Thermal evaporation and e-beam evaporation are both physical vapor deposition (PVD) techniques used to create thin films, but they differ significantly in their mechanisms, operational parameters, and resulting film properties. Thermal evaporation relies on heating a material until it vaporizes, while e-beam evaporation uses a focused electron beam to achieve the same goal. The choice between these methods depends on factors such as the material being deposited, desired film properties, and specific application requirements. Below, we explore the key differences between these two techniques in detail.
Key Points Explained:
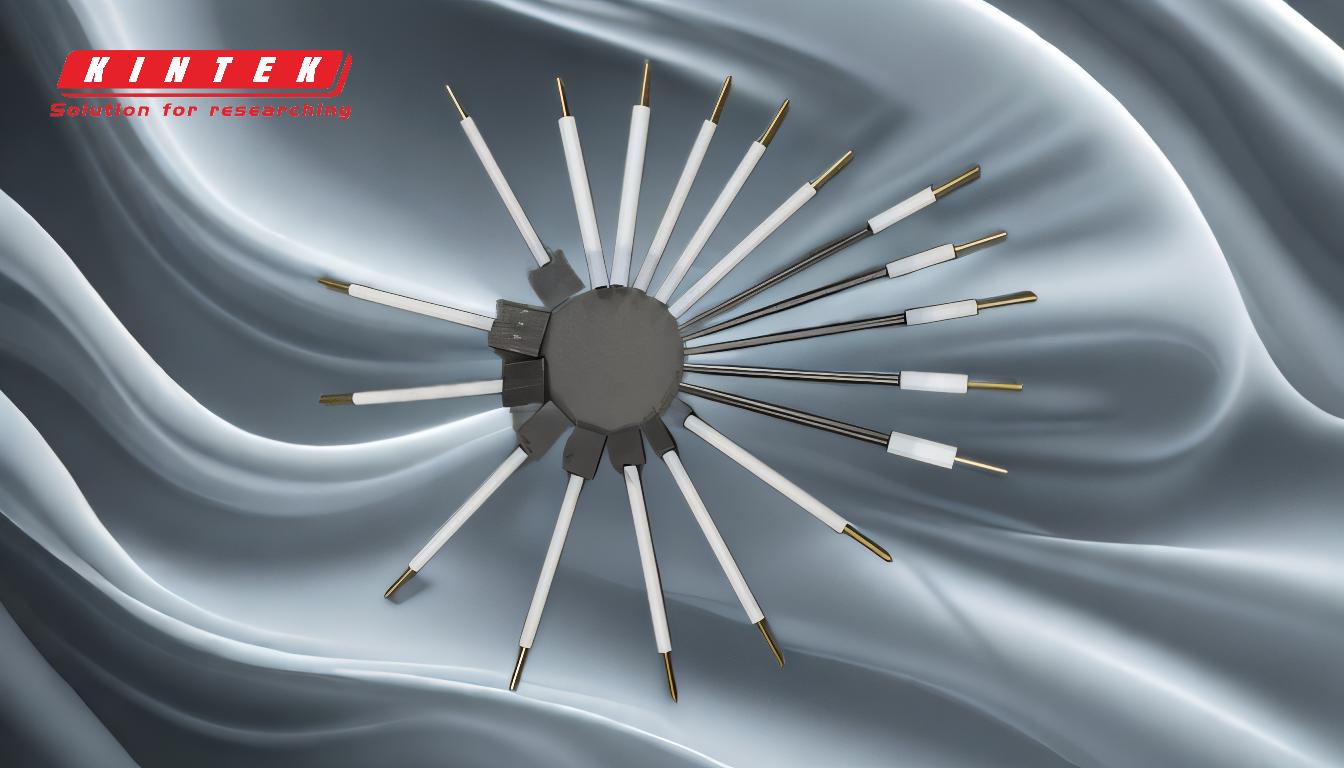
-
Mechanism of Vaporization:
- Thermal Evaporation: In this method, the material to be deposited is heated in a crucible until it reaches its vaporization temperature. The heat is typically supplied by resistive heating or induction heating. The vaporized material then travels through the vacuum chamber and condenses on the substrate.
- E-beam Evaporation: This technique uses a focused beam of high-energy electrons to locally heat and vaporize the target material. The electron beam is directed at the material in a crucible, causing it to vaporize. The vaporized material then deposits onto the substrate.
-
Vacuum Requirements:
- Thermal Evaporation: Requires a high vacuum environment to ensure that the vaporized material travels unimpeded to the substrate. This minimizes contamination and ensures high-purity films.
- E-beam Evaporation: Also operates under high vacuum conditions, similar to thermal evaporation, to achieve clean and efficient deposition.
-
Deposition Rate:
- Thermal Evaporation: Generally offers a high deposition rate, making it suitable for applications where rapid coating is necessary.
- E-beam Evaporation: Typically provides an even higher deposition rate compared to thermal evaporation, especially for materials with high melting points. This is due to the intense localized heating provided by the electron beam.
-
Film Purity and Adhesion:
- Thermal Evaporation: Produces films with high purity, but the adhesion to the substrate can be relatively low, depending on the material and substrate preparation.
- E-beam Evaporation: Offers excellent film purity and generally better adhesion to the substrate due to the higher energy of the deposited particles.
-
Energy of Deposited Species:
- Thermal Evaporation: The energy of the vaporized particles is relatively low, which can result in less dense films with larger grain sizes.
- E-beam Evaporation: The particles have higher energy, leading to denser films with smaller grain sizes. This can improve the mechanical and electrical properties of the film.
-
Material Compatibility:
- Thermal Evaporation: Best suited for materials with lower melting points. High-melting-point materials can be challenging to evaporate using this method.
- E-beam Evaporation: Capable of evaporating a wider range of materials, including those with very high melting points, due to the intense localized heating provided by the electron beam.
-
Film Homogeneity and Grain Size:
- Thermal Evaporation: Films may have less homogeneity and larger grain sizes, which can affect the film's properties.
- E-beam Evaporation: Produces more homogeneous films with smaller grain sizes, which can enhance the film's mechanical and electrical characteristics.
-
Operational Complexity and Cost:
- Thermal Evaporation: Generally simpler and less expensive to operate, making it a popular choice for many applications.
- E-beam Evaporation: More complex and costly due to the need for high-energy electron beam generation and precise control systems. However, it offers superior performance for certain materials and applications.
In summary, while both thermal evaporation and e-beam evaporation are effective PVD techniques, they are suited to different types of materials and applications. Thermal evaporation is simpler and more cost-effective, making it ideal for materials with lower melting points and applications where high deposition rates are needed. E-beam evaporation, on the other hand, excels in depositing high-melting-point materials and producing high-quality, dense films with excellent adhesion and small grain sizes. For more detailed information on thermal evaporation, you can explore further resources.
Summary Table:
Aspect | Thermal Evaporation | E-beam Evaporation |
---|---|---|
Mechanism | Heating material to vaporization | Focused electron beam vaporizes material |
Vacuum Requirements | High vacuum | High vacuum |
Deposition Rate | High | Higher, especially for high-melting materials |
Film Purity | High | Excellent |
Adhesion | Relatively low | Better due to higher particle energy |
Energy of Particles | Lower energy, less dense films | Higher energy, denser films |
Material Compatibility | Best for low-melting materials | Suitable for high-melting materials |
Film Homogeneity | Less homogeneous, larger grain sizes | More homogeneous, smaller grain sizes |
Cost & Complexity | Simpler and more cost-effective | More complex and costly |
Need help choosing the right evaporation technique for your application? Contact our experts today!