Two-plate and three-plate moulds are commonly used in injection moulding, each with distinct design features, advantages, and applications. The primary difference lies in their structure and functionality, which directly impacts their cost, cycle time, and suitability for specific manufacturing needs. Two-plate moulds are simpler, less expensive, and have shorter cycle times, making them ideal for straightforward projects. Three-plate moulds, on the other hand, are more complex, costlier, and offer greater flexibility in part ejection and runner system placement, making them suitable for intricate designs.
Key Points Explained:
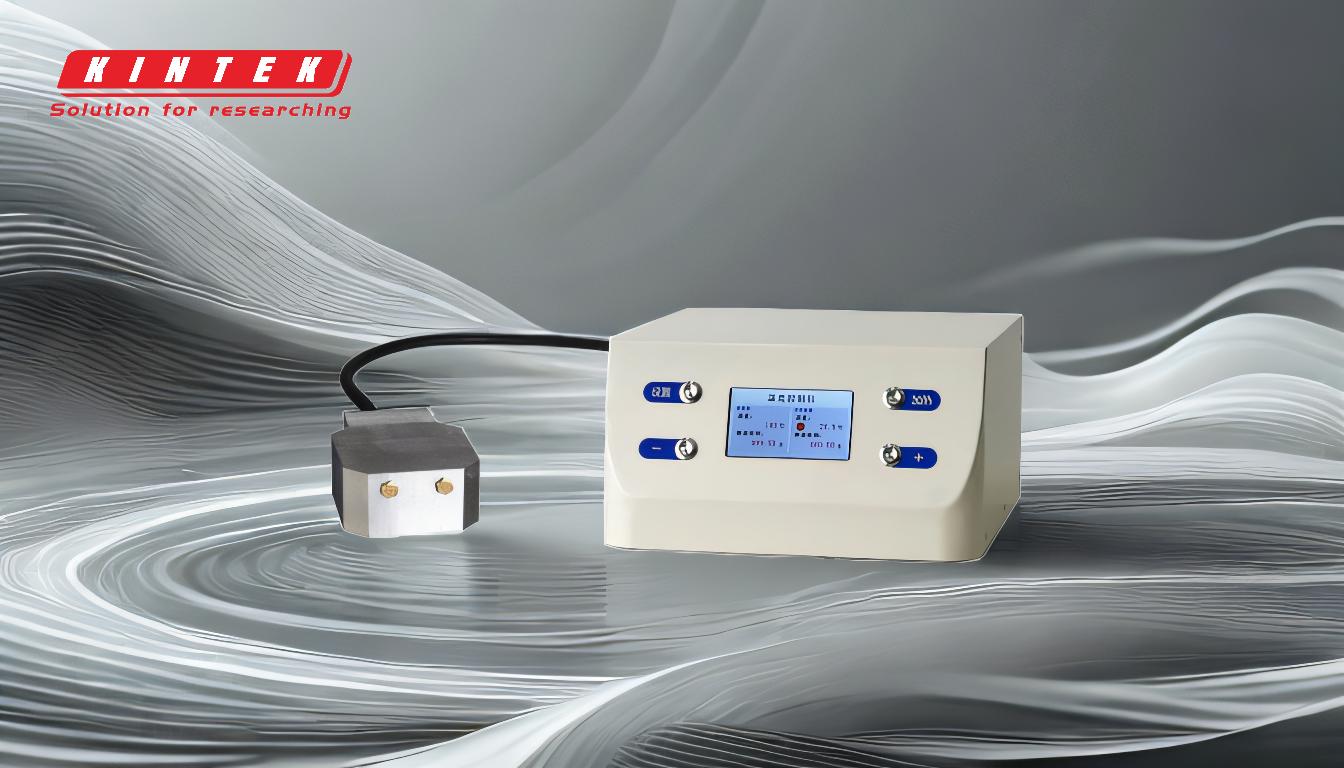
-
Design Complexity:
- Two-Plate Mould: Consists of two main plates—the cavity plate and the core plate. The design is straightforward, with fewer moving parts, making it easier to manufacture and maintain.
- Three-Plate Mould: Incorporates an additional plate (the runner plate) between the cavity and core plates. This extra plate allows for more complex runner systems and part ejection mechanisms, increasing design flexibility but also adding complexity.
-
Cost:
- Two-Plate Mould: Due to its simpler design, a two-plate mould is generally less expensive to produce. The reduced number of components lowers both material and machining costs.
- Three-Plate Mould: The added complexity of the third plate and associated mechanisms makes three-plate moulds more expensive. The cost is further influenced by the need for precise alignment and additional maintenance.
-
Cycle Time:
- Two-Plate Mould: With fewer moving parts, the cycle time is shorter, leading to faster production rates. This efficiency is beneficial for high-volume manufacturing.
- Three-Plate Mould: The additional plate and mechanisms increase the cycle time. While this may reduce production speed, it allows for more intricate designs and better part ejection, which can be critical for certain applications.
-
Runner System:
- Two-Plate Mould: The runner system is typically located on the same plane as the part, which can limit design options and increase material waste.
- Three-Plate Mould: The runner system is separated from the part by the additional plate, allowing for more flexible runner placement and reducing material waste. This separation also enables automatic degating, which can improve part quality.
-
Part Ejection:
- Two-Plate Mould: Parts and runners are ejected together, which can complicate the ejection process and increase the risk of part damage.
- Three-Plate Mould: The additional plate allows for separate ejection of parts and runners, reducing the risk of damage and improving overall part quality.
-
Applications:
- Two-Plate Mould: Best suited for simple parts with straightforward designs and high-volume production. Commonly used in industries where cost and speed are critical factors.
- Three-Plate Mould: Ideal for complex parts requiring intricate runner systems and precise ejection. Often used in industries where part quality and design flexibility are prioritized over cost and cycle time.
By understanding these key differences, manufacturers can make informed decisions about which type of mould best suits their specific production requirements, balancing cost, cycle time, and design complexity.
Summary Table:
Feature | Two-Plate Mould | Three-Plate Mould |
---|---|---|
Design Complexity | Simpler design with fewer moving parts | More complex with an additional runner plate |
Cost | Less expensive due to simpler design | More expensive due to added complexity |
Cycle Time | Shorter cycle time for faster production | Longer cycle time for intricate designs |
Runner System | Limited design options, more waste | Flexible runner placement, less waste |
Part Ejection | Parts and runners ejected together | Separate ejection, reducing part damage |
Applications | Ideal for simple, high-volume production | Best for complex parts with precise needs |
Still unsure which mould type suits your project? Contact our experts today for personalized advice!