Plasma CVD (Chemical Vapor Deposition) and thermal CVD are both techniques used to deposit thin films onto substrates, but they differ significantly in their mechanisms, operating conditions, and applications. Plasma CVD utilizes plasma to activate chemical reactions at lower temperatures, making it suitable for temperature-sensitive substrates. Thermal CVD, on the other hand, relies on high temperatures to drive chemical reactions, which can limit its use with certain materials. Both methods have unique advantages and limitations, and the choice between them depends on factors like substrate compatibility, desired film properties, and operational constraints.
Key Points Explained:
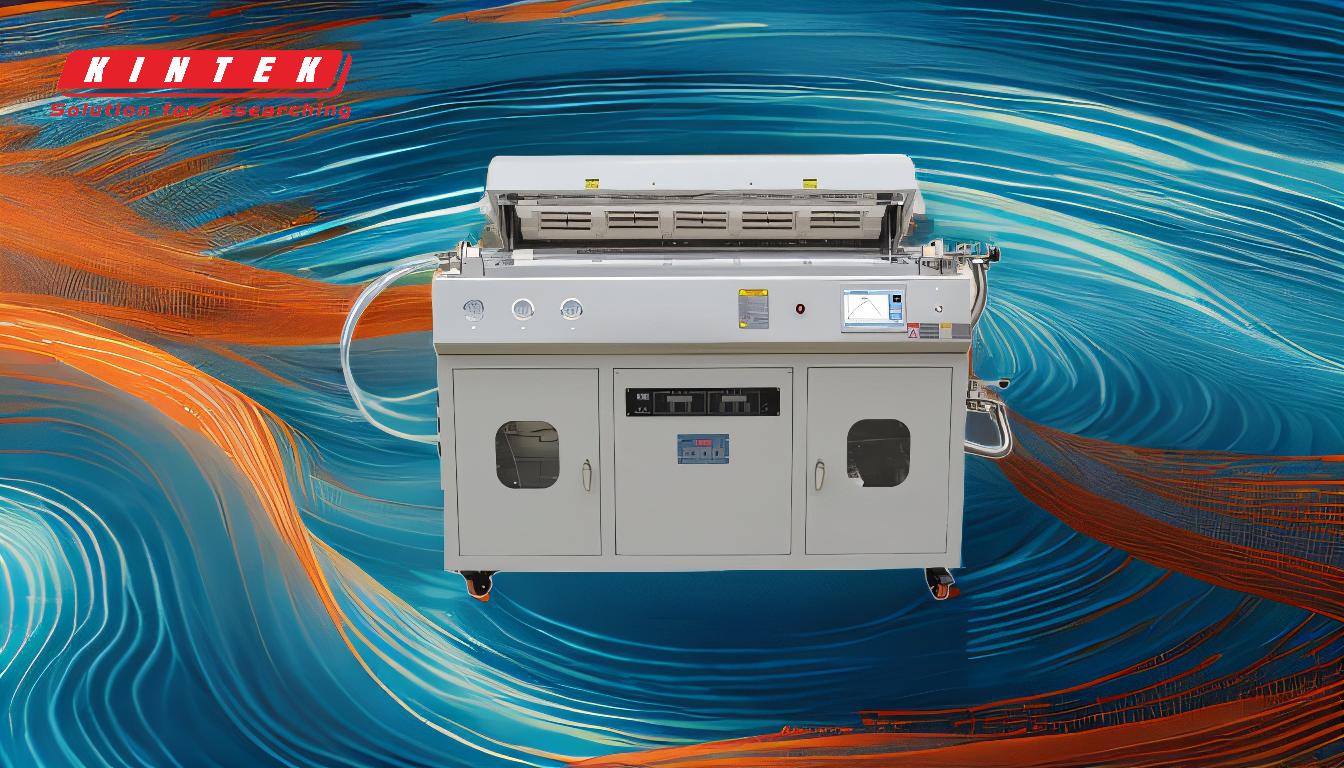
-
Mechanism of Deposition:
- Plasma CVD: This method uses plasma (an ionized gas) to activate chemical reactions at lower temperatures. The plasma provides the energy needed to break down gaseous precursors into reactive species, which then deposit onto the substrate. This process is highly controllable and can be used for a wide range of materials.
- Thermal CVD: In thermal CVD, high temperatures are used to thermally decompose gaseous precursors, leading to the formation of a solid film on the substrate. This method is effective for high-quality, dense coatings but requires substrates that can withstand high temperatures.
-
Temperature Requirements:
- Plasma CVD: Operates at relatively lower temperatures (typically below 500°C), making it suitable for temperature-sensitive substrates such as polymers or certain metals.
- Thermal CVD: Requires high temperatures (450°C to 1050°C), which can limit its use with substrates that cannot tolerate such heat. This method is often used for high-temperature-resistant materials like ceramics.
-
Deposition Rate and Uniformity:
- Plasma CVD: Offers faster deposition rates and better uniformity due to the controlled activation of reactive species by the plasma. This makes it ideal for applications requiring precise film properties.
- Thermal CVD: Generally provides denser and more uniform coatings but at a slower deposition rate. The high temperatures ensure strong adhesion and high-quality films.
-
Material Compatibility:
- Plasma CVD: Can deposit a broader range of materials, including metals, alloys, and ceramics, due to its lower temperature operation and plasma activation.
- Thermal CVD: Typically limited to ceramics and polymers, as the high temperatures can degrade or react with other materials.
-
Applications:
- Plasma CVD: Widely used in semiconductor manufacturing, optical coatings, and protective coatings for temperature-sensitive materials.
- Thermal CVD: Commonly used in the production of high-performance ceramics, coatings for cutting tools, and other applications requiring high-temperature resistance.
-
Advantages and Limitations:
-
Plasma CVD:
- Advantages: Lower temperature operation, faster deposition rates, and better control over film properties.
- Limitations: Requires complex equipment and careful handling of plasma, which can introduce impurities if not properly managed.
-
Thermal CVD:
- Advantages: Produces dense, high-quality films with excellent adhesion and uniformity.
- Limitations: High temperatures can limit substrate compatibility and increase operational costs.
-
Plasma CVD:
-
Comparison with Other Techniques:
- Both plasma CVD and thermal CVD differ from PVD (Physical Vapor Deposition), which involves the physical vaporization of materials without chemical reactions. PVD is typically used for metals and alloys and operates at lower temperatures compared to thermal CVD. For more information on related techniques, you can explore short path vacuum distillation.
In summary, the choice between plasma CVD and thermal CVD depends on the specific requirements of the application, including substrate compatibility, desired film properties, and operational constraints. Plasma CVD offers advantages in terms of lower temperature operation and faster deposition rates, while thermal CVD excels in producing high-quality, dense coatings at higher temperatures.
Summary Table:
Aspect | Plasma CVD | Thermal CVD |
---|---|---|
Mechanism | Uses plasma to activate reactions at lower temperatures | Relies on high temperatures to thermally decompose precursors |
Temperature | Operates below 500°C, suitable for temperature-sensitive substrates | Requires 450°C to 1050°C, limited to high-temperature-resistant materials |
Deposition Rate | Faster deposition rates with better uniformity | Slower deposition rates but denser, more uniform coatings |
Material Compatibility | Deposits a wide range of materials (metals, alloys, ceramics) | Limited to ceramics and polymers due to high temperatures |
Applications | Semiconductor manufacturing, optical coatings, protective coatings | High-performance ceramics, cutting tool coatings, high-temperature resistance |
Advantages | Lower temperature operation, faster deposition, better control over film properties | Produces dense, high-quality films with excellent adhesion and uniformity |
Limitations | Complex equipment, potential for impurities | High temperatures limit substrate compatibility, higher operational costs |
Need help choosing between plasma CVD and thermal CVD? Contact our experts today for tailored advice!