Ion beam sputtering (IBS) and magnetron sputtering are both physical vapor deposition (PVD) techniques used to deposit thin films, but they differ significantly in their mechanisms, applications, and operational characteristics. Ion beam sputtering involves a separate ion source that generates a focused beam of ions to sputter target material onto a substrate, without requiring a plasma between the target and substrate. This method is versatile, allowing the use of both conductive and non-conductive materials. Magnetron sputtering, on the other hand, uses a magnetic field to confine plasma near the target, enabling high deposition rates and efficient coating of large substrates. Below, we explore the key differences between these two techniques in detail.
Key Points Explained:
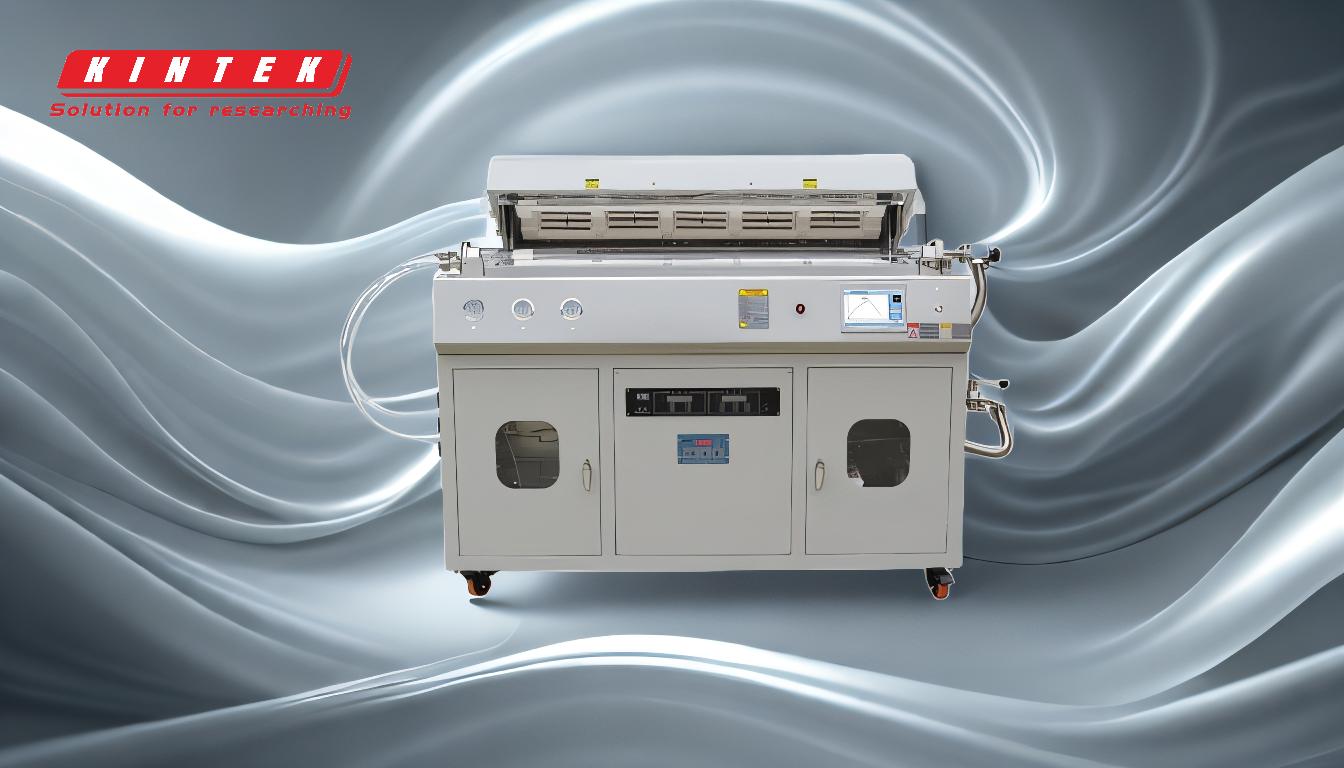
-
Mechanism of Sputtering:
-
Ion Beam Sputtering (IBS):
- In IBS, the ion source generates a focused beam of ions (e.g., argon ions) that is directed at the target material. The ions sputter atoms from the target, which then deposit onto the substrate.
- The plasma is confined within the ion source, meaning there is no plasma between the target and substrate. This separation allows for precise control over the sputtering process.
- Since the ion beam is neutralized before reaching the substrate, IBS can be used with both conductive and non-conductive materials without the risk of electrical damage.
-
Magnetron Sputtering:
- Magnetron sputtering uses a magnetic field to trap electrons near the target surface, creating a high-density plasma. This plasma ionizes the inert gas (e.g., argon), which then bombards the target material, causing sputtering.
- The plasma is present between the target and substrate, which can lead to higher deposition rates but may also introduce challenges with substrate heating or damage.
-
Ion Beam Sputtering (IBS):
-
Target and Substrate Compatibility:
-
Ion Beam Sputtering:
- IBS does not require a biased target, making it suitable for sensitive, conductive, and non-conductive materials. This flexibility is particularly useful for depositing materials like oxides or polymers.
- The absence of plasma between the target and substrate reduces the risk of substrate damage, making IBS ideal for delicate or temperature-sensitive substrates.
-
Magnetron Sputtering:
- Magnetron sputtering typically requires a conductive target material due to the need for a biased cathode. However, reactive magnetron sputtering can be used to deposit non-conductive materials by introducing reactive gases (e.g., oxygen or nitrogen) into the chamber.
- The presence of plasma near the substrate can cause heating or damage, which may limit its use for certain sensitive applications.
-
Ion Beam Sputtering:
-
Deposition Rate and Efficiency:
-
Ion Beam Sputtering:
- IBS generally has a lower deposition rate compared to magnetron sputtering due to the focused nature of the ion beam and the absence of a high-density plasma.
- However, IBS offers excellent film quality, with high density, low roughness, and precise control over film thickness.
-
Magnetron Sputtering:
- Magnetron sputtering is known for its high deposition rates, making it more efficient for coating large substrates or producing thick films.
- The magnetic field enhances ionization efficiency, leading to faster sputtering and higher throughput.
-
Ion Beam Sputtering:
-
Applications:
-
Ion Beam Sputtering:
- IBS is commonly used in applications requiring high-precision coatings, such as optical coatings, semiconductor devices, and research-grade thin films.
- Its ability to deposit high-quality films with minimal defects makes it ideal for advanced materials research and high-performance coatings.
-
Magnetron Sputtering:
- Magnetron sputtering is widely used in industrial applications, including decorative coatings, hard coatings, and large-area coatings for architectural glass or solar panels.
- Its high deposition rates and scalability make it a preferred choice for mass production.
-
Ion Beam Sputtering:
-
Operational Complexity and Cost:
-
Ion Beam Sputtering:
- IBS systems are generally more complex and expensive due to the need for a separate ion source and precise beam control.
- The process requires careful optimization of ion energy and beam focus, which can increase operational complexity.
-
Magnetron Sputtering:
- Magnetron sputtering systems are relatively simpler and more cost-effective, especially for large-scale industrial applications.
- The use of magnetic fields and high-density plasma simplifies the process, but it may require additional cooling or shielding to manage substrate heating.
-
Ion Beam Sputtering:
In summary, ion beam sputtering and magnetron sputtering each have unique advantages and limitations. IBS excels in precision and versatility, making it suitable for high-quality, small-scale applications, while magnetron sputtering offers high deposition rates and scalability, ideal for industrial and large-area coatings. The choice between the two depends on the specific requirements of the application, such as film quality, substrate sensitivity, and production scale.
Summary Table:
Aspect | Ion Beam Sputtering (IBS) | Magnetron Sputtering |
---|---|---|
Mechanism | Uses a focused ion beam; no plasma between target and substrate. | Uses a magnetic field to confine plasma near the target. |
Target Compatibility | Works with conductive and non-conductive materials. | Requires conductive targets; reactive sputtering for non-conductive materials. |
Deposition Rate | Lower deposition rate but high film quality. | High deposition rates, ideal for large-area coatings. |
Applications | Precision coatings for optics, semiconductors, and research. | Industrial uses like decorative coatings, hard coatings, and solar panels. |
Operational Complexity | More complex and expensive due to precise ion beam control. | Simpler and cost-effective for large-scale applications. |
Need help choosing the right sputtering technique for your application? Contact our experts today!