Spark plasma sintering (SPS) and flash sintering are both advanced sintering techniques that utilize electrical currents to enhance the sintering process, but they differ significantly in their mechanisms, heating rates, and applications. SPS employs a pulsed direct current to generate heat internally within the material, achieving rapid densification at high heating rates (up to 1000°C/min). Flash sintering, on the other hand, relies on a continuous electric field applied during heating, causing a sudden densification at a critical temperature. While SPS is widely used for a variety of materials, including ceramics and composites, flash sintering is primarily explored for its potential to sinter materials at lower temperatures and shorter times.
Key Points Explained:
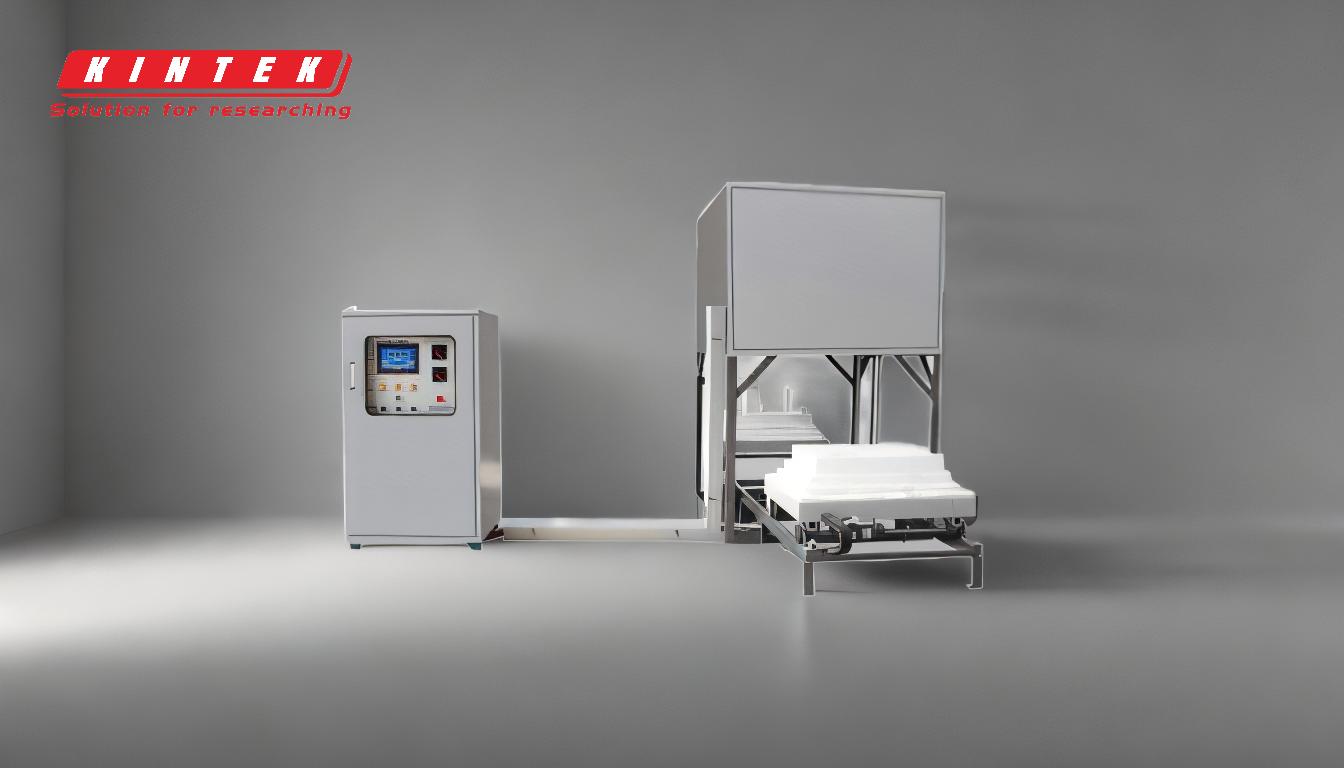
-
Mechanism of Heating:
- Spark Plasma Sintering (SPS): SPS uses a pulsed direct current that passes through the material, generating heat internally. This method activates mechanisms like surface oxide removal, electromigration, and electroplasticity, which enhance the sintering process. The internal heating ensures uniform temperature distribution and rapid densification.
- Flash Sintering: Flash sintering applies a continuous electric field during heating. At a critical temperature, the material undergoes a sudden densification due to the combined effect of Joule heating and the electric field. This process is characterized by a sharp increase in conductivity and rapid densification.
-
Heating Rate and Temperature:
- SPS: SPS is known for its extremely high heating rates, up to 1000°C/min, which allows for rapid sintering within minutes. This high heating rate is beneficial for achieving dense sintered bodies without the need for additional additives. The sintering temperature in SPS can be very high, depending on the material.
- Flash Sintering: Flash sintering typically occurs at lower temperatures compared to SPS. The process is initiated at a critical temperature where the material's conductivity increases sharply, leading to rapid densification. The heating rate in flash sintering is generally lower than in SPS, but the overall process time is shorter.
-
Applications and Material Suitability:
- SPS: SPS is versatile and can be used to sinter a wide range of materials, including ceramics, metals, and composites. It is particularly effective for sintering difficult-to-sinter materials like special ceramics and cemented carbides. The spark plasma sintering furnace is designed to handle these materials efficiently.
- Flash Sintering: Flash sintering is still an emerging technology and is primarily explored for its potential to sinter materials at lower temperatures and shorter times. It is particularly promising for sintering ceramics and other materials that are sensitive to high temperatures.
-
Uniformity and Densification:
- SPS: The internal heating in SPS ensures uniform temperature distribution, which leads to uniform densification throughout the material. This uniformity is crucial for achieving high-quality sintered products with consistent properties.
- Flash Sintering: Flash sintering can also achieve uniform densification, but the process is more dependent on the material's response to the electric field. The sudden increase in conductivity can lead to localized heating, which may affect the uniformity of the sintered product.
-
Process Time:
- SPS: Despite its high heating rates, SPS typically takes a few minutes to complete the sintering process. This is significantly shorter than traditional sintering methods, which can take several hours or even days.
- Flash Sintering: Flash sintering is known for its extremely short process time, often just a few seconds to minutes. This rapid densification is one of the key advantages of flash sintering, making it attractive for industrial applications where time is a critical factor.
In summary, while both SPS and flash sintering utilize electrical currents to enhance sintering, they differ in their heating mechanisms, rates, and applications. SPS is characterized by its high heating rates and versatility, making it suitable for a wide range of materials, whereas flash sintering offers the potential for rapid densification at lower temperatures, making it an exciting area of research for future applications.
Summary Table:
Feature | Spark Plasma Sintering (SPS) | Flash Sintering |
---|---|---|
Heating Mechanism | Pulsed direct current, internal heating | Continuous electric field |
Heating Rate | Up to 1000°C/min | Lower than SPS |
Temperature | High | Lower critical temperature |
Applications | Ceramics, metals, composites | Emerging tech, ceramics |
Uniformity | High uniformity | Dependent on material response |
Process Time | Minutes | Seconds to minutes |
Interested in advanced sintering solutions? Contact our experts today to learn more!