Thermal evaporation and molecular beam epitaxy (MBE) are both thin film deposition techniques, but they differ significantly in their mechanisms, applications, and the quality of films they produce. Thermal evaporation involves heating a material in a vacuum until it evaporates and then condenses onto a substrate, forming a thin film. It is suitable for materials with lower melting points and is widely used in applications like OLEDs and thin-film transistors. In contrast, MBE is a more advanced technique where atoms or molecules are evaporated in an ultra-high vacuum and directed as a beam onto a substrate, allowing for precise control over film composition and structure. MBE is ideal for creating high-quality, single-crystal films used in advanced semiconductor devices. The choice between the two depends on factors like material properties, desired film quality, and application requirements.
Key Points Explained:
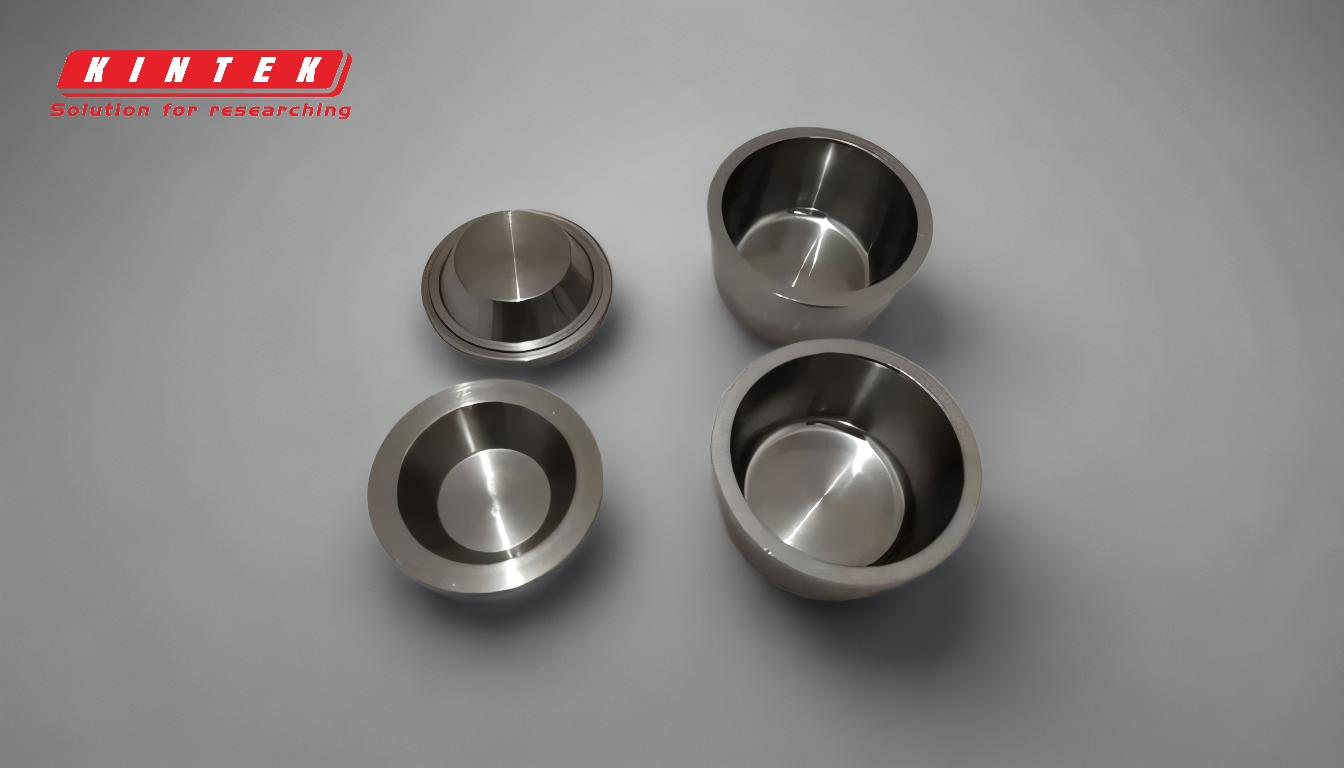
-
Mechanism of Deposition:
- Thermal Evaporation: This method uses an electric current to heat a crucible containing the source material. The material melts and evaporates, then condenses onto a substrate to form a thin film. It is a relatively simple and cost-effective process.
- Molecular Beam Epitaxy (MBE): MBE operates in an ultra-high vacuum environment. Atoms or molecules are evaporated from effusion cells and directed as a beam onto a substrate. The process allows for atomic-level control over film growth, enabling the creation of highly precise and complex structures.
-
Material Compatibility:
- Thermal Evaporation: Best suited for materials with lower melting points, such as metals and some organic compounds. It is less effective for materials requiring high temperatures or those prone to decomposition.
- MBE: Can handle a wider range of materials, including high-temperature materials like oxides and semiconductors. It is particularly effective for growing single-crystal films and complex multi-layer structures.
-
Film Quality and Precision:
- Thermal Evaporation: Produces films with good uniformity but may have lower density and higher impurity levels compared to MBE. It is less precise in controlling film thickness and composition.
- MBE: Offers superior film quality with high density, low impurities, and excellent control over thickness and composition. The ultra-high vacuum environment minimizes contamination, resulting in high-purity films.
-
Deposition Rate:
- Thermal Evaporation: Generally has a higher deposition rate, making it suitable for applications where speed is important, such as large-area coatings.
- MBE: Typically has a slower deposition rate due to the need for precise control over the growth process. This slower rate is acceptable for applications requiring high-quality, defect-free films.
-
Applications:
- Thermal Evaporation: Commonly used in the production of OLEDs, thin-film transistors, and simple metal coatings. It is favored for its simplicity and cost-effectiveness in less demanding applications.
- MBE: Used in advanced semiconductor manufacturing, such as the production of quantum wells, superlattices, and high-electron-mobility transistors (HEMTs). It is essential for applications requiring high precision and purity.
-
Equipment and Cost:
- Thermal Evaporation: Requires relatively simple and less expensive equipment. The process is easier to set up and maintain, making it accessible for a wide range of users.
- MBE: Involves complex and expensive equipment, including ultra-high vacuum systems and precise control mechanisms. The high cost and complexity limit its use to specialized applications and research settings.
-
Environmental Conditions:
- Thermal Evaporation: Operates under moderate vacuum conditions, which are easier to achieve and maintain.
- MBE: Requires ultra-high vacuum conditions to ensure minimal contamination and precise control over the deposition process. This necessitates more sophisticated vacuum systems and monitoring equipment.
In summary, while both thermal evaporation and MBE are valuable thin film deposition techniques, they cater to different needs. Thermal evaporation is more suited for simpler, cost-effective applications, whereas MBE is indispensable for high-precision, high-quality film growth in advanced technological applications. The choice between the two depends on the specific requirements of the material, desired film properties, and the intended application.
Summary Table:
Aspect | Thermal Evaporation | Molecular Beam Epitaxy (MBE) |
---|---|---|
Mechanism | Heating material in a vacuum to evaporate and condense onto a substrate. | Atoms/molecules evaporated in ultra-high vacuum and directed as a beam onto a substrate. |
Material Compatibility | Best for low-melting-point materials (e.g., metals, organic compounds). | Handles high-temperature materials (e.g., oxides, semiconductors) and complex multi-layer films. |
Film Quality | Good uniformity, lower density, higher impurities. | High density, low impurities, precise control over thickness and composition. |
Deposition Rate | Higher rate, suitable for large-area coatings. | Slower rate, ideal for high-quality, defect-free films. |
Applications | OLEDs, thin-film transistors, simple metal coatings. | Advanced semiconductor devices, quantum wells, superlattices, HEMTs. |
Equipment and Cost | Simple, cost-effective equipment. | Complex, expensive ultra-high vacuum systems. |
Environmental Conditions | Moderate vacuum conditions. | Ultra-high vacuum conditions for minimal contamination. |
Need help selecting the right thin film deposition method? Contact our experts today for personalized advice!