LPCVD (Low-Pressure Chemical Vapor Deposition) and PECVD (Plasma-Enhanced Chemical Vapor Deposition) are both widely used in thin-film deposition processes, particularly in semiconductor manufacturing. While both techniques fall under the broader category of CVD, they differ significantly in their operating principles, temperature requirements, deposition rates, and applications. LPCVD operates at higher temperatures and does not require a plasma, making it suitable for high-purity, uniform films. In contrast, PECVD utilizes plasma to enhance the deposition process, enabling lower operating temperatures and faster deposition rates, which is advantageous for temperature-sensitive substrates. Understanding these differences is crucial for selecting the appropriate method based on the specific requirements of the application.
Key Points Explained:
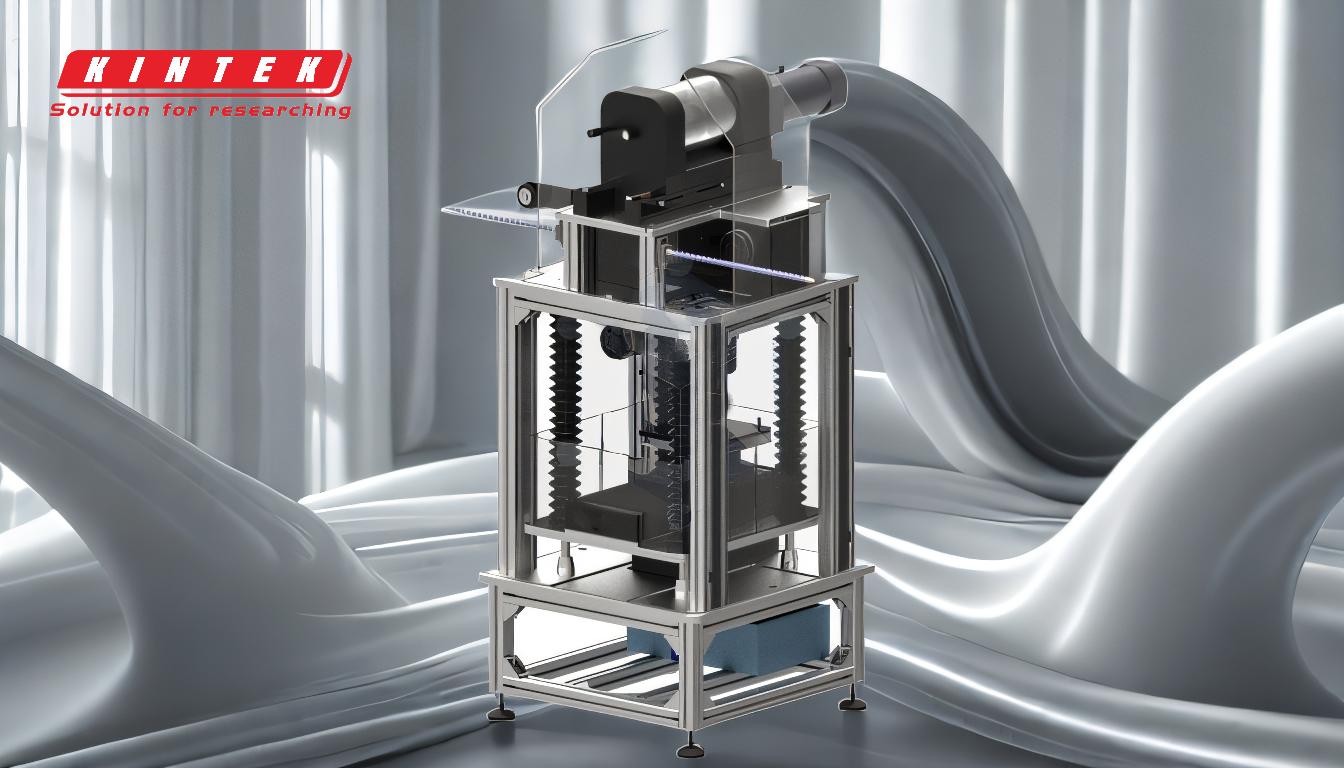
-
Operating Temperature:
- LPCVD: Operates at high temperatures, typically ranging from 450°C to 900°C. This high-temperature environment facilitates the chemical reactions necessary for film deposition without the need for plasma.
- PECVD: Operates at significantly lower temperatures, often between 200°C and 400°C. The use of plasma allows the chemical reactions to occur at these lower temperatures, making it suitable for substrates that cannot withstand high heat.
-
Deposition Rate:
- LPCVD: Generally has a slower deposition rate compared to PECVD. The high-temperature process is more controlled, resulting in high-quality, uniform films but at a slower pace.
- PECVD: Offers faster deposition rates due to the plasma-enhanced reactions. This makes PECVD more efficient for applications requiring rapid film growth.
-
Plasma Utilization:
- LPCVD: Does not use plasma. The deposition process relies solely on thermal energy to drive the chemical reactions.
- PECVD: Utilizes plasma to enhance the chemical reactions. The plasma provides additional energy, allowing the reactions to occur at lower temperatures and increasing the deposition rate.
-
Film Quality and Uniformity:
- LPCVD: Produces films with high purity and excellent uniformity. The absence of plasma reduces the risk of contamination, and the high temperatures ensure a well-controlled deposition process.
- PECVD: Also produces high-quality films, but the presence of plasma can sometimes introduce impurities. However, PECVD offers better edge coverage and more uniform films over complex geometries due to the plasma's ability to enhance surface reactions.
-
Substrate Compatibility:
- LPCVD: Does not require a silicon substrate and can deposit films on a variety of materials. However, the high temperatures limit its use with temperature-sensitive substrates.
- PECVD: Compatible with a wider range of substrates, including those that are temperature-sensitive, due to its lower operating temperatures. This makes PECVD more versatile for applications involving delicate materials.
-
Applications:
- LPCVD: Commonly used in applications requiring high-purity, uniform films, such as in the production of silicon nitride and polysilicon layers in semiconductor devices.
- PECVD: Preferred for applications where lower temperatures and faster deposition rates are necessary, such as in the fabrication of thin-film transistors, solar cells, and protective coatings on temperature-sensitive materials.
Understanding these key differences allows for the appropriate selection of either LPCVD or PECVD based on the specific requirements of the thin-film deposition process, ensuring optimal results for the intended application.
Summary Table:
Aspect | LPCVD | PECVD |
---|---|---|
Operating Temperature | 450°C to 900°C | 200°C to 400°C |
Deposition Rate | Slower, high-quality films | Faster, efficient for rapid film growth |
Plasma Utilization | No plasma, relies on thermal energy | Uses plasma for enhanced reactions |
Film Quality | High purity, uniform films | High quality with better edge coverage |
Substrate Compatibility | Limited for temperature-sensitive materials | Compatible with temperature-sensitive substrates |
Applications | Silicon nitride, polysilicon layers | Thin-film transistors, solar cells, protective coatings |
Need help choosing between LPCVD and PECVD for your application? Contact our experts today!