Welding and vacuum brazing are both joining processes used in manufacturing, but they differ significantly in their methods, applications, and outcomes. Welding involves melting the base metals to fuse them together, often requiring high heat and sometimes filler materials. In contrast, vacuum brazing uses a filler metal that melts at a lower temperature than the base metals, bonding them without melting the base materials. This process occurs in a controlled environment, typically inside a vacuum brazing furnace, to prevent oxidation and ensure a clean, strong joint. Below, we’ll explore the key differences between these two processes in detail.
Key Points Explained:
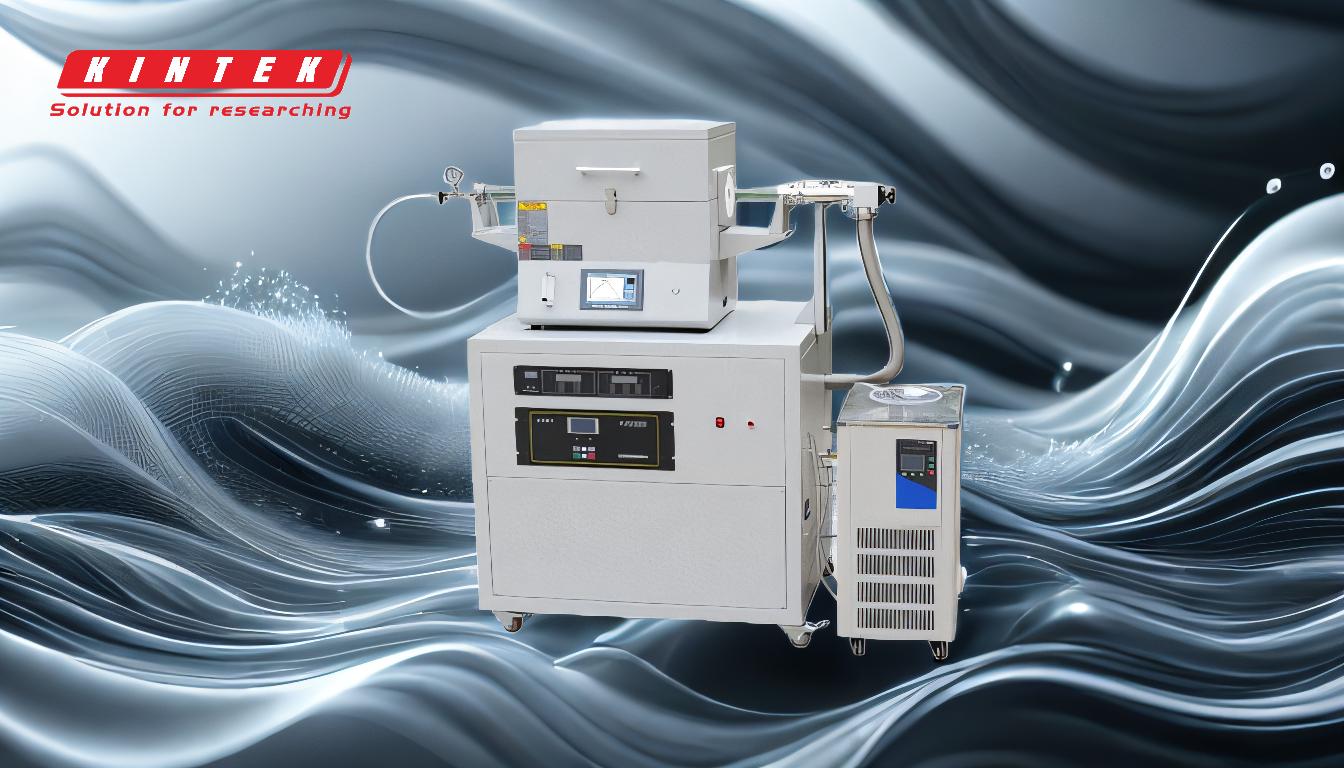
-
Definition and Process:
- Welding: Welding is a fabrication process that joins materials, usually metals or thermoplastics, by melting the base materials and often adding a filler material to form a molten pool. The pool cools to form a strong joint.
- Vacuum Brazing: Vacuum brazing is a joining process where a filler metal is melted and flowed into the joint between two or more base materials without melting the base metals. This process is conducted in a vacuum environment to eliminate oxidation and contamination.
-
Temperature Requirements:
- Welding: Welding typically requires very high temperatures, often exceeding the melting point of the base metals. This can lead to significant heat-affected zones (HAZ) and potential distortion of the materials.
- Vacuum Brazing: Brazing is performed at lower temperatures than welding, as only the filler metal needs to melt. This reduces the risk of warping or damaging the base materials, making it suitable for delicate or complex components.
-
Filler Material:
- Welding: In welding, the filler material (if used) often has a similar composition to the base metals. The filler is melted along with the base materials to create a homogeneous joint.
- Vacuum Brazing: The filler metal used in brazing has a lower melting point than the base metals. Common filler materials include silver, copper, and nickel alloys, which flow into the joint by capillary action.
-
Joint Strength and Integrity:
- Welding: Welded joints are typically as strong as or stronger than the base materials, as the joint becomes a single, continuous piece of metal.
- Vacuum Brazing: Brazed joints are strong but may not match the strength of a welded joint. However, brazing provides excellent leak-tight seals and is ideal for applications requiring precision and minimal distortion.
-
Applications:
- Welding: Welding is widely used in industries such as construction, automotive, and shipbuilding, where high-strength joints are critical.
- Vacuum Brazing: Vacuum brazing is commonly used in industries requiring high precision and cleanliness, such as aerospace, medical devices, and electronics. It is particularly suited for joining dissimilar metals or complex assemblies.
-
Equipment and Environment:
- Welding: Welding can be performed using various methods (e.g., arc welding, gas welding, laser welding) and typically does not require a controlled atmosphere.
- Vacuum Brazing: This process requires specialized equipment, such as a vacuum brazing furnace, to create an oxygen-free environment. This ensures clean, oxidation-free joints, which are critical for high-performance applications.
-
Advantages and Limitations:
- Welding: Advantages include high joint strength and versatility. Limitations include potential distortion, heat-affected zones, and difficulty in joining dissimilar materials.
- Vacuum Brazing: Advantages include minimal distortion, ability to join dissimilar materials, and clean, oxidation-free joints. Limitations include lower joint strength compared to welding and the need for specialized equipment.
In summary, welding and vacuum brazing serve different purposes and are chosen based on the specific requirements of the application. Welding is ideal for high-strength applications, while vacuum brazing excels in precision joining, especially for delicate or complex components. The use of a vacuum brazing furnace ensures a controlled environment, making it a preferred choice for industries demanding high-quality, contamination-free joints.
Summary Table:
Aspect | Welding | Vacuum Brazing |
---|---|---|
Process | Melts base metals to fuse them together | Uses filler metal to bond without melting base materials |
Temperature | High temperatures, exceeding base metal melting points | Lower temperatures, only filler metal melts |
Filler Material | Similar composition to base metals | Lower melting point (e.g., silver, copper, nickel alloys) |
Joint Strength | As strong or stronger than base metals | Strong but slightly weaker than welded joints; excellent leak-tight seals |
Applications | Construction, automotive, shipbuilding | Aerospace, medical devices, electronics |
Equipment | No controlled atmosphere required | Requires vacuum brazing furnace for oxygen-free environment |
Advantages | High joint strength, versatile | Minimal distortion, clean joints, suitable for dissimilar materials |
Limitations | Potential distortion, heat-affected zones | Lower joint strength, specialized equipment needed |
Need help choosing the right joining process for your application? Contact our experts today!