Calcination and roasting are two distinct thermal treatment processes used in metallurgy and materials processing, each serving different purposes. Calcination involves heating a substance to high temperatures in the absence or limited supply of air or oxygen, primarily to remove volatile components, decompose compounds, or drive off moisture. Roasting, on the other hand, involves heating an ore or concentrate in the presence of excess air or oxygen, often to convert sulfides into oxides, remove sulfur, or oxidize impurities. While both processes involve heat treatment, their objectives, chemical reactions, and applications differ significantly.
Key Points Explained:
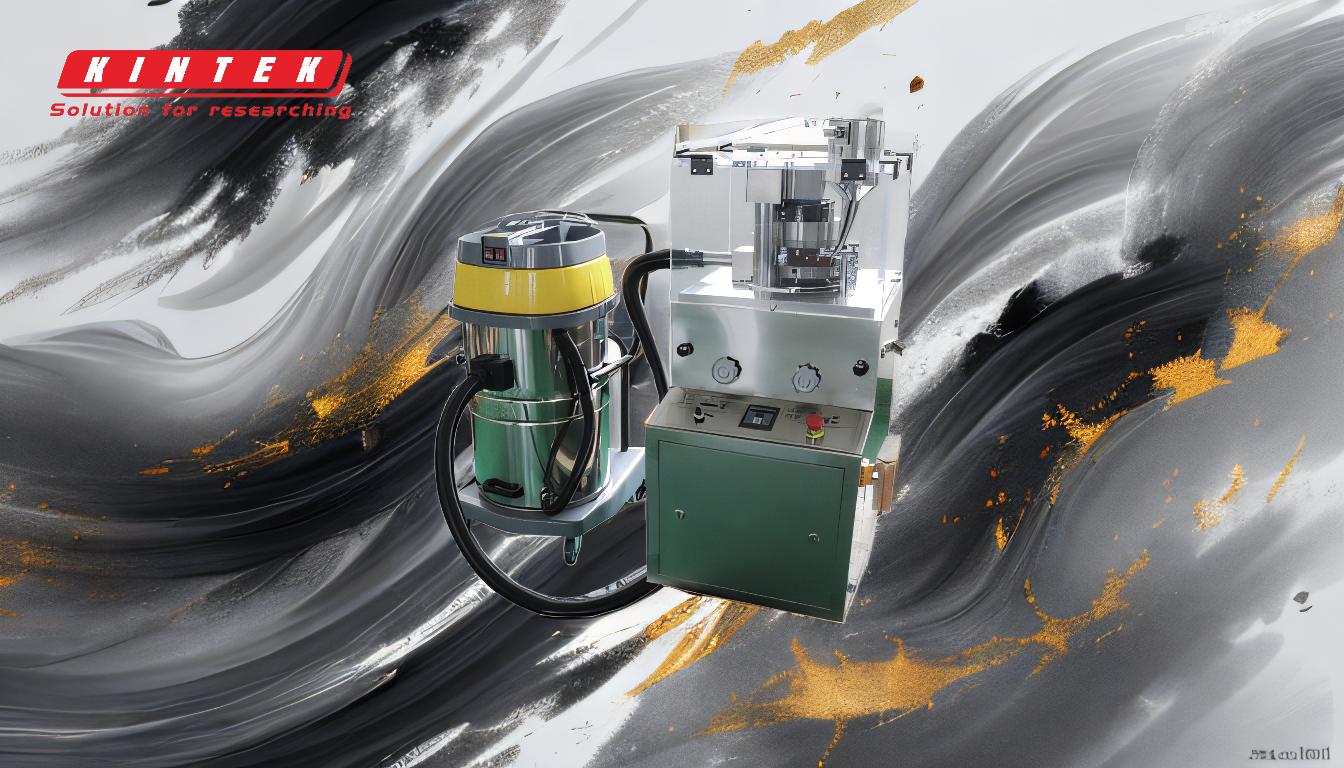
-
Definition and Purpose:
-
Calcination:
- Calcination is the process of heating a material to a high temperature (typically below its melting point) in the absence or limited supply of air or oxygen.
- The primary purpose is to remove volatile substances, decompose compounds, or drive off moisture. For example, limestone (CaCO₃) is calcined to produce lime (CaO) and carbon dioxide (CO₂).
-
Roasting:
- Roasting involves heating an ore or concentrate in the presence of excess air or oxygen, often at high temperatures.
- The main goal is to oxidize or chemically alter the material, such as converting metal sulfides into oxides or removing sulfur and other impurities. For instance, zinc sulfide (ZnS) is roasted to produce zinc oxide (ZnO) and sulfur dioxide (SO₂).
-
Calcination:
-
Chemical Reactions:
-
Calcination:
- Calcination typically involves decomposition reactions. For example:
- CaCO₃ (limestone) → CaO (lime) + CO₂ (carbon dioxide)
- It may also involve the removal of water of crystallization, as in the case of gypsum (CaSO₄·2H₂O) being calcined to produce plaster of Paris (CaSO₄·0.5H₂O).
- Calcination typically involves decomposition reactions. For example:
-
Roasting:
- Roasting involves oxidation reactions. For example:
- 2ZnS (zinc sulfide) + 3O₂ → 2ZnO (zinc oxide) + 2SO₂ (sulfur dioxide)
- It may also involve the removal of volatile impurities, such as arsenic or antimony, in the form of their oxides.
- Roasting involves oxidation reactions. For example:
-
Calcination:
-
Atmosphere:
-
Calcination:
- Calcination is typically carried out in the absence or limited supply of air or oxygen. This controlled atmosphere prevents oxidation and allows for the decomposition of compounds.
-
Roasting:
- Roasting is conducted in the presence of excess air or oxygen. The oxidizing atmosphere is essential for the chemical reactions that convert sulfides to oxides or remove impurities.
-
Calcination:
-
Temperature:
-
Calcination:
- The temperature for calcination is usually below the melting point of the material being treated. For example, limestone is calcined at around 900°C to 1000°C.
-
Roasting:
- Roasting temperatures can vary widely but are often higher than those used in calcination, depending on the material and the desired reaction. For example, zinc sulfide roasting occurs at temperatures around 900°C to 1100°C.
-
Calcination:
-
Applications:
-
Calcination:
- Calcination is commonly used in the production of cement, lime, and plaster of Paris. It is also used in the preparation of catalysts, the decomposition of carbonates, and the removal of bound moisture from minerals.
-
Roasting:
- Roasting is primarily used in metallurgical processes to prepare metal ores for further processing, such as smelting. It is essential in the extraction of metals like zinc, copper, and lead from their sulfide ores.
-
Calcination:
-
By-products:
-
Calcination:
- The by-products of calcination are typically gases, such as carbon dioxide or water vapor, which are driven off during the process.
-
Roasting:
- Roasting often produces gaseous by-products like sulfur dioxide, which can be captured and used in the production of sulfuric acid. Solid by-products may include metal oxides or other compounds formed during the oxidation process.
-
Calcination:
-
Environmental Impact:
-
Calcination:
- Calcination can release carbon dioxide, contributing to greenhouse gas emissions, especially in industries like cement production. However, the process itself is relatively clean if the gases are properly managed.
-
Roasting:
- Roasting can produce significant amounts of sulfur dioxide, which is a major air pollutant. Modern roasting processes often include gas scrubbing systems to capture and neutralize these emissions.
-
Calcination:
-
Equipment:
-
Calcination:
- Calcination is typically carried out in rotary kilns, shaft kilns, or fluidized bed reactors, depending on the material and scale of production.
-
Roasting:
- Roasting is often performed in multiple hearth furnaces, fluidized bed roasters, or flash roasters, which are designed to handle the high temperatures and oxidizing conditions required.
-
Calcination:
In summary, while both calcination and roasting involve the application of heat to materials, they differ in their objectives, chemical reactions, and the environments in which they are conducted. Calcination is primarily a decomposition process carried out in a limited oxygen environment, whereas roasting is an oxidation process that requires excess oxygen to achieve its goals. Understanding these differences is crucial for selecting the appropriate thermal treatment process for a given material or application.
Summary Table:
Aspect | Calcination | Roasting |
---|---|---|
Definition | Heating in the absence/limited air to remove volatiles or decompose compounds. | Heating in excess air/oxygen to oxidize or chemically alter materials. |
Purpose | Remove moisture, decompose compounds, or drive off volatile substances. | Convert sulfides to oxides, remove sulfur, or oxidize impurities. |
Chemical Reactions | Decomposition (e.g., CaCO₃ → CaO + CO₂). | Oxidation (e.g., 2ZnS + 3O₂ → 2ZnO + 2SO₂). |
Atmosphere | Limited or no oxygen. | Excess oxygen or air. |
Temperature | Below melting point (e.g., 900°C–1000°C for limestone). | Often higher than calcination (e.g., 900°C–1100°C for zinc sulfide). |
Applications | Cement, lime, plaster of Paris, catalyst preparation. | Metallurgical processes (e.g., zinc, copper, lead extraction). |
By-products | Gases like CO₂ or water vapor. | Gases like SO₂ (used in sulfuric acid production) and metal oxides. |
Environmental Impact | CO₂ emissions (greenhouse gases). | SO₂ emissions (air pollutants, often scrubbed). |
Equipment | Rotary kilns, shaft kilns, fluidized bed reactors. | Multiple hearth furnaces, fluidized bed roasters, flash roasters. |
Need help choosing the right thermal treatment process for your materials? Contact our experts today for tailored solutions!