Thermal evaporation and e-beam evaporation are two distinct thin-film deposition techniques used in various industries, including semiconductor manufacturing, optics, and materials science. The primary difference lies in the method of heating the source material: thermal evaporation uses electric current to heat a crucible, while e-beam evaporation employs a high-energy electron beam to directly heat the material. Thermal evaporation is suitable for lower-melting-point materials, whereas e-beam evaporation excels with high-melting-point materials like oxides. Additionally, e-beam evaporation offers denser coatings, higher deposition rates, and lower impurity risks compared to thermal evaporation.
Key Points Explained:
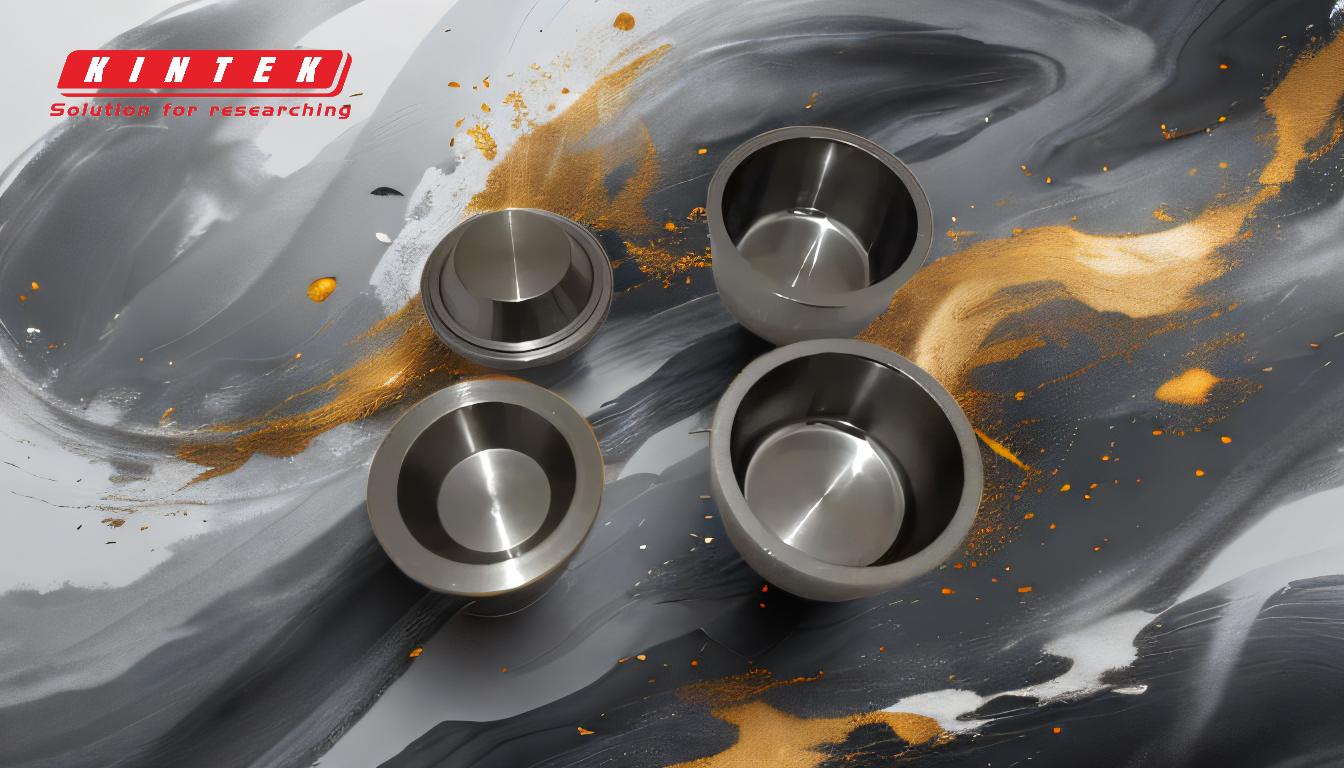
-
Heating Mechanism:
- Thermal Evaporation: Uses an electric current to heat a crucible, which then melts and evaporates the source material. This method relies on resistive heating.
- E-beam Evaporation: Utilizes a high-energy electron beam to directly heat the source material, transferring kinetic energy to cause evaporation. This method is more precise and localized.
-
Suitability for Materials:
- Thermal Evaporation: Best suited for materials with lower melting temperatures, such as aluminum, gold, and silver. It is less effective for high-melting-point materials.
- E-beam Evaporation: Capable of handling high-melting-point materials like oxides, ceramics, and refractory metals. This makes it versatile for a wider range of applications.
-
Film Quality:
- Thermal Evaporation: Produces thin films that may be less dense and have higher impurity levels due to crucible contamination.
- E-beam Evaporation: Results in denser, higher-quality thin films with fewer impurities, as the electron beam directly targets the material without crucible contact.
-
Deposition Rate:
- Thermal Evaporation: Generally has a lower deposition rate, which can be a limitation for high-throughput applications.
- E-beam Evaporation: Offers a higher deposition rate, making it more efficient for large-scale or time-sensitive projects.
-
Operational Complexity and Cost:
- Thermal Evaporation: Simpler and less expensive to operate, making it a cost-effective choice for applications requiring lower-melting-point materials.
- E-beam Evaporation: More complex and costly due to the need for high-energy electron beams and sophisticated control systems. However, the benefits in film quality and material versatility often justify the higher cost.
-
Applications:
- Thermal Evaporation: Commonly used in applications where cost and simplicity are prioritized, such as in the deposition of metallic coatings for mirrors, solar cells, and simple electronic components.
- E-beam Evaporation: Preferred for advanced applications requiring high-purity, dense films, such as in semiconductor devices, optical coatings, and specialized materials research.
By understanding these key differences, equipment and consumable purchasers can make informed decisions based on the specific requirements of their projects, such as material compatibility, film quality, deposition rate, and budget constraints.
Summary Table:
Aspect | Thermal Evaporation | E-beam Evaporation |
---|---|---|
Heating Mechanism | Electric current heats a crucible to evaporate the material. | High-energy electron beam directly heats the material for evaporation. |
Material Suitability | Best for lower-melting-point materials (e.g., aluminum, gold, silver). | Ideal for high-melting-point materials (e.g., oxides, ceramics, refractory metals). |
Film Quality | Less dense films with higher impurity risks due to crucible contamination. | Denser, high-quality films with fewer impurities. |
Deposition Rate | Lower deposition rate, suitable for smaller-scale applications. | Higher deposition rate, ideal for large-scale or time-sensitive projects. |
Operational Cost | Simpler and more cost-effective for lower-melting-point materials. | More complex and costly but offers superior film quality and material versatility. |
Applications | Used in cost-sensitive applications like mirrors, solar cells, and simple electronics. | Preferred for advanced applications like semiconductors, optical coatings, and research. |
Need help choosing the right thin-film deposition technique? Contact our experts today for tailored solutions!