Graphite Furnace Atomic Absorption Spectroscopy (GFAAS) and Flame Atomic Absorption Spectroscopy (FAAS) are both techniques used to measure the concentration of elements in a sample. The primary difference lies in their atomization methods: FAAS uses a flame to atomize the sample, while GFAAS employs a graphite furnace. This distinction impacts sensitivity, sample size requirements, and application suitability. FAAS is generally faster and simpler, making it suitable for routine analysis of higher-concentration samples. GFAAS, on the other hand, offers higher sensitivity and is better suited for trace-level analysis or when sample volumes are limited.
Key Points Explained:
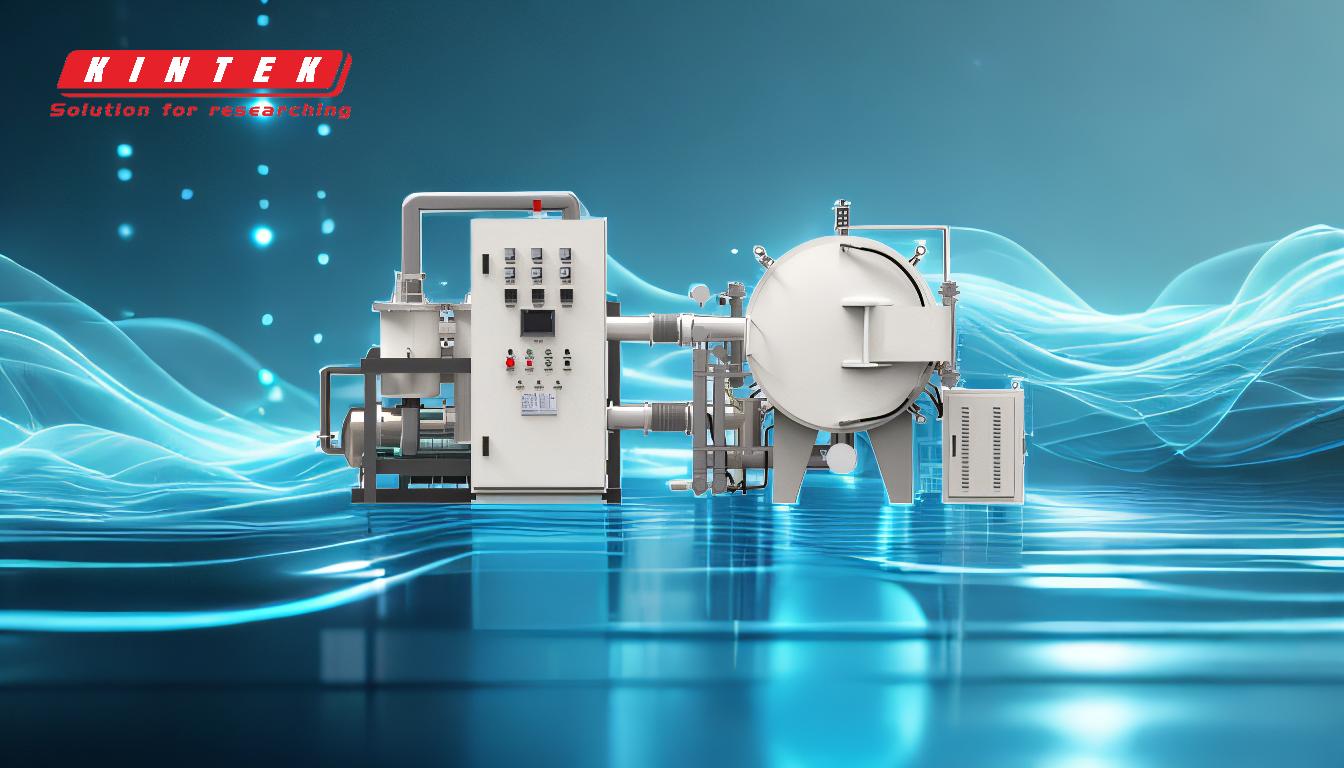
-
Atomization Method:
- FAAS: Uses a flame (typically air-acetylene or nitrous oxide-acetylene) to atomize the sample. The flame heats the sample to high temperatures, breaking it down into free atoms.
- GFAAS: Utilizes a graphite furnace to atomize the sample. The furnace heats the sample in stages, allowing for precise control over the atomization process.
-
Sensitivity:
- FAAS: Suitable for detecting elements at higher concentrations (typically in the ppm range). It is less sensitive compared to GFAAS.
- GFAAS: Highly sensitive, capable of detecting elements at much lower concentrations (in the ppb or even ppt range). This makes it ideal for trace analysis.
-
Sample Size:
- FAAS: Requires larger sample volumes (typically milliliters) due to the nature of flame atomization.
- GFAAS: Can analyze much smaller sample volumes (microliters), making it suitable for samples with limited availability.
-
Analysis Speed:
- FAAS: Faster analysis, as the flame atomization process is relatively quick. It is often used for high-throughput routine analysis.
- GFAAS: Slower due to the stepwise heating process in the graphite furnace. However, the slower process allows for better control and higher sensitivity.
-
Applications:
- FAAS: Commonly used for routine analysis in environmental, clinical, and industrial settings where higher concentrations of elements are expected.
- GFAAS: Preferred for specialized applications requiring high sensitivity, such as trace metal analysis in biological samples, environmental monitoring, and forensic analysis.
-
Cost and Maintenance:
- FAAS: Generally less expensive to purchase and maintain. The flame system is simpler and requires less frequent maintenance.
- GFAAS: More expensive due to the complexity of the graphite furnace system. It also requires more frequent maintenance and careful handling to avoid contamination.
-
Interferences:
- FAAS: More prone to matrix interferences due to the high temperatures and rapid atomization process in the flame.
- GFAAS: Less prone to matrix interferences, as the stepwise heating process can help to separate and minimize interferences.
In summary, the choice between FAAS and GFAAS depends on the specific analytical requirements, including the concentration of the analyte, sample volume, and the need for sensitivity. FAAS is more suitable for routine analysis of higher-concentration samples, while GFAAS is ideal for trace-level analysis and situations where sample volume is limited.
Summary Table:
Feature | FAAS | GFAAS |
---|---|---|
Atomization Method | Flame (air-acetylene or nitrous oxide-acetylene) | Graphite furnace |
Sensitivity | Lower (ppm range) | Higher (ppb or ppt range) |
Sample Size | Larger (milliliters) | Smaller (microliters) |
Analysis Speed | Faster | Slower |
Applications | Routine analysis (environmental, clinical, industrial) | Trace-level analysis (biological, environmental, forensic) |
Cost and Maintenance | Less expensive, simpler maintenance | More expensive, frequent maintenance |
Interferences | More prone to matrix interferences | Less prone to matrix interferences |
Need help choosing between GFAAS and FAAS? Contact our experts today for personalized guidance!