The primary difference between fast and slow biomass pyrolysis lies in the process conditions, reaction times, and the resulting products. Slow pyrolysis is a long-duration process (several hours) that primarily produces biochar, while fast pyrolysis is a rapid process (completed in seconds) that yields a higher proportion of bio-oil (60%) alongside biochar (20%) and syngas (20%). Fast pyrolysis operates at higher temperatures, requires precise control of heating rates, and involves rapid cooling of vapors, making it more efficient for biofuel production. In contrast, slow pyrolysis is more suited for biochar production, with a lower energy output relative to input.
Key Points Explained:
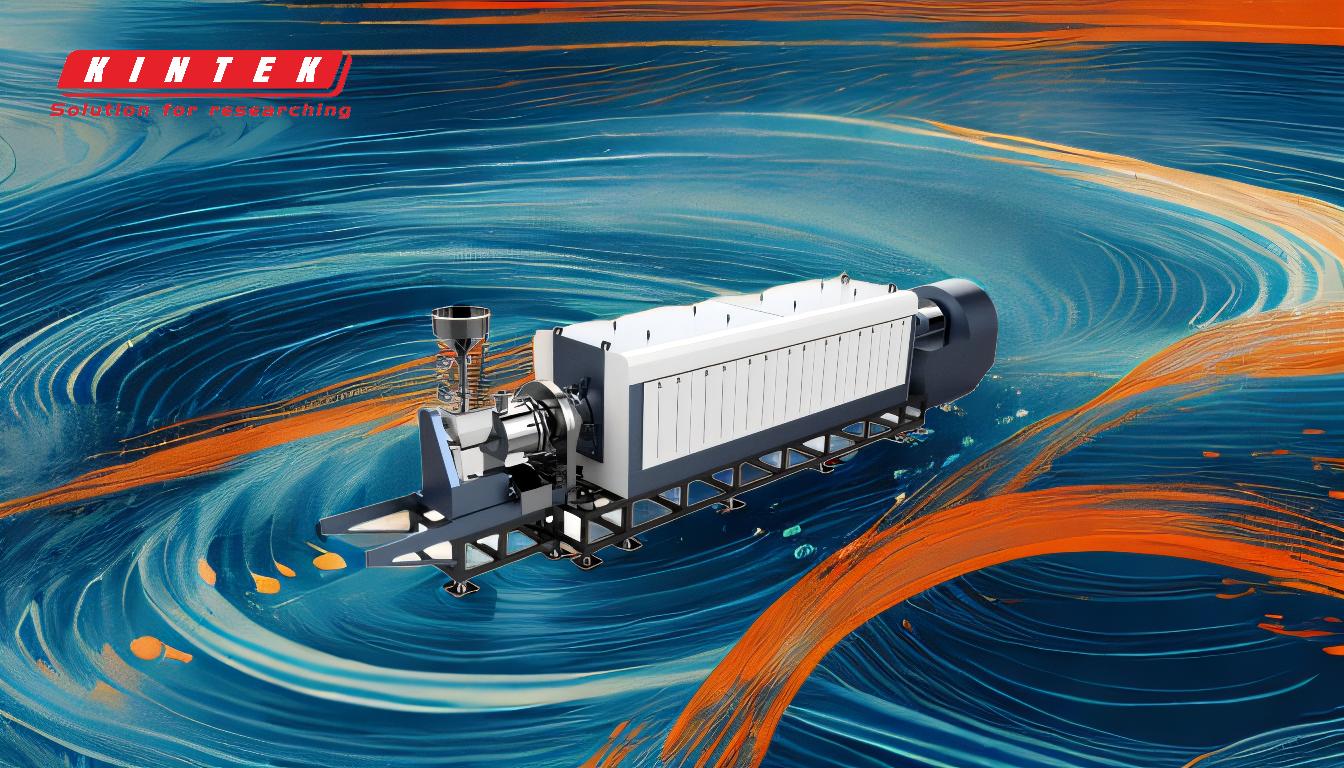
-
Reaction Time and Process Duration:
- Slow Pyrolysis: Takes several hours to complete, allowing for a more gradual decomposition of biomass. This extended duration favors the formation of biochar.
- Fast Pyrolysis: Completes in seconds (residence time of around 5 seconds), making it a much faster process. The rapid heating and cooling prevent the biomass from fully decomposing into char, resulting in higher yields of bio-oil and syngas.
-
Primary Products:
- Slow Pyrolysis: Primarily produces biochar, a solid carbon-rich material used for soil amendment, carbon sequestration, and as a fuel source.
- Fast Pyrolysis: Yields a mix of products, with bio-oil being the dominant product (60%), followed by biochar (20%) and syngas (20%). Bio-oil is a liquid fuel that can be further refined, while syngas is a gaseous mixture used for energy generation.
-
Temperature and Heating Rates:
- Slow Pyrolysis: Operates at lower temperatures and slower heating rates, which favor the formation of biochar. The process is less energy-intensive but also less efficient in terms of energy output.
- Fast Pyrolysis: Requires very high heating rates and controlled reaction temperatures around 500°C. The rapid heating and cooling processes are critical for maximizing bio-oil production.
-
Energy Efficiency:
- Slow Pyrolysis: Requires more energy input relative to its energy output, making it less efficient for biofuel production. However, it is highly effective for producing biochar.
- Fast Pyrolysis: Requires less energy input relative to its energy output, making it more efficient for biofuel production. The high yield of bio-oil and syngas makes it a preferred method for generating renewable energy.
-
Feedstock Preparation:
- Slow Pyrolysis: Can handle a wider range of feedstock sizes and types, as the process is less sensitive to particle size.
- Fast Pyrolysis: Requires finely ground feed to ensure rapid and uniform heating. The small particle size is crucial for achieving the high heat transfer rates needed for fast pyrolysis.
-
Applications:
- Slow Pyrolysis: Best suited for applications where biochar is the desired product, such as agriculture (soil improvement) and carbon sequestration.
- Fast Pyrolysis: Ideal for applications requiring liquid biofuels (bio-oil) and syngas, such as renewable energy production and industrial fuel applications.
-
Process Control and Complexity:
- Slow Pyrolysis: Simpler to control due to the slower reaction rates and lower temperatures. It is less demanding in terms of equipment and process control.
- Fast Pyrolysis: More complex and requires precise control of heating rates, reaction temperatures, and rapid cooling of pyrolysis vapors. This complexity is necessary to maximize bio-oil yield and ensure process efficiency.
In summary, the choice between fast and slow pyrolysis depends on the desired end products and the specific application. Slow pyrolysis is ideal for biochar production, while fast pyrolysis is more efficient for generating bio-oil and syngas, making it a better option for renewable energy production.
Summary Table:
Aspect | Slow Pyrolysis | Fast Pyrolysis |
---|---|---|
Reaction Time | Several hours | Seconds (residence time ~5 seconds) |
Primary Products | Biochar (dominant) | Bio-oil (60%), Biochar (20%), Syngas (20%) |
Temperature | Lower temperatures, slower heating rates | High temperatures (~500°C), rapid heating and cooling |
Energy Efficiency | Less efficient for biofuel production, better for biochar | More efficient for biofuel production |
Feedstock Preparation | Handles a wide range of sizes and types | Requires finely ground feed |
Applications | Agriculture (soil improvement), carbon sequestration | Renewable energy production, industrial fuel applications |
Process Complexity | Simpler to control, less demanding equipment | Complex, requires precise control of heating rates and cooling |
Ready to optimize your biomass conversion process? Contact us today to learn more about fast and slow pyrolysis solutions!