The sintering process plays a crucial role in determining the flexural strength of translucent monolithic zirconia. By applying heat and sometimes pressure, sintering reduces porosity and increases density, which directly impacts the material's mechanical properties. Optimal sintering temperatures, such as 1500℃, maximize strength, while deviations can lead to grain growth and reduced strength. The transformation of zirconia's crystalline structure during sintering also contributes to its enhanced mechanical and optical properties. Understanding the relationship between sintering conditions and flexural strength is essential for producing high-performance zirconia restorations.
Key Points Explained:
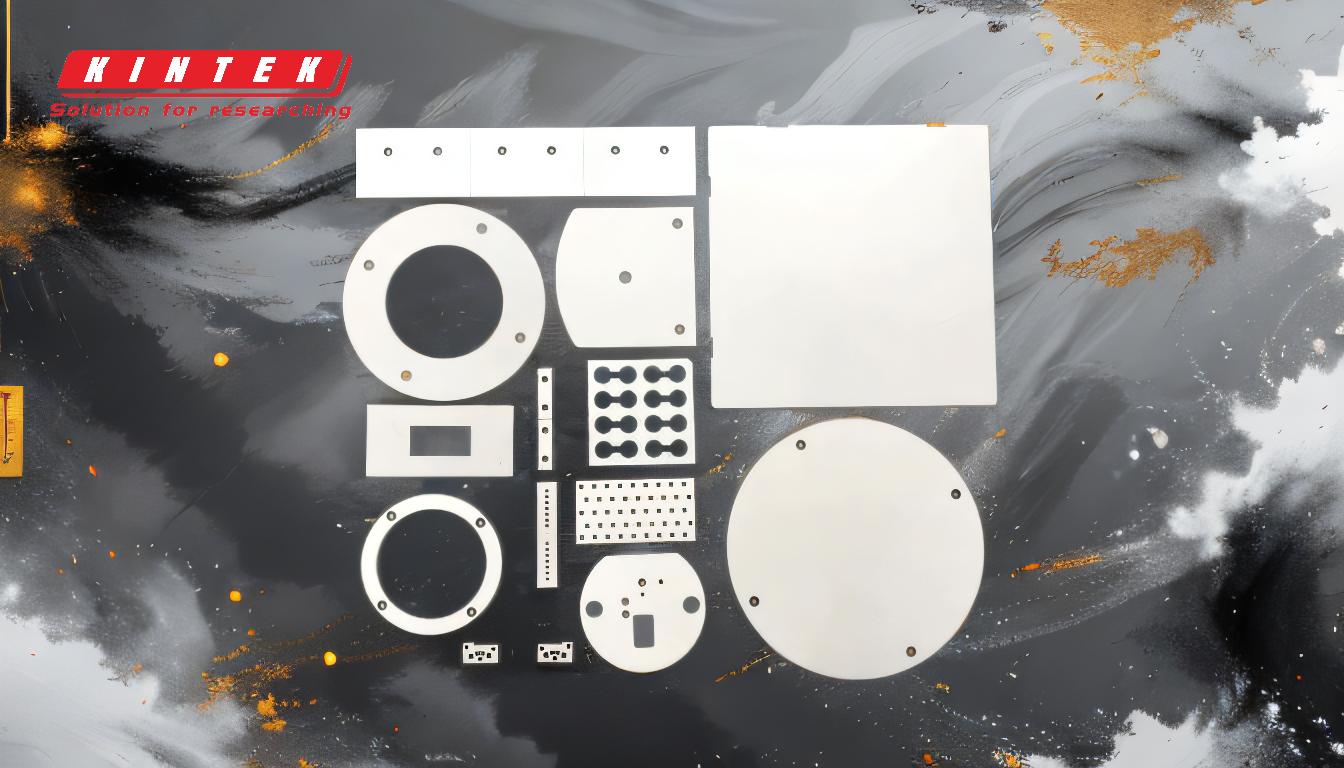
-
Sintering Process Overview:
- Sintering involves heating zirconia, often with pressure, to fuse particles into a solid mass.
- This process reduces porosity and increases density, enhancing the material's mechanical properties, including flexural strength.
-
Effect of Temperature on Flexural Strength:
- Optimal Temperature: Sintering at around 1500℃ maximizes the flexural strength of zirconia. This temperature ensures a balance between reducing porosity and preventing excessive grain growth.
- Temperature Deviations: Deviating by 150℃ above or below the optimal temperature can lead to grain growth, which negatively impacts strength. Higher temperatures, in particular, can cause significant drops in flexural strength.
-
Crystalline Structure Transformation:
- During sintering, zirconia undergoes a phase transformation from a monoclinic to a polytetragonal crystalline structure at temperatures between 1100℃ and 1200℃.
- This transformation results in a material that is extremely hard and dense, contributing to improved flexural strength and translucency.
-
Impact of Porosity and Density:
- Reduced porosity and increased density are direct results of the sintering process.
- Lower porosity means fewer internal defects, which enhances the material's ability to withstand bending forces, thereby improving flexural strength.
-
Practical Implications for Zirconia Restorations:
- Strength and Durability: Proper sintering conditions ensure that zirconia restorations are strong and durable, capable of withstanding the mechanical stresses encountered in dental applications.
- Translucency: While the primary focus is on strength, sintering also affects the translucency of zirconia, making it suitable for aesthetic dental restorations.
-
Summary of Key Findings:
- Sintering at the optimal temperature of 1500℃ is crucial for achieving the highest flexural strength in translucent monolithic zirconia.
- Deviations from this temperature can lead to reduced strength due to grain growth.
- The sintering process transforms the crystalline structure of zirconia, enhancing both its mechanical properties and translucency.
By carefully controlling the sintering process, manufacturers can produce zirconia restorations with superior flexural strength and aesthetic qualities, meeting the demands of modern dental applications.
Summary Table:
Key Factor | Impact on Flexural Strength |
---|---|
Optimal Sintering Temperature | 1500℃ maximizes strength by balancing porosity reduction and preventing grain growth. |
Temperature Deviations | Deviations by ±150℃ lead to grain growth, reducing strength. |
Crystalline Transformation | Monoclinic to polytetragonal transformation enhances strength and translucency. |
Porosity and Density | Reduced porosity and increased density improve material durability and strength. |
Practical Implications | Ensures strong, durable, and aesthetically pleasing zirconia restorations for dental use. |
Discover how precise sintering can enhance your zirconia restorations—contact our experts today!