PVD (Physical Vapor Deposition) coating is a specific type of coating process that differs from traditional coating methods in several key ways. PVD is a thin-film deposition technique that uses physical processes, such as sputtering or evaporation, to deposit materials onto a substrate in a vacuum environment. This results in a thin, durable, and high-quality coating that offers superior hardness, resistance to wear, and aesthetic flexibility. Unlike traditional coating methods, which often involve chemical reactions and thicker layers, PVD is more environmentally friendly, as it avoids the use of hazardous substances and produces recyclable components. PVD is particularly valued for its ability to apply a wide range of materials, including metals, alloys, and ceramics, making it suitable for applications requiring high performance and durability.
Key Points Explained:
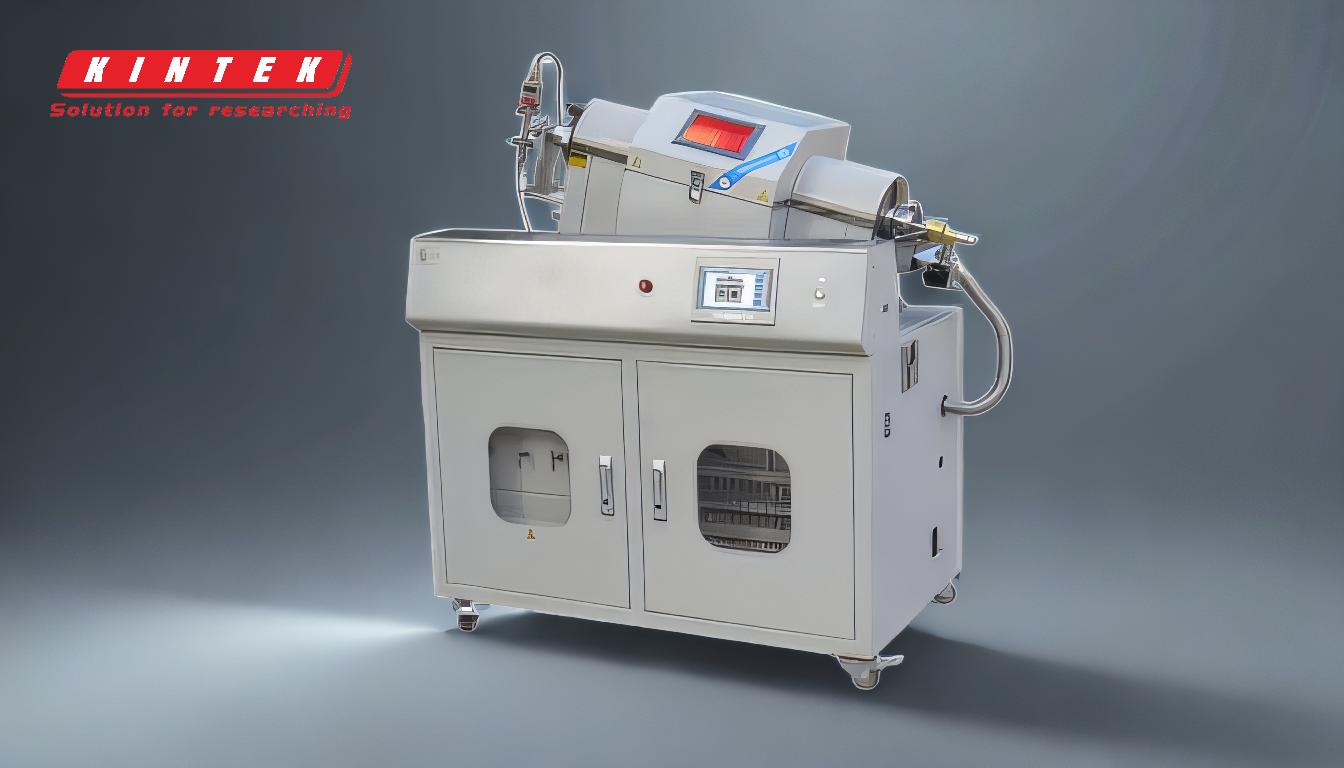
-
Thin Film Deposition:
- PVD coating is known for producing a thin film on the workpiece, typically in the range of nanometers to micrometers. This is in contrast to traditional coating methods, which often result in thicker layers.
- The thin-film nature of PVD allows for precise control over the coating's thickness and properties, making it ideal for applications requiring high precision and performance.
-
Environmental Friendliness:
- PVD is considered a more environmentally friendly alternative to traditional coating processes like chrome plating. It does not involve the use of hazardous chemicals or generate toxic by-products.
- The coated components are 100% recyclable, contributing to sustainability and reducing environmental impact.
-
Durability and Performance:
- PVD coatings are highly durable and resistant to wear, friction, and heat. This makes them suitable for applications that demand high performance, such as automotive parts, cutting tools, and medical devices.
- The coatings also offer increased hardness and scratch resistance, extending the lifespan of the coated components.
-
Aesthetic Flexibility:
- PVD allows for a wide range of colors and finishes, providing greater design freedom. The texture of the underlying metal can remain visible, enhancing the aesthetic appeal of the coated product.
- This makes PVD a popular choice for decorative applications, such as jewelry, watches, and architectural elements.
-
Material Versatility:
- PVD can deposit a broader range of materials, including metals, alloys, and ceramics, compared to other coating methods like CVD (Chemical Vapor Deposition), which is typically limited to ceramics and polymers.
- This versatility allows PVD to be used in a wide variety of industries and applications.
-
Process Differences:
- PVD occurs in a vacuum at high temperatures using physical processes, such as sputtering or evaporation. This contrasts with CVD, which relies on chemical reactions at lower temperatures.
- PVD coatings are less dense and less uniform than CVD coatings but are faster to apply, making them more efficient for certain applications.
-
Superior Finish:
- PVD provides a superior finish due to its molecular-scale application. This results in a high-quality, uniform coating that enhances both the functional and aesthetic properties of the substrate.
- The process also reduces the need for post-coating treatments, saving time and resources.
In summary, PVD coating stands out from traditional coating methods due to its thin-film deposition, environmental friendliness, durability, aesthetic flexibility, material versatility, and superior finish. These characteristics make PVD an ideal choice for a wide range of high-performance and decorative applications.
Summary Table:
Feature | PVD Coating | Traditional Coating |
---|---|---|
Thickness | Thin film (nanometers to micrometers) | Thicker layers |
Environmental Impact | Eco-friendly, no hazardous chemicals, recyclable components | Often involves toxic chemicals and by-products |
Durability | High resistance to wear, friction, and heat | Less durable, prone to wear and tear |
Aesthetic Flexibility | Wide range of colors and finishes, preserves metal texture | Limited design options |
Material Versatility | Can deposit metals, alloys, and ceramics | Limited to specific materials (e.g., ceramics, polymers) |
Process | Physical processes (sputtering/evaporation) in a vacuum | Chemical reactions at lower temperatures |
Finish Quality | Superior, uniform, and molecular-scale application | Less uniform, may require post-coating treatments |
Ready to explore the benefits of PVD coating for your applications? Contact us today to learn more!