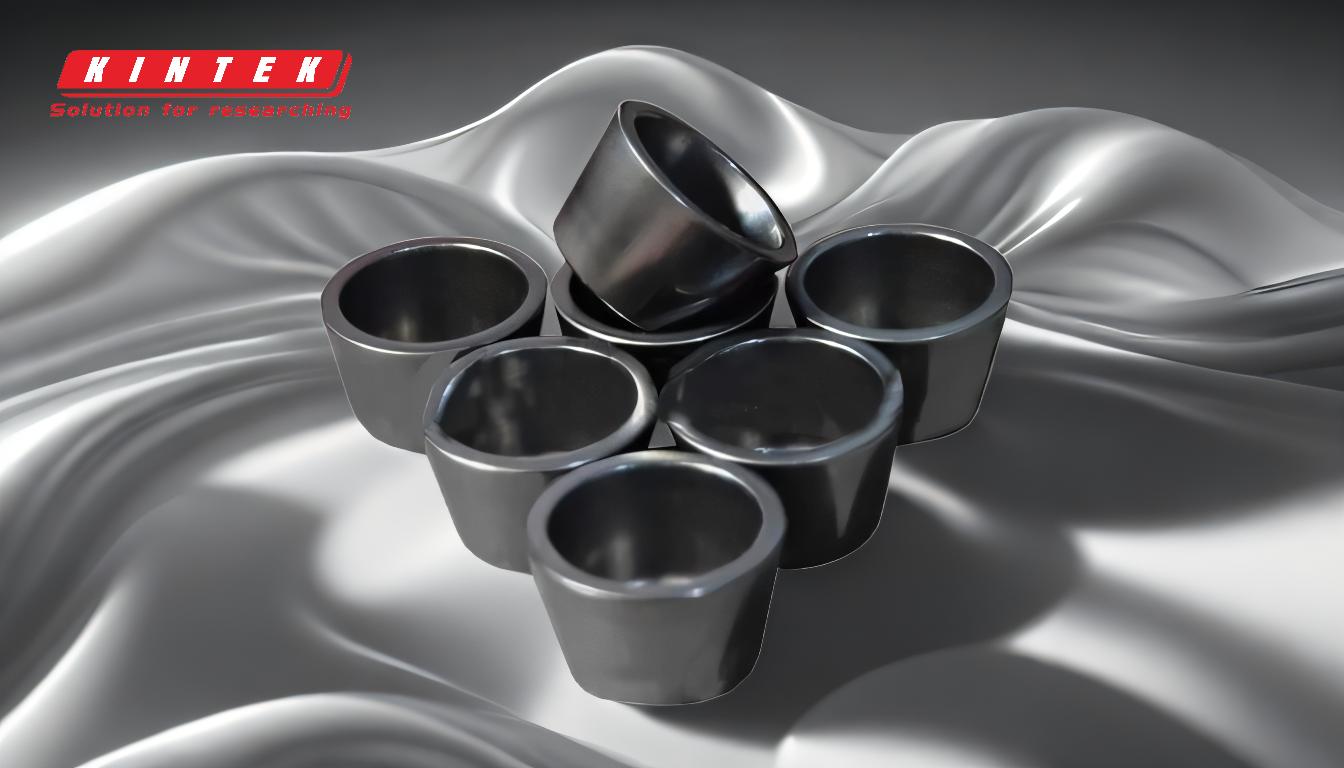
-
Purpose and Application:
- Evaporation: Used for depositing thin films of materials onto substrates, often in applications like optical coatings, semiconductor devices, and protective coatings.
- Electron Beam Lithography: Used for creating nanoscale patterns on substrates, essential in the fabrication of integrated circuits, photomasks, and nanodevices.
-
Mechanism:
-
Evaporation:
- Involves heating a target material using a high-energy electron beam, causing it to vaporize.
- The vaporized material then condenses onto a substrate to form a thin film.
- The process occurs in a high vacuum to minimize contamination and ensure a clean deposition.
-
Electron Beam Lithography:
- Uses a focused electron beam to expose a resist material coated on a substrate.
- The exposed resist undergoes a chemical change, allowing it to be developed to create a pattern.
- The pattern can then be transferred to the underlying substrate through etching or deposition processes.
-
Evaporation:
-
Equipment and Setup:
-
Evaporation:
- Requires an electron beam evaporation system, including an electron gun, a vacuum chamber, and a substrate holder.
- The electron gun generates a high-energy beam that is focused onto the target material.
-
Electron Beam Lithography:
- Requires an electron beam lithography system, including an electron beam column, a vacuum chamber, and a stage for precise substrate positioning.
- The system must also include a resist coating and development setup.
-
Evaporation:
-
Material Considerations:
-
Evaporation:
- Suitable for a wide range of materials, including metals, oxides, and high-melting-point materials.
- The choice of material depends on the desired properties of the thin film, such as conductivity, transparency, or durability.
-
Electron Beam Lithography:
- Primarily involves resist materials that are sensitive to electron exposure.
- The resist material must be carefully selected based on the desired resolution, sensitivity, and etch resistance.
-
Evaporation:
-
Process Parameters:
-
Evaporation:
- Key parameters include the electron beam energy, deposition rate, substrate temperature, and vacuum level.
- The deposition rate and film uniformity are critical for achieving the desired film properties.
-
Electron Beam Lithography:
- Key parameters include the electron beam energy, dose, spot size, and scan speed.
- The resolution and pattern fidelity are highly dependent on these parameters.
-
Evaporation:
-
Advantages and Limitations:
-
Evaporation:
- Advantages: High deposition rate, ability to deposit high-purity films, and compatibility with high-temperature materials.
- Limitations: Limited scalability, complex and costly equipment, and potential for contamination if the vacuum is not maintained.
-
Electron Beam Lithography:
- Advantages: Extremely high resolution (down to a few nanometers), ability to create complex patterns, and compatibility with a wide range of substrates.
- Limitations: Slow process speed, high cost of equipment and operation, and sensitivity to environmental factors like vibration and temperature.
-
Evaporation:
In summary, while both evaporation and electron beam lithography utilize electron beams, they serve different purposes in the realm of material science and microfabrication. Evaporation is focused on depositing thin films, whereas electron beam lithography is aimed at creating intricate patterns at the nanoscale. Understanding these differences is crucial for selecting the appropriate technique for a given application.
Summary Table:
Aspect | Evaporation | Electron Beam Lithography |
---|---|---|
Purpose | Deposits thin films on substrates | Creates nanoscale patterns on substrates |
Mechanism | Vaporizes target material with an electron beam, condenses onto substrate | Exposes resist material with a focused electron beam, develops patterns |
Applications | Optical coatings, semiconductor devices, protective coatings | Integrated circuits, photomasks, nanodevices |
Equipment | Electron gun, vacuum chamber, substrate holder | Electron beam column, vacuum chamber, resist coating/development setup |
Materials | Metals, oxides, high-melting-point materials | Electron-sensitive resist materials |
Advantages | High deposition rate, high-purity films, high-temperature compatibility | High resolution, complex patterns, wide substrate compatibility |
Limitations | Limited scalability, costly equipment, contamination risks | Slow process, high cost, sensitivity to environmental factors |
Need help choosing the right technique for your project? Contact our experts today!