Sintering and melting are two distinct processes used to bind or combine materials, particularly metals, but they differ significantly in terms of temperature, energy requirements, and the physical state of the material. Melting involves heating a material to its melting point, causing it to transition from a solid to a liquid state, which requires high energy and can lead to imperfections. Sintering, on the other hand, uses a combination of heat and pressure to bond particles together without liquefying the material, making it more energy-efficient and suitable for materials with high melting points. Sintering occurs at temperatures below the material's melting point and can be performed at lower temperatures with sufficient pressure, offering greater control and consistency in the final product.
Key Points Explained:
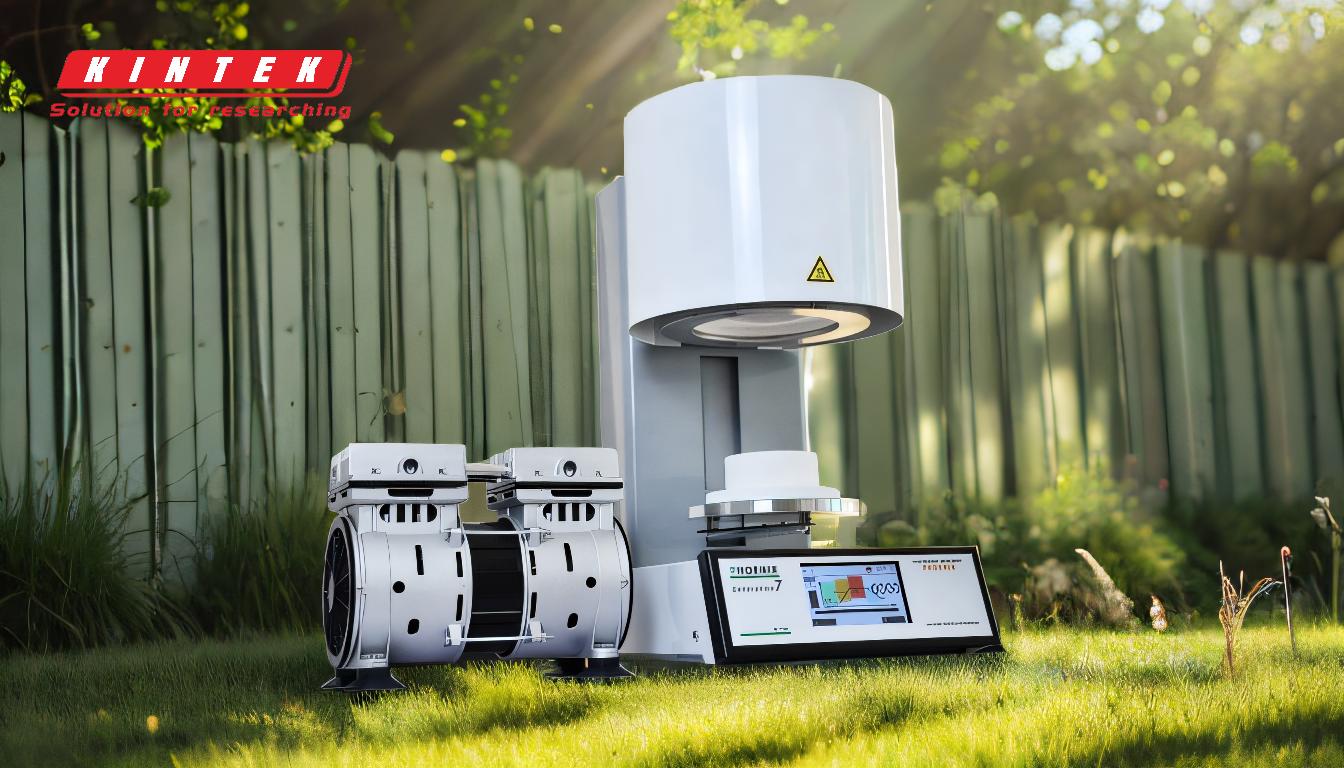
-
Temperature Requirements:
- Melting: Requires the material to reach its melting point, where it transitions from a solid to a liquid state. This process demands high temperatures and significant energy input.
- Sintering: Occurs at temperatures below the material's melting point. It uses a combination of heat and pressure to bond particles together without causing liquefaction, making it more energy-efficient.
-
Physical State of Material:
- Melting: Involves a complete phase change from solid to liquid. The material becomes fully molten, which can lead to imperfections such as porosity or uneven cooling.
- Sintering: The material remains in a solid state throughout the process. Particles are fused together through diffusion and pressure, resulting in a solid but porous structure.
-
Energy Efficiency:
- Melting: High energy consumption due to the need to reach and maintain the material's melting point.
- Sintering: More energy-efficient as it operates at lower temperatures and does not require the material to reach its melting point.
-
Control and Consistency:
- Melting: Less control over the process due to the material's liquid state, which can lead to inconsistencies and defects in the final product.
- Sintering: Offers greater control and consistency, as the material remains solid and the process can be finely tuned with pressure and temperature adjustments.
-
Suitability for High Melting Point Materials:
- Melting: Challenging for materials with very high melting points, as it requires extreme temperatures and energy.
- Sintering: Ideal for materials with high melting points, as it does not require the material to reach its melting temperature.
-
Application Examples:
- Melting: Commonly used in casting processes where the material needs to be poured into molds.
- Sintering: Used in powder metallurgy to create complex shapes and components, often enhancing properties like strength and hardness.
-
Pressure Role:
- Melting: Primarily driven by temperature, with pressure playing a minimal role.
- Sintering: Can be driven by both temperature and pressure. In some cases, sufficient pressure alone can induce sintering at low temperatures.
-
Final Product Characteristics:
- Melting: Results in a fully dense material, but with potential for defects like porosity or inclusions.
- Sintering: Produces a porous material, which can be advantageous for certain applications like filters or self-lubricating bearings.
By understanding these key differences, one can choose the appropriate method based on the material properties and the desired outcome of the process. Sintering is often preferred for its energy efficiency and ability to handle high melting point materials, while melting is suitable for applications requiring a fully dense and homogeneous material.
Summary Table:
Aspect | Melting | Sintering |
---|---|---|
Temperature | Reaches melting point (high energy) | Below melting point (energy-efficient) |
Material State | Solid to liquid transition | Remains solid; particles bond without liquefaction |
Energy Efficiency | High energy consumption | More energy-efficient |
Control & Consistency | Less control; potential for defects | Greater control; consistent results |
High Melting Materials | Challenging due to extreme temperatures | Ideal; does not require melting |
Applications | Casting processes | Powder metallurgy, complex shapes, enhanced properties |
Pressure Role | Minimal role | Can drive sintering with pressure |
Final Product | Fully dense but may have defects | Porous structure; useful for filters, bearings |
Need help choosing the right process for your material? Contact our experts today!