Physical Vapor Deposition (PVD) and Chemical Vapor Deposition (CVD) are two prominent techniques used to deposit thin films onto substrates, but they differ significantly in their processes, materials, and applications. PVD relies on physical means, such as vaporizing a solid material and condensing it onto a substrate, resulting in durable, high-temperature-resistant coatings. CVD, on the other hand, involves chemical reactions between gaseous precursors and the substrate, enabling the deposition of thicker, rougher layers on a broader range of materials. The choice between PVD and CVD depends on factors like desired coating properties, substrate compatibility, and application requirements.
Key Points Explained:
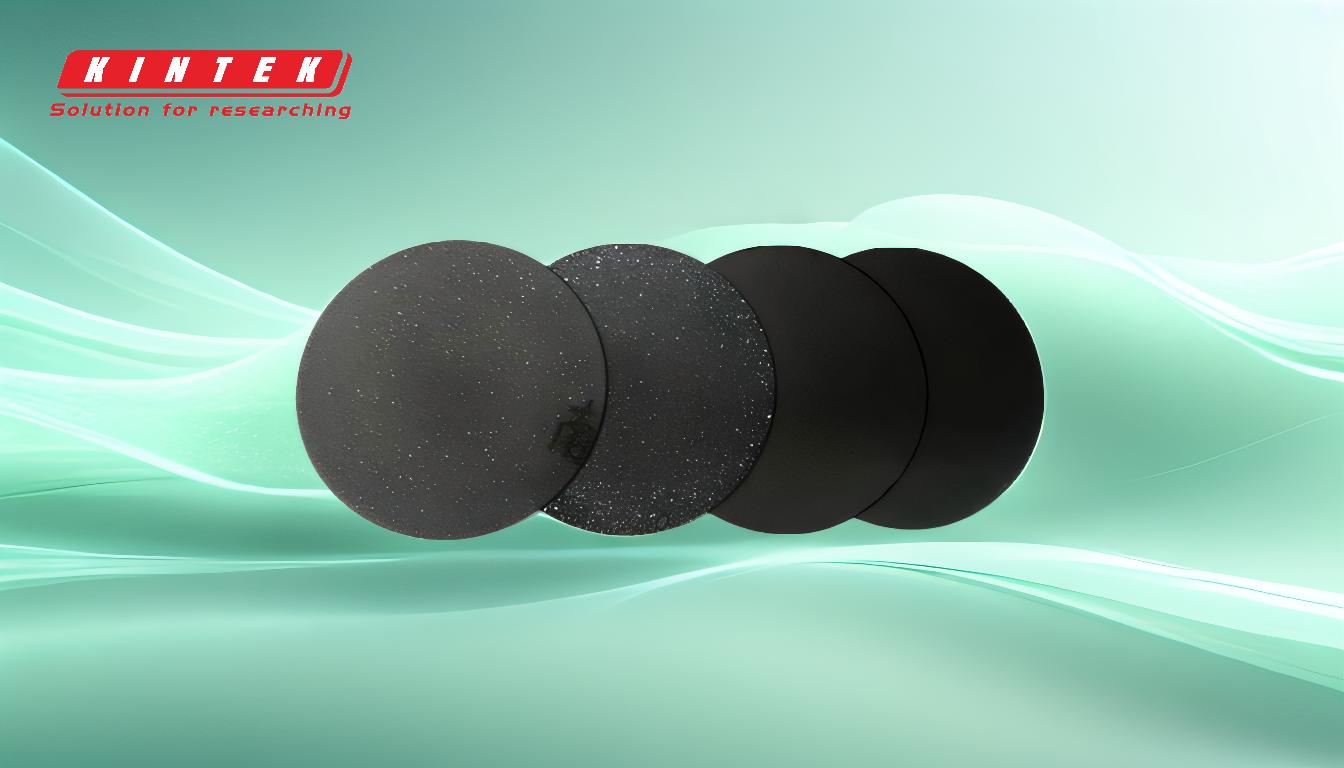
-
Process Mechanism:
- PVD: Utilizes physical reactions to convert a solid material into vapor, which then condenses onto the substrate to form a thin film. This process involves no chemical changes in the material.
- CVD: Relies on chemical reactions between gaseous precursors and the substrate surface. The reaction produces a solid film, often accompanied by byproducts like gases or liquids.
-
Material State:
- PVD: Uses solid coating materials that are vaporized and deposited onto the substrate.
- CVD: Employs gaseous coating materials that chemically react with the substrate to form the desired layer.
-
Temperature Requirements:
- PVD: Operates at relatively lower temperatures, typically between 250°C and 450°C, making it suitable for temperature-sensitive substrates.
- CVD: Requires higher temperatures, ranging from 450°C to 1050°C, which can limit its use with certain materials but enables the deposition of thicker and more robust coatings.
-
Coating Characteristics:
- PVD: Produces thin, smooth, and highly durable coatings with excellent adhesion and resistance to high temperatures and wear.
- CVD: Results in thicker, rougher coatings that can be applied to a wider variety of materials, including complex shapes and internal surfaces.
-
Application Suitability:
- PVD: Ideal for applications requiring high precision, durability, and resistance to extreme conditions, such as cutting tools, medical devices, and aerospace components.
- CVD: Suitable for applications needing uniform coatings on complex geometries, such as semiconductor devices, optical components, and protective coatings for industrial tools.
-
Advantages and Limitations:
-
PVD Advantages:
- High durability and wear resistance.
- Excellent adhesion and smooth surface finish.
- Lower temperature processing reduces substrate damage.
-
PVD Limitations:
- Limited to line-of-sight deposition, making it challenging to coat complex geometries.
- Typically produces thinner coatings compared to CVD.
-
CVD Advantages:
- Can coat complex shapes and internal surfaces uniformly.
- Produces thicker coatings with better conformality.
- Compatible with a broader range of materials.
-
CVD Limitations:
- Higher temperatures may damage temperature-sensitive substrates.
- Chemical byproducts may require additional handling and disposal.
-
PVD Advantages:
-
Industrial Applications:
- PVD: Commonly used in industries requiring high-performance coatings, such as automotive (engine components), aerospace (turbine blades), and medical (surgical instruments).
- CVD: Widely applied in semiconductor manufacturing (integrated circuits), optics (anti-reflective coatings), and wear-resistant coatings for industrial tools.
By understanding these key differences, equipment and consumable purchasers can make informed decisions based on the specific requirements of their applications, such as coating thickness, substrate compatibility, and environmental conditions.
Summary Table:
Aspect | PVD | CVD |
---|---|---|
Process Mechanism | Physical vaporization and condensation of solid materials. | Chemical reactions between gaseous precursors and the substrate. |
Material State | Solid materials vaporized and deposited. | Gaseous materials chemically react to form solid films. |
Temperature Range | 250°C to 450°C (lower, suitable for sensitive substrates). | 450°C to 1050°C (higher, enables thicker coatings). |
Coating Characteristics | Thin, smooth, durable, and wear-resistant. | Thicker, rougher, and applicable to complex geometries. |
Applications | Cutting tools, medical devices, aerospace components. | Semiconductor devices, optical components, industrial tools. |
Advantages | High durability, smooth finish, lower temperature processing. | Uniform coatings on complex shapes, thicker films, broader material compatibility. |
Limitations | Line-of-sight deposition, thinner coatings. | High temperatures, chemical byproducts. |
Need help choosing between PVD and CVD for your application? Contact our experts today for personalized guidance!