Graphite furnaces are highly effective for high-temperature applications such as sintering, graphitizing, and pyrolysis. However, they come with several disadvantages that can impact their practicality and usability. These include the need for heavy power supplies and water cooling systems, making them unsuitable for portable applications. Additionally, they may require frequent maintenance, have limitations in capacity for large-scale production, and involve higher operational costs due to energy consumption and component wear. These factors make graphite furnaces less ideal for certain industrial or research settings, particularly where portability, cost-efficiency, or rapid heating are critical.
Key Points Explained:
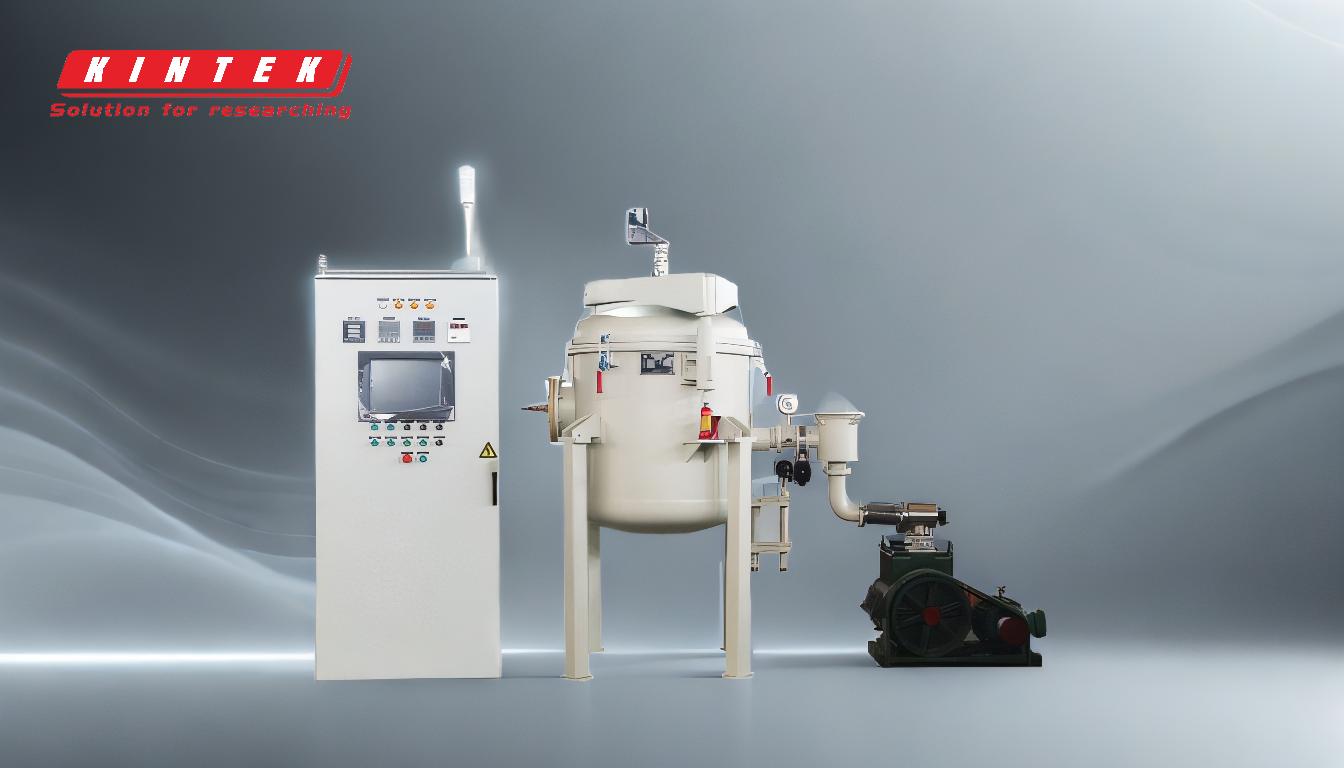
-
Heavy Power Supplies and Water Cooling Systems
- Graphite furnaces require substantial power supplies to generate the extremely high temperatures they are known for. This makes them energy-intensive and often necessitates specialized electrical infrastructure.
- Water cooling systems are essential to manage the heat generated during operation, adding to the complexity and cost of the setup. These systems also increase the overall footprint of the furnace, making it less suitable for portable or space-constrained environments.
-
Unsuitability for Portable Instrumentation
- Due to the need for heavy power supplies and water cooling, graphite furnaces are not practical for portable applications. This limits their use in fieldwork or situations where mobility is required.
- The reliance on external cooling and power systems further restricts their adaptability in environments where such resources are not readily available.
-
Frequent Maintenance and Component Wear
- Graphite components, such as crucibles, are subject to wear and tear from prolonged exposure to high temperatures. This necessitates frequent replacement, increasing operational costs and downtime.
- The maintenance requirements can be labor-intensive and may require specialized knowledge, adding to the overall cost of ownership.
-
Limitations in Capacity for Large-Scale Production
- Graphite furnaces may have limitations in terms of capacity, making them less suitable for large-scale industrial production. This can be a significant drawback for industries requiring high throughput.
- The slower melting times compared to other furnace types can further reduce efficiency in large-scale operations.
-
Higher Operational Costs
- The energy consumption required to achieve and maintain high temperatures can lead to significant operational costs. This includes both electricity for heating and water for cooling systems.
- The need for frequent replacement of components like crucibles adds to the ongoing expenses, making graphite furnaces a costly option over time.
-
Space Requirements
- Graphite furnaces, along with their associated cooling and power systems, can take up a considerable amount of space. This can be a disadvantage in environments where space is at a premium.
- The large footprint may also complicate installation and integration into existing facilities.
-
Expertise Required for Operation
- Operating a graphite furnace effectively requires specialized knowledge and experience. This can limit the pool of qualified operators and increase training costs.
- The complexity of adjusting heating degrees and managing the furnace's systems means that inexperienced operators may struggle to achieve optimal performance.
In summary, while graphite furnaces offer significant advantages in terms of high-temperature capabilities, their disadvantages—such as high operational costs, maintenance requirements, and unsuitability for portable use—make them less ideal for certain applications. Understanding these drawbacks is crucial for potential purchasers to make informed decisions based on their specific needs and constraints.
Summary Table:
Disadvantage | Key Details |
---|---|
Heavy Power Supplies & Water Cooling | Requires substantial power and water cooling, increasing complexity and cost. |
Unsuitability for Portable Applications | Not practical for fieldwork due to reliance on external systems. |
Frequent Maintenance & Component Wear | High wear and tear on components, leading to frequent replacements. |
Limited Capacity for Large-Scale Production | Not ideal for high-throughput industrial applications. |
Higher Operational Costs | Energy-intensive and costly due to electricity and water cooling. |
Space Requirements | Large footprint complicates installation in space-constrained environments. |
Expertise Required for Operation | Specialized knowledge needed, increasing training and operational costs. |
Need help deciding if a graphite furnace is right for your application? Contact our experts today for personalized advice!