Roasting and calcination are both thermal processes used in metallurgy and material processing, but they differ in their chemical nature, purpose, and the conditions under which they are performed. Roasting involves heating an ore in the presence of excess air or oxygen, often leading to oxidation and the removal of volatile impurities. For example, sulfide ores like zinc sulfide (ZnS) are roasted to convert them into oxides (ZnO). Calcination, on the other hand, involves heating a substance in the absence or limited supply of air, typically to decompose carbonates or hydroxides into oxides, releasing gases like carbon dioxide (CO₂). An example is the calcination of limestone (CaCO₃) to produce quicklime (CaO). Both processes are crucial in industrial applications but serve distinct purposes and operate under different conditions.
Key Points Explained:
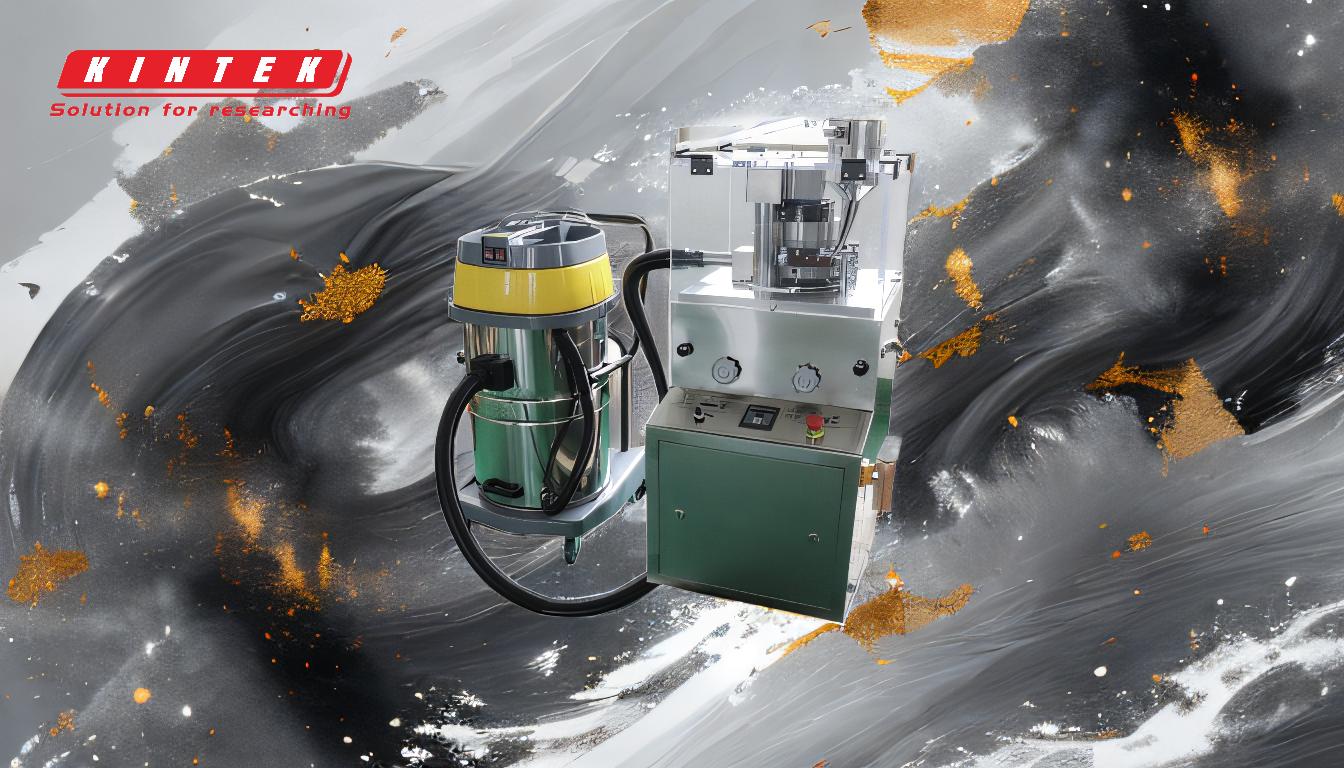
-
Definition and Purpose:
- Roasting: A process where an ore (usually sulfide) is heated in the presence of excess air or oxygen to convert it into an oxide. It is primarily used to remove volatile impurities and oxidize the ore.
- Calcination: A process where a substance (usually carbonate or hydroxide) is heated in the absence or limited supply of air to decompose it into an oxide, releasing gases like CO₂ or water vapor.
-
Chemical Reactions:
- Roasting Example: Zinc sulfide (ZnS) is roasted to produce zinc oxide (ZnO) and sulfur dioxide (SO₂). [ 2ZnS + 3O₂ \rightarrow 2ZnO + 2SO₂ ]
- Calcination Example: Limestone (CaCO₃) is calcined to produce quicklime (CaO) and carbon dioxide (CO₂). [ CaCO₃ \rightarrow CaO + CO₂ ]
-
Conditions:
- Roasting: Requires an oxidizing environment (excess air or oxygen) and is typically performed at high temperatures (500°C–1000°C).
- Calcination: Requires a controlled environment with limited or no air supply and is also performed at high temperatures (800°C–1200°C).
-
Applications:
- Roasting: Commonly used in the extraction of metals like zinc, copper, and lead from their sulfide ores.
- Calcination: Used in the production of lime (CaO) from limestone, as well as in the preparation of cement and ceramics.
-
By-products:
- Roasting: Produces gaseous by-products like sulfur dioxide (SO₂), which can be further processed to produce sulfuric acid (H₂SO₄).
- Calcination: Produces gaseous by-products like carbon dioxide (CO₂), which is often released into the atmosphere unless captured for industrial use.
-
Industrial Significance:
- Roasting: Essential for converting sulfide ores into oxides, which are easier to reduce to pure metals in subsequent processes like smelting.
- Calcination: Critical for producing materials like lime, which is used in construction, agriculture, and chemical industries.
-
Environmental Impact:
- Roasting: The release of SO₂ can lead to environmental issues like acid rain, necessitating the use of scrubbers to capture the gas.
- Calcination: The release of CO₂ contributes to greenhouse gas emissions, prompting efforts to capture and utilize CO₂ in industrial processes.
By understanding these differences, purchasers of equipment and consumables can better select the appropriate processes and materials for their specific industrial needs, ensuring efficiency and environmental compliance.
Summary Table:
Aspect | Roasting | Calcination |
---|---|---|
Definition | Heating ore in excess air/oxygen to oxidize and remove impurities. | Heating substance in limited/no air to decompose into oxides and release gases. |
Purpose | Convert sulfide ores into oxides; remove volatile impurities. | Decompose carbonates/hydroxides into oxides; release gases like CO₂. |
Chemical Reaction | 2ZnS + 3O₂ → 2ZnO + 2SO₂ | CaCO₃ → CaO + CO₂ |
Temperature | 500°C–1000°C | 800°C–1200°C |
Applications | Extraction of metals (zinc, copper, lead) from sulfide ores. | Production of lime (CaO), cement, and ceramics. |
By-products | SO₂ (can be processed into sulfuric acid). | CO₂ (often released into the atmosphere). |
Environmental Impact | SO₂ emissions can cause acid rain. | CO₂ emissions contribute to greenhouse gases. |
Need help selecting the right process for your industrial needs? Contact our experts today for tailored solutions!