Gas brazing and induction brazing are two distinct methods used in the brazing process, each with its own set of advantages, limitations, and applications. Gas brazing typically involves the use of a flame generated by a gas torch to heat the filler metal and base materials, allowing the filler metal to flow and form a joint. Induction brazing, on the other hand, uses electromagnetic induction to generate heat directly within the workpiece, offering a more localized and controlled heating process. The choice between these methods depends on factors such as the materials being joined, the required precision, production volume, and cost considerations.
Key Points Explained:
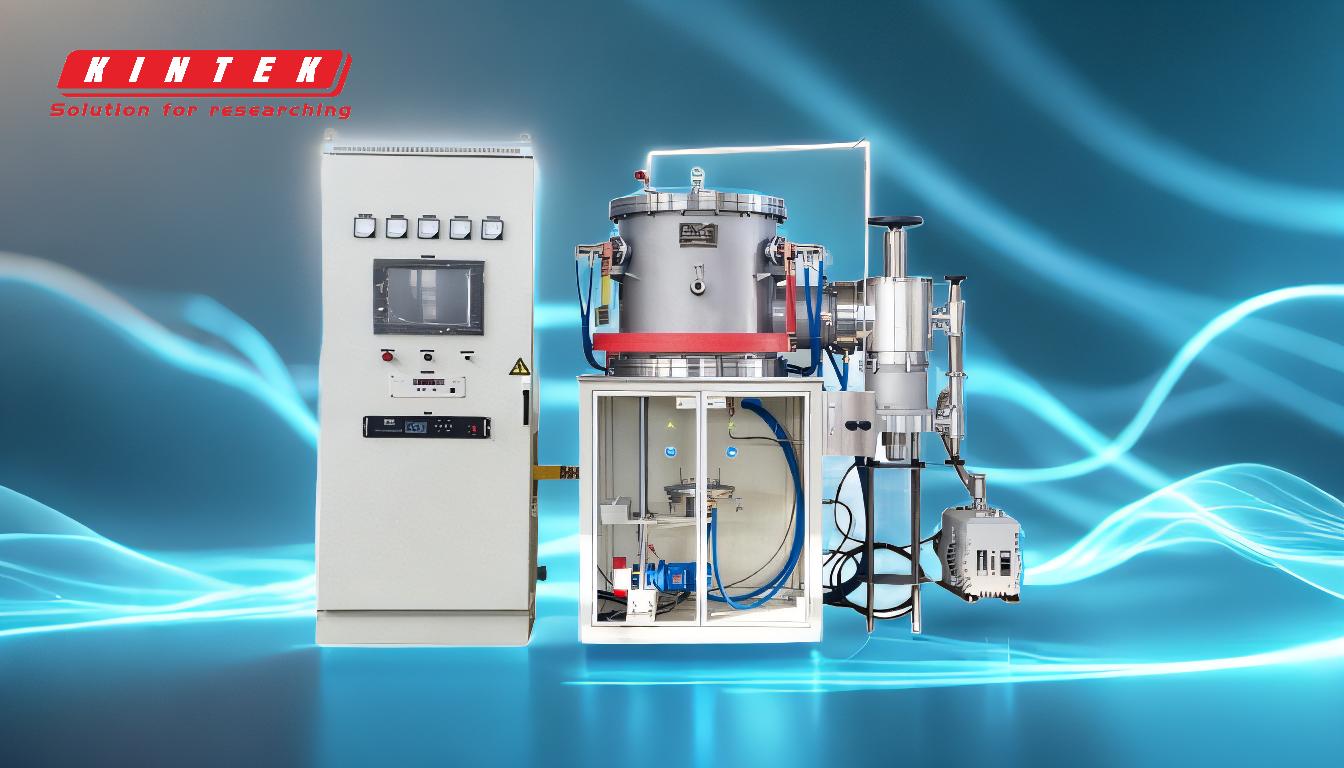
-
Heating Mechanism:
- Gas Brazing: Utilizes a flame produced by a gas torch (often using oxy-acetylene or propane) to heat the workpiece and filler metal. The heat is applied externally, which can lead to a broader heat-affected zone.
- Induction Brazing: Employs electromagnetic induction to generate heat directly within the workpiece. This method provides localized heating, reducing the heat-affected zone and allowing for precise temperature control.
-
Heat Control and Precision:
- Gas Brazing: While effective, gas brazing can be less precise due to the external application of heat. The flame can cause uneven heating, especially in complex or delicate parts.
- Induction Brazing: Offers superior control over the heating process, as the heat is generated internally within the workpiece. This allows for precise temperature management, making it ideal for applications requiring high accuracy and repeatability.
-
Productivity and Speed:
- Gas Brazing: Generally slower compared to induction brazing, especially for large or complex assemblies. The process may require more manual intervention, which can affect productivity.
- Induction Brazing: Typically faster, as the heating process is more efficient and can be automated. This results in higher productivity, particularly in high-volume production settings.
-
Quality of the Brazed Joint:
- Gas Brazing: The quality of the joint can be influenced by the skill of the operator and the uniformity of the heat application. There is a higher risk of oxidation and contamination due to exposure to the flame.
- Induction Brazing: Produces cleaner and more consistent joints due to the controlled heating environment. The localized heating minimizes oxidation and contamination, resulting in stronger and more reliable joints.
-
Cost Considerations:
- Gas Brazing: Generally more cost-effective in terms of initial equipment investment. However, the ongoing costs of gas and the potential for higher scrap rates due to inconsistent heating can add up.
- Induction Brazing: Higher initial investment in equipment, but the process can be more cost-efficient in the long run due to reduced material waste, lower energy consumption, and higher productivity.
-
Applications and Suitability:
- Gas Brazing: Suitable for a wide range of applications, including repair work, small-scale production, and situations where portability is important. It is often used in industries such as HVAC, plumbing, and automotive repair.
- Induction Brazing: Ideal for high-precision applications, mass production, and industries requiring high-quality joints, such as aerospace, electronics, and medical device manufacturing. It is also preferred for brazing dissimilar metals and materials with different thermal conductivities.
-
Environmental and Safety Considerations:
- Gas Brazing: Involves the use of flammable gases, which requires careful handling and proper ventilation to ensure safety. The process can also produce fumes and emissions that need to be managed.
- Induction Brazing: Generally safer, as it does not involve open flames or combustible gases. The process is cleaner, with minimal emissions, making it more environmentally friendly.
In summary, the choice between gas brazing and induction brazing depends on the specific requirements of the application, including the desired quality, precision, production volume, and budget. Gas brazing is more versatile and cost-effective for smaller-scale or less critical applications, while induction brazing offers superior control, efficiency, and quality for high-precision and high-volume production.
Summary Table:
Aspect | Gas Brazing | Induction Brazing |
---|---|---|
Heating Mechanism | Flame from gas torch (oxy-acetylene or propane) heats externally. | Electromagnetic induction generates heat internally within the workpiece. |
Precision | Less precise; uneven heating in complex parts. | Highly precise; localized heating for accurate temperature control. |
Productivity | Slower; manual intervention required. | Faster; efficient and automated for high-volume production. |
Joint Quality | Risk of oxidation and contamination; operator-dependent. | Cleaner, consistent joints; minimal oxidation and contamination. |
Cost | Lower initial cost; higher ongoing gas and scrap costs. | Higher initial investment; cost-efficient long-term due to reduced waste. |
Applications | HVAC, plumbing, automotive repair; portable and versatile. | Aerospace, electronics, medical devices; high-precision and mass production. |
Safety & Environment | Flammable gases; requires ventilation; produces fumes. | Safer; no open flames; minimal emissions and environmentally friendly. |
Still unsure which brazing method is best for your needs? Contact our experts today for personalized advice!