Physical Vapor Deposition (PVD) and Atomic Layer Deposition (ALD) are two distinct thin-film deposition techniques used in various industries, each with unique processes, advantages, and applications. PVD relies on physical processes like evaporation or sputtering to deposit materials, often at lower temperatures and with high deposition rates, making it suitable for simpler geometries and alloy depositions. In contrast, ALD is a chemical process that uses sequential, self-limiting reactions to deposit ultra-thin, conformal films with precise thickness control, ideal for complex geometries and high-precision applications. While PVD is a "line-of-sight" process, ALD provides isotropic coating, ensuring uniform coverage on all surfaces.
Key Points Explained:
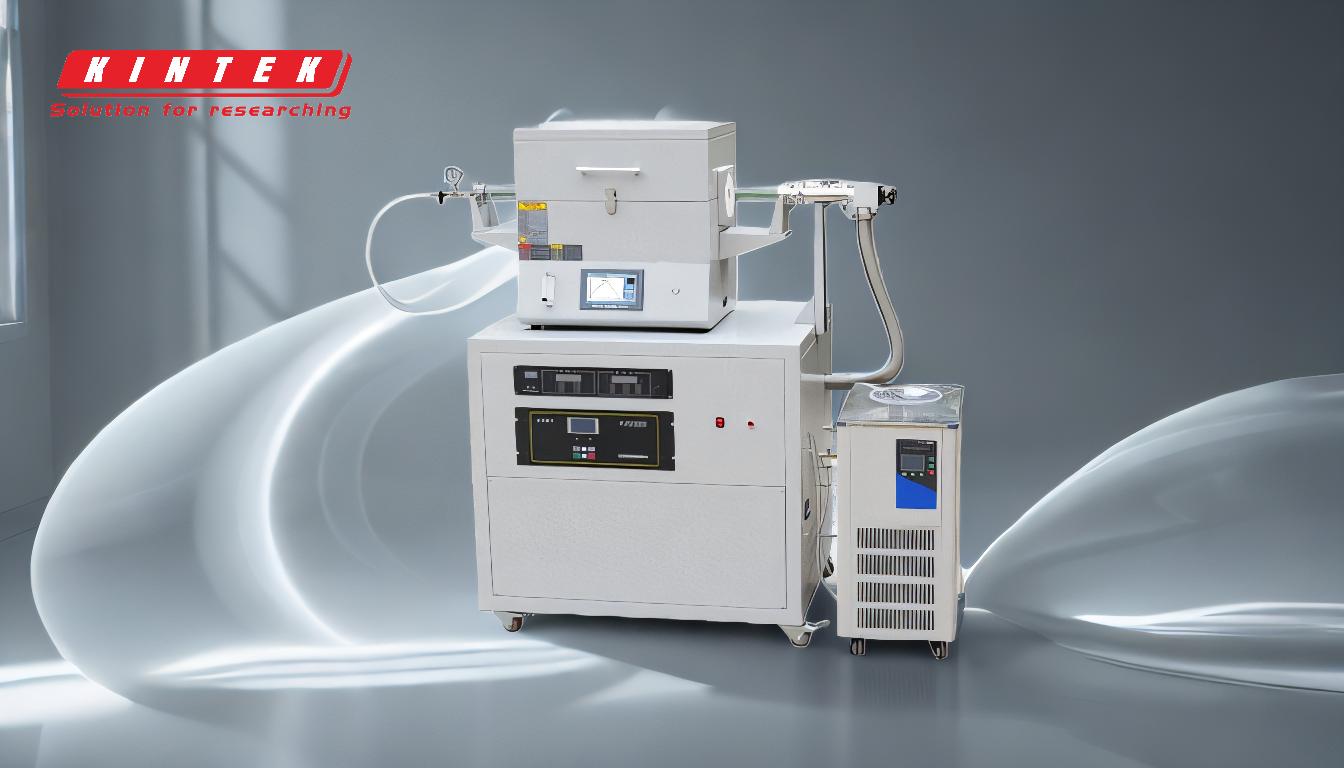
-
Process Mechanism:
- PVD: Involves physical processes such as evaporation or sputtering, where solid materials are vaporized and then condensed onto a substrate. This process does not rely on chemical reactions and is carried out under vacuum conditions.
- ALD: A chemical process that uses sequential pulses of precursors and reactants to form a chemically-bound monolayer on the substrate. Each step is self-limiting, ensuring precise control over film thickness.
-
Temperature Requirements:
- PVD: Can be performed at relatively low temperatures, making it suitable for temperature-sensitive substrates. This is particularly advantageous for applications requiring low thermal stress.
- ALD: Typically requires higher temperatures to facilitate the chemical reactions necessary for film growth. However, ALD can also be adapted for low-temperature processes in some cases.
-
Deposition Rates:
- PVD: Offers high deposition rates, ranging from 0.1 to 100 μm/min, depending on the method (e.g., EBPVD). This makes it suitable for applications where rapid coating is needed.
- ALD: Has much lower deposition rates due to its layer-by-layer growth mechanism. Each cycle deposits only a single atomic layer, resulting in slower overall deposition but exceptional precision.
-
Coating Uniformity and Conformality:
- PVD: A "line-of-sight" process, meaning only surfaces directly exposed to the source are coated. This limits its effectiveness for complex geometries or substrates with intricate features.
- ALD: Provides isotropic coating, ensuring uniform coverage on all surfaces, including those with complex geometries. This makes ALD ideal for applications requiring high conformality.
-
Material Utilization and Efficiency:
- PVD: High material utilization efficiency, especially in methods like EBPVD. The process is efficient in terms of raw material usage and can be cost-effective for large-scale production.
- ALD: While highly precise, ALD can be less efficient in terms of material usage due to the sequential nature of the process and the need for precise precursor delivery.
-
Applications:
- PVD: Commonly used for applications requiring high deposition rates, such as decorative coatings, hard coatings for tools, and alloy depositions. It is also suitable for simpler substrate geometries.
- ALD: Ideal for applications requiring ultra-thin, conformal films with precise thickness control, such as semiconductor manufacturing, MEMS devices, and advanced optics.
-
Safety and Handling:
- PVD: Generally safer and easier to handle as it does not rely on toxic chemicals or require high substrate temperatures. The process is less likely to produce corrosive by-products.
- ALD: While ALD is also safe, it involves handling reactive precursors and may require more stringent safety protocols to manage chemical reactions and by-products.
-
Cost and Scalability:
- PVD: Often more cost-effective for large-scale production due to higher deposition rates and simpler process requirements. It is scalable for industrial applications.
- ALD: More expensive and slower, making it less suitable for high-volume production. However, its precision and conformality justify its use in high-value, specialized applications.
By understanding these key differences, equipment and consumable purchasers can make informed decisions about which deposition technique best suits their specific needs, whether prioritizing speed, precision, or cost-effectiveness.
Summary Table:
Aspect | PVD | ALD |
---|---|---|
Process Mechanism | Physical processes like evaporation or sputtering | Chemical process with sequential, self-limiting reactions |
Temperature | Lower temperatures, suitable for sensitive substrates | Higher temperatures, but adaptable for low-temperature processes |
Deposition Rate | High (0.1 to 100 μm/min) | Low (layer-by-layer growth) |
Coating Uniformity | Line-of-sight, limited for complex geometries | Isotropic, uniform coverage on all surfaces |
Material Efficiency | High material utilization | Less efficient due to sequential process |
Applications | Decorative coatings, hard coatings, alloy depositions | Semiconductor manufacturing, MEMS devices, advanced optics |
Safety | Safer, fewer toxic chemicals | Requires handling reactive precursors |
Cost & Scalability | Cost-effective for large-scale production | Expensive, suitable for high-value, specialized applications |
Need help selecting the right thin-film deposition technique? Contact our experts today for personalized guidance!