Magnetron sputtering and DC sputtering are both physical vapor deposition (PVD) techniques used to deposit thin films onto substrates. However, they differ significantly in their mechanisms, efficiency, and applications. Magnetron sputtering is an enhanced version of DC sputtering, incorporating a magnetic field to improve plasma confinement and deposition rates. This method is more efficient and versatile, allowing for the deposition of both conductive and non-conductive materials, depending on whether DC or RF (radio frequency) power is used. DC sputtering, on the other hand, is simpler but limited to conductive materials and generally operates at higher pressures. Below, we explore the key differences between these two techniques in detail.
Key Points Explained:
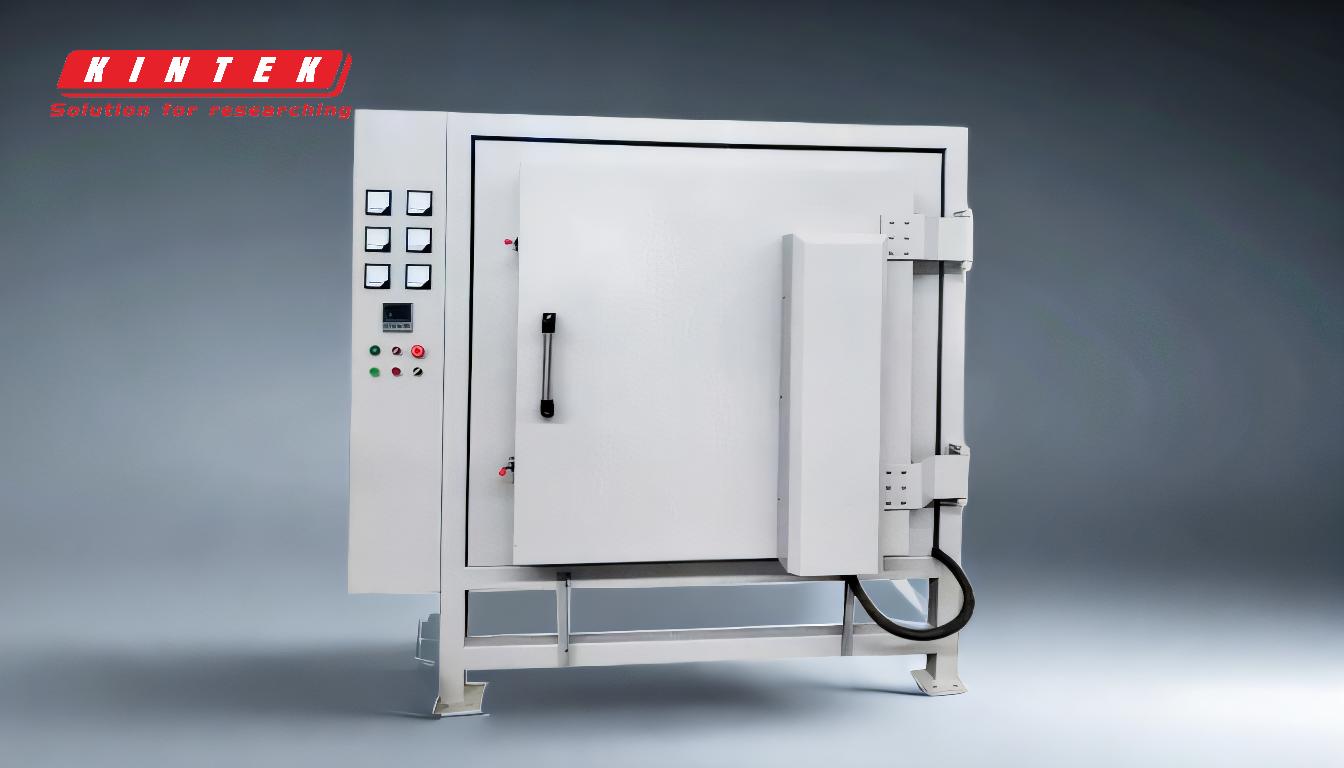
-
Mechanism of Plasma Confinement:
- Magnetron Sputtering: Utilizes a magnetic field near the target area to trap electrons, increasing their path length and the likelihood of ionizing gas atoms. This confinement enhances plasma density and deposition rates.
- DC Sputtering: Relies solely on an electric field to accelerate ions toward the target. Without magnetic confinement, the plasma is less dense, resulting in lower deposition rates.
-
Power Source and Material Compatibility:
-
Magnetron Sputtering:
- DC Magnetron Sputtering: Uses direct current and is suitable only for conductive materials.
- RF Magnetron Sputtering: Alternates the charge, preventing charge buildup on the target, and can be used with both conductive and non-conductive materials.
- DC Sputtering: Limited to direct current and conductive materials, as non-conductive targets would accumulate charge and disrupt the process.
-
Magnetron Sputtering:
-
Operating Pressure:
- Magnetron Sputtering: Operates efficiently at lower pressures due to the high ionization efficiency of the confined plasma.
- DC Sputtering: Typically requires higher pressures to sustain the plasma, which can be more challenging to maintain and may lead to less efficient deposition.
-
Deposition Rate and Efficiency:
- Magnetron Sputtering: The magnetic field increases the ionization of sputtering gas, leading to higher deposition rates and better energy efficiency.
- DC Sputtering: Lower plasma density results in slower deposition rates and less efficient use of energy.
-
Applications and Versatility:
- Magnetron Sputtering: Versatile and widely used in industries requiring high-quality thin films, such as semiconductors, optics, and decorative coatings. RF magnetron sputtering is particularly useful for depositing insulating materials.
- DC Sputtering: Primarily used for depositing conductive materials in applications where simplicity and cost-effectiveness are prioritized over deposition speed and material versatility.
-
Complexity and Cost:
- Magnetron Sputtering: More complex due to the addition of magnetic fields and the need for precise control of plasma confinement. This complexity can lead to higher equipment and operational costs.
- DC Sputtering: Simpler and less expensive, making it a practical choice for basic applications.
In summary, magnetron sputtering offers significant advantages over DC sputtering, including higher deposition rates, greater material compatibility, and better efficiency. However, these benefits come with increased complexity and cost. The choice between the two methods depends on the specific requirements of the application, such as the type of material to be deposited, the desired deposition rate, and budget constraints.
Summary Table:
Aspect | Magnetron Sputtering | DC Sputtering |
---|---|---|
Mechanism | Uses magnetic fields to trap electrons, enhancing plasma density and deposition rates. | Relies on electric fields, resulting in lower plasma density and slower rates. |
Material Compatibility | Compatible with conductive and non-conductive materials (RF magnetron sputtering). | Limited to conductive materials only. |
Operating Pressure | Operates efficiently at lower pressures. | Requires higher pressures to sustain plasma. |
Deposition Rate | Higher deposition rates due to increased ionization efficiency. | Slower deposition rates due to lower plasma density. |
Applications | Widely used in semiconductors, optics, and decorative coatings. | Primarily used for conductive materials in simpler applications. |
Complexity and Cost | More complex and costly due to magnetic field integration. | Simpler and more cost-effective for basic applications. |
Need help choosing the right sputtering technique for your application? Contact our experts today!