Resistance brazing and induction brazing are two distinct methods of joining metals using a filler material, but they differ significantly in their heating mechanisms, applications, and operational characteristics. Resistance brazing relies on electrical resistance to generate heat directly at the joint, making it suitable for localized heating and precise control. Induction brazing, on the other hand, uses electromagnetic induction to heat the workpiece, offering faster heating rates and better suitability for complex geometries or high-volume production. Both methods have unique advantages and limitations, making them suitable for different industrial applications.
Key Points Explained:
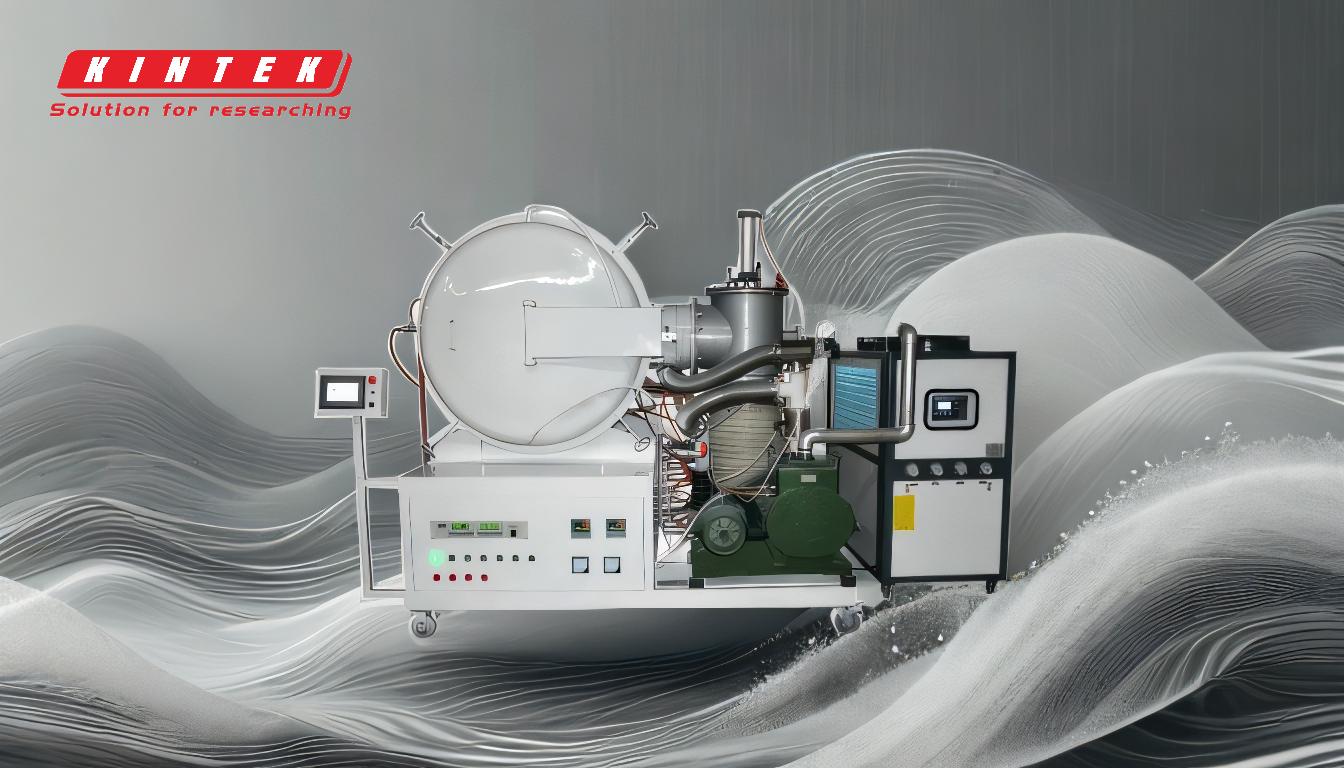
-
Heating Mechanism:
-
Resistance Brazing:
- Heat is generated by passing an electric current through the joint, which creates resistance and produces localized heating.
- The heat is concentrated at the joint, minimizing heat-affected zones in surrounding areas.
-
Induction Brazing:
- Heat is generated by inducing eddy currents in the workpiece using an alternating magnetic field.
- The heating is more uniform and can penetrate deeper into the material, making it suitable for larger or more complex parts.
-
Resistance Brazing:
-
Energy Efficiency:
-
Resistance Brazing:
- Highly energy-efficient for small, localized joints due to direct heat generation at the joint.
- Requires precise control of current and pressure to avoid overheating or insufficient heating.
-
Induction Brazing:
- More energy-efficient for larger parts or high-volume production because it heats the workpiece directly without significant energy loss.
- Faster heating rates reduce overall energy consumption for repetitive tasks.
-
Resistance Brazing:
-
Control and Precision:
-
Resistance Brazing:
- Offers excellent control over the heating process, making it ideal for delicate or precision work.
- Requires careful alignment of electrodes and consistent pressure to ensure proper joint formation.
-
Induction Brazing:
- Provides rapid and consistent heating, but control is more dependent on the design of the induction coil and frequency settings.
- Suitable for automated or high-speed production lines.
-
Resistance Brazing:
-
Applications:
-
Resistance Brazing:
- Commonly used for small components, such as electrical contacts, jewelry, or medical devices.
- Ideal for applications requiring localized heating and minimal thermal distortion.
-
Induction Brazing:
- Widely used in automotive, aerospace, and industrial manufacturing for larger or more complex assemblies.
- Suitable for high-volume production and parts with intricate geometries.
-
Resistance Brazing:
-
Equipment and Setup:
-
Resistance Brazing:
- Requires specialized electrodes and fixtures to apply pressure and current.
- Equipment is generally simpler and less expensive compared to induction systems.
-
Induction Brazing:
- Requires an induction coil and power supply, which can be more complex and costly.
- Offers greater flexibility in terms of coil design to accommodate different part shapes and sizes.
-
Resistance Brazing:
-
Material Compatibility:
-
Resistance Brazing:
- Works well with conductive materials like copper, brass, and steel.
- Limited by the need for direct electrical contact with the workpiece.
-
Induction Brazing:
- Compatible with a wider range of materials, including non-conductive or low-conductivity metals when using susceptors.
- Can handle materials with varying thermal and electrical properties.
-
Resistance Brazing:
-
Advantages and Limitations:
-
Resistance Brazing:
- Advantages: Precise control, localized heating, and minimal heat-affected zones.
- Limitations: Limited to small or simple joints, requires direct electrical contact, and slower for high-volume production.
-
Induction Brazing:
- Advantages: Fast heating, suitable for complex geometries, and scalable for high-volume production.
- Limitations: Higher initial equipment cost, requires careful coil design, and may not be ideal for very small or delicate parts.
-
Resistance Brazing:
By understanding these differences, equipment and consumable purchasers can make informed decisions about which brazing method best suits their specific application requirements.
Summary Table:
Aspect | Resistance Brazing | Induction Brazing |
---|---|---|
Heating Mechanism | Heat generated by electrical resistance at the joint. | Heat generated by electromagnetic induction in the workpiece. |
Energy Efficiency | Highly efficient for small, localized joints. | Efficient for larger parts or high-volume production. |
Control and Precision | Excellent control for delicate or precision work. | Rapid heating, suitable for automated or high-speed production. |
Applications | Small components (e.g., electrical contacts, jewelry). | Larger or complex assemblies (e.g., automotive, aerospace). |
Equipment and Setup | Simpler and less expensive equipment. | More complex and costly equipment with flexible coil designs. |
Material Compatibility | Works with conductive materials (e.g., copper, brass). | Compatible with a wider range of materials, including non-conductive metals. |
Advantages | Precise control, localized heating, minimal heat-affected zones. | Fast heating, scalable for high-volume production, suitable for complex geometries. |
Limitations | Limited to small joints, requires direct electrical contact. | Higher initial cost, requires careful coil design. |
Still unsure which brazing method is best for your application? Contact our experts today for personalized advice!