Pyrolysis and incineration are both thermal processes used to treat waste materials, but they differ significantly in terms of temperature, duration, environmental impact, and end products. Pyrolysis involves the thermal decomposition of carbonaceous materials in an oxygen-free environment at lower temperatures (350-550°C) over several hours, producing renewable products like bio-oil, syngas, and char. In contrast, incineration occurs at much higher temperatures (800-1000°C) over a few minutes in the presence of oxygen, resulting in the complete combustion of waste into ash, flue gas, and heat. Pyrolysis is considered more environmentally friendly due to its lower emissions and potential for resource recovery, while incineration is often used for waste volume reduction and energy generation.
Key Points Explained:
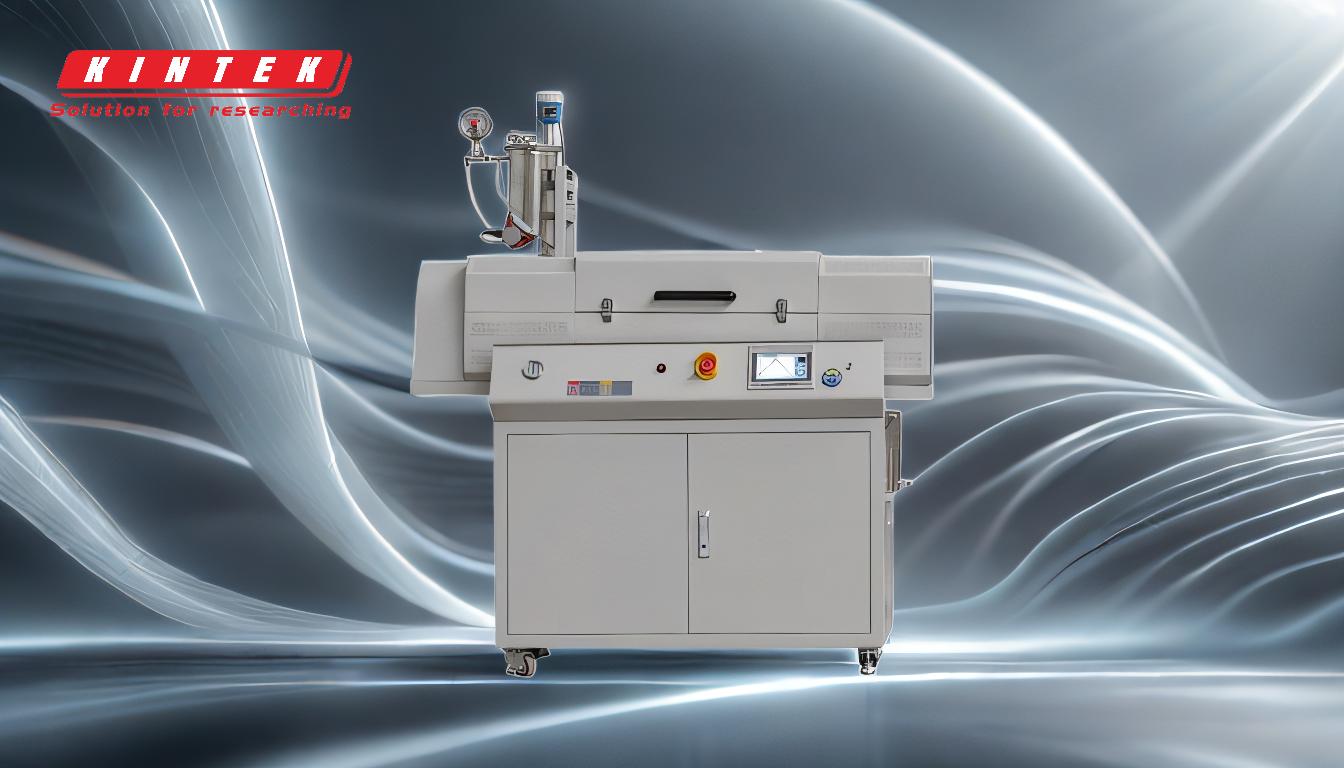
-
Temperature and Duration:
- Pyrolysis: Operates at lower temperatures (350-550°C) and takes several hours to complete. This slower process allows for the controlled breakdown of materials without combustion.
- Incineration: Operates at higher temperatures (800-1000°C) and is completed in a few minutes. The rapid, high-temperature process ensures complete combustion of waste materials.
-
Oxygen Environment:
- Pyrolysis: Conducted in an oxygen-free or low-oxygen environment, preventing combustion and allowing for the thermal decomposition of materials into useful byproducts.
- Incineration: Requires the presence of oxygen to facilitate the complete combustion of waste, resulting in the oxidation of materials.
-
End Products:
- Pyrolysis: Produces renewable products such as bio-oil, syngas, and char. These byproducts can be further processed or used as fuel, making pyrolysis a resource recovery process.
- Incineration: Produces ash, flue gas, and heat. The ash is typically landfilled, while the heat can be used for energy generation. However, the process does not recover resources in the same way as pyrolysis.
-
Environmental Impact:
- Pyrolysis: Generally considered more environmentally friendly due to lower emissions of pollutants and the potential for resource recovery. The process generates fewer harmful byproducts compared to incineration.
- Incineration: Can produce higher levels of pollutants, including dioxins and heavy metals, depending on the waste composition and the efficiency of the flue gas treatment system. However, modern incinerators are equipped with advanced emission control technologies to mitigate environmental impact.
-
Applications:
- Pyrolysis: Suitable for processing a wide range of materials, including biomass, tires, and plastics. It is often used in waste-to-energy and resource recovery applications.
- Incineration: Primarily used for municipal solid waste (MSW) treatment and hazardous waste disposal. It is effective for reducing waste volume and generating energy but is less focused on resource recovery.
-
Technological Variability:
- Pyrolysis: Technologies vary widely in terms of input materials, size, and the specific products generated. This variability allows for customization based on the desired output and feedstock.
- Incineration: Technologies are more standardized, focusing on efficient combustion and energy recovery. The process is less flexible in terms of the types of waste it can handle compared to pyrolysis.
In summary, while both pyrolysis and incineration are thermal waste treatment methods, they differ fundamentally in their operational conditions, environmental impact, and end products. Pyrolysis offers a more sustainable approach with potential for resource recovery, whereas incineration is effective for waste reduction and energy generation but with higher environmental concerns.
Summary Table:
Aspect | Pyrolysis | Incineration |
---|---|---|
Temperature | 350-550°C (lower) | 800-1000°C (higher) |
Duration | Several hours | A few minutes |
Oxygen Environment | Oxygen-free or low-oxygen | Requires oxygen |
End Products | Bio-oil, syngas, char | Ash, flue gas, heat |
Environmental Impact | Lower emissions, resource recovery | Higher emissions, waste volume reduction |
Applications | Biomass, tires, plastics (resource recovery) | Municipal solid waste, hazardous waste (energy generation) |
Technological Variability | Highly customizable based on input and output needs | Standardized, less flexible |
Discover the best waste treatment solution for your needs—contact our experts today!