Cleaning-In-Place (CIP) systems are essential in industries like food, beverage, and pharmaceuticals for maintaining hygiene and operational efficiency. Wet bag and dry bag CIP systems are two common configurations, each with distinct operational characteristics and applications. Wet bag CIP systems involve submerging the spray device in a cleaning solution, making them suitable for smaller-scale operations with frequent cleaning cycles. Dry bag CIP systems, on the other hand, keep the spray device dry when not in use, making them ideal for larger-scale operations with less frequent cleaning. The choice between the two depends on factors such as production scale, cleaning frequency, and operational requirements.
Key Points Explained:
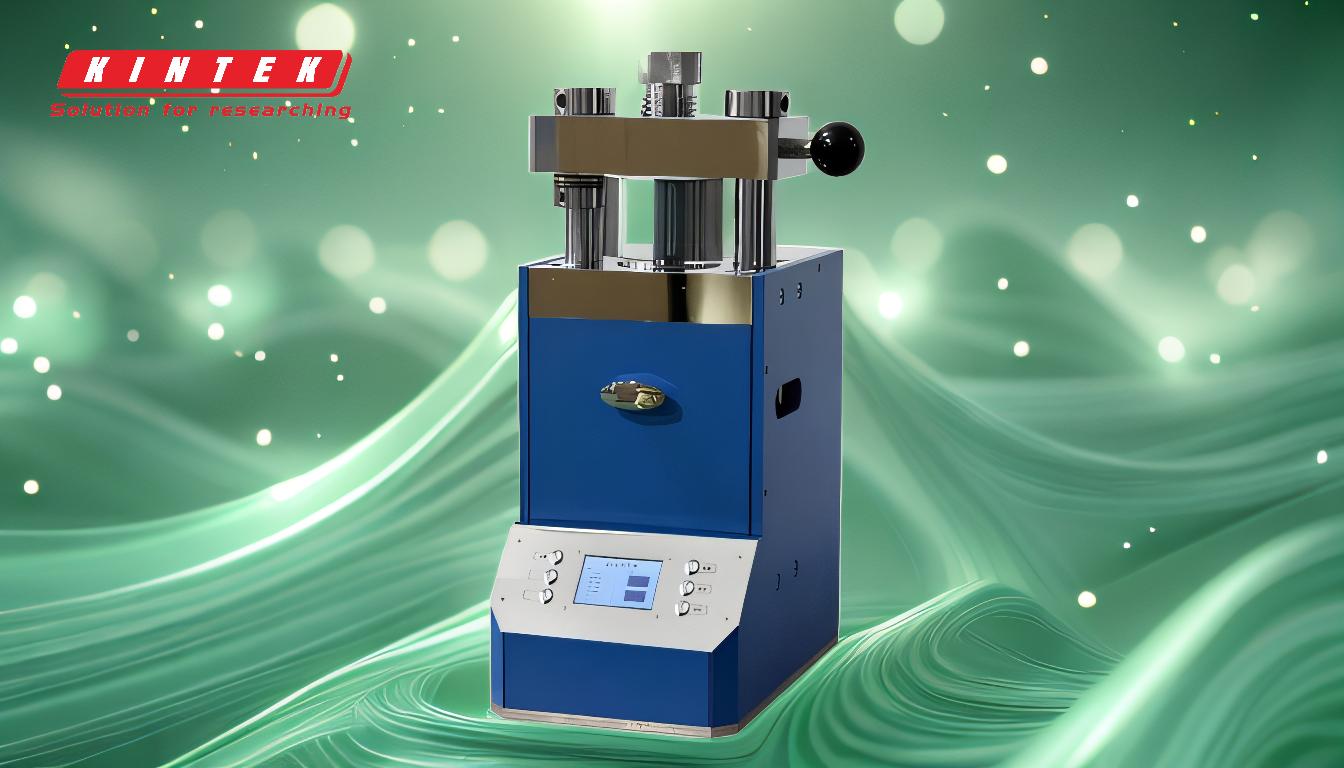
-
Definition and Operation of Wet Bag CIP:
- Wet bag CIP systems are designed with the spray device submerged in a cleaning solution when not in use. This ensures that the spray device is always ready for immediate use, which is particularly beneficial for operations requiring frequent cleaning cycles.
- The submerged nature of the spray device in wet bag systems helps in maintaining the cleanliness of the device itself, reducing the risk of contamination.
- Wet bag systems are typically used in smaller-scale operations where the frequency of cleaning is high, and the volume of cleaning solution required is manageable.
-
Definition and Operation of Dry Bag CIP:
- Dry bag CIP systems keep the spray device dry when not in use. The cleaning solution is only introduced into the system during the cleaning cycle, which helps in conserving cleaning agents and reducing the risk of contamination from stagnant cleaning solutions.
- Dry bag systems are more suitable for larger-scale operations where the cleaning cycles are less frequent, and the volume of cleaning solution required is significant.
- The dry nature of the spray device in dry bag systems reduces the risk of microbial growth and contamination, making them ideal for industries with stringent hygiene requirements.
-
Comparison of Cleaning Efficiency:
- Wet bag CIP systems are generally more efficient for operations requiring frequent cleaning due to the immediate availability of the cleaning solution. However, the constant exposure to cleaning solutions can lead to wear and tear of the spray device over time.
- Dry bag CIP systems, while less efficient for frequent cleaning cycles, offer better conservation of cleaning agents and reduced wear on the spray device. They are more suitable for operations where cleaning cycles are spaced out, and the risk of contamination from stagnant cleaning solutions is a concern.
-
Maintenance and Operational Considerations:
- Wet bag CIP systems require regular maintenance to ensure the cleaning solution remains effective and the spray device is in good condition. The constant exposure to cleaning solutions can lead to corrosion and other forms of degradation over time.
- Dry bag CIP systems, on the other hand, require less frequent maintenance due to the reduced exposure of the spray device to cleaning solutions. However, they may require more complex plumbing and control systems to manage the introduction and removal of cleaning solutions during each cycle.
-
Application in Different Industries:
- Wet bag CIP systems are commonly used in industries with high-frequency cleaning requirements, such as small-scale food and beverage production, where the volume of cleaning solution is manageable, and the need for immediate cleaning is critical.
- Dry bag CIP systems are preferred in larger-scale operations, such as large-scale pharmaceutical manufacturing or dairy processing, where the volume of cleaning solution is significant, and the cleaning cycles are less frequent. The reduced risk of contamination and better conservation of cleaning agents make dry bag systems more suitable for these applications.
In conclusion, the choice between wet bag and dry bag CIP systems depends on the specific operational requirements of the industry, including the scale of production, frequency of cleaning cycles, and hygiene standards. Wet bag systems offer immediate cleaning readiness and are suitable for smaller-scale operations, while dry bag systems provide better conservation of cleaning agents and reduced contamination risks, making them ideal for larger-scale operations.
Summary Table:
Feature | Wet Bag CIP Systems | Dry Bag CIP Systems |
---|---|---|
Spray Device State | Submerged in cleaning solution | Dry when not in use |
Cleaning Frequency | High-frequency cleaning cycles | Less frequent cleaning cycles |
Operational Scale | Smaller-scale operations | Larger-scale operations |
Maintenance | Regular maintenance required | Less frequent maintenance |
Applications | Small-scale food, beverage production | Large-scale pharmaceutical, dairy production |
Contamination Risk | Moderate | Low |
Cleaning Efficiency | Immediate cleaning readiness | Better conservation of cleaning agents |
Need help choosing the right CIP system for your operations? Contact our experts today to get tailored advice!