Cold isostatic pressing (CIP) and hot isostatic pressing (HIP) are two distinct processes used in material densification and consolidation, each with unique applications and benefits. CIP is performed at or near room temperature using a liquid medium to apply uniform pressure, making it ideal for forming large or complex parts that require further sintering. HIP, on the other hand, combines high temperature and pressure to achieve near-theoretical density, making it suitable for high-performance applications like aerospace and medical implants. While CIP is cost-effective for initial part formation, HIP ensures superior material properties and density, albeit at a higher cost.
Key Points Explained:
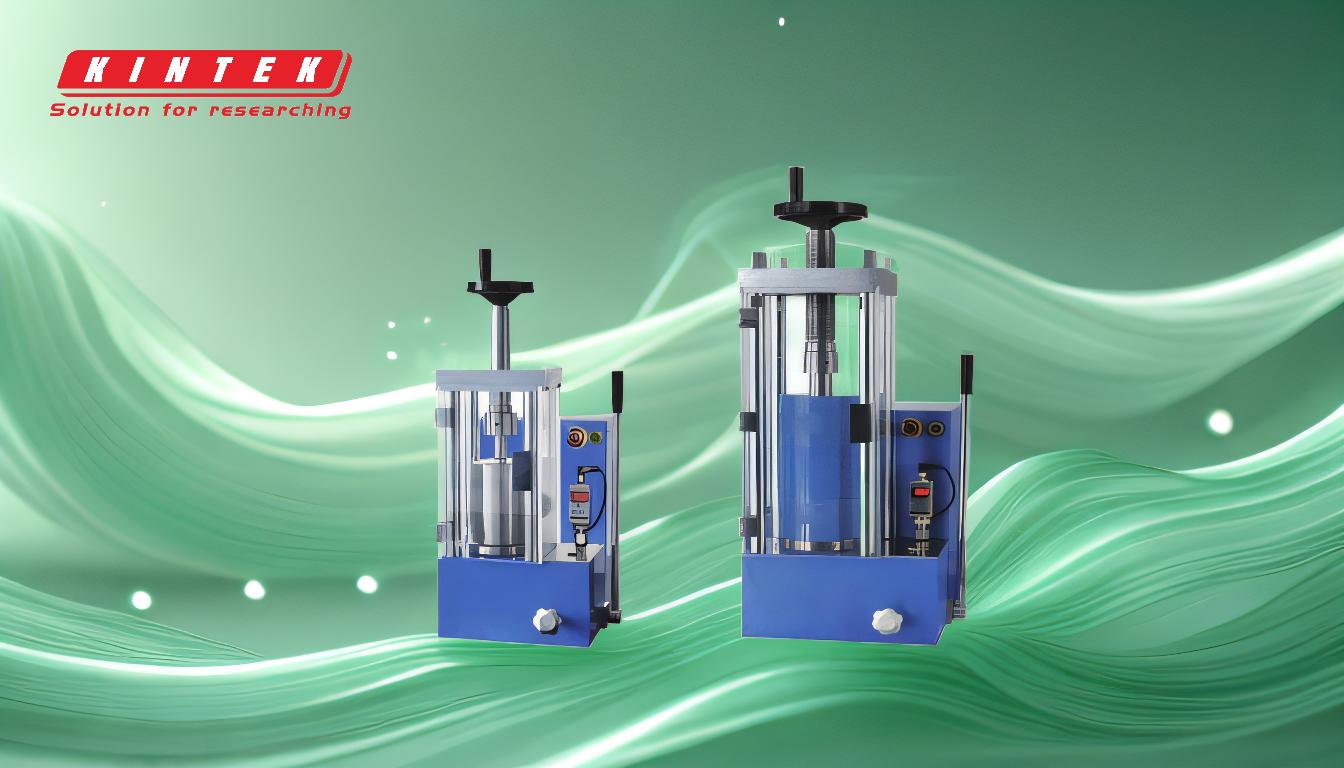
-
Temperature Differences:
- Cold Isostatic Pressing (CIP): Operates at or slightly above room temperature, typically below 93°C. It uses a liquid medium like water, oil, or glycol to apply uniform pressure.
- Hot Isostatic Pressing (HIP): Conducted at elevated temperatures, often exceeding 1000°C, combined with high pressure to achieve densification through solid-state diffusion.
-
Process Applications:
- CIP: Primarily used for forming "green" parts that require further sintering. It is ideal for large or complex components where initial costs must be minimized.
- HIP: Used for densification and consolidation of materials, particularly in high-performance applications like aerospace, medical implants, and engineered ceramics. It ensures near-theoretical density and minimizes voids.
-
Material Densification:
- CIP: Produces parts with sufficient strength for handling but requires sintering to achieve final density. Densities typically range from 65% to 99%.
- HIP: Achieves densities exceeding 99%, often reaching 100% theoretical density, ensuring uniform material properties and eliminating porosity.
-
Cost and Complexity:
- CIP: More cost-effective for initial part formation, especially for large or complex geometries. It is less energy-intensive due to lower operating temperatures.
- HIP: More expensive due to the need for high temperatures and pressures, but it delivers superior material properties, making it suitable for critical applications.
-
Equipment and Medium:
- Both processes use high-pressure gases or liquids to apply uniform pressure. CIP relies on liquid media, while HIP uses heated gases to achieve the desired temperature and pressure conditions.
-
Applications in Industry:
- CIP: Commonly used in industries where cost-effective initial part formation is critical, such as automotive and general manufacturing.
- HIP: Preferred in industries requiring high-performance materials, such as aerospace, medical devices, and advanced ceramics.
By understanding these key differences, equipment and consumable purchasers can make informed decisions based on the specific requirements of their projects, balancing cost, material properties, and application needs.
Summary Table:
Aspect | Cold Isostatic Pressing (CIP) | Hot Isostatic Pressing (HIP) |
---|---|---|
Temperature | At or near room temperature (below 93°C) | Elevated temperatures (often exceeding 1000°C) |
Pressure Medium | Liquid medium (water, oil, or glycol) | Heated gases |
Material Density | 65% to 99% (requires sintering for final density) | Exceeds 99%, often reaching 100% theoretical density |
Applications | Forming "green" parts, large/complex components, cost-effective initial part formation | High-performance applications (aerospace, medical implants, engineered ceramics) |
Cost | Cost-effective for initial part formation | Higher cost due to high temperatures and pressures |
Industries | Automotive, general manufacturing | Aerospace, medical devices, advanced ceramics |
Need help choosing the right isostatic pressing process for your project? Contact our experts today for personalized guidance!