Sintering is a critical process in powder metallurgy that transforms compacted metal powders into durable, high-performance components. By heating the material below its melting point in a controlled atmosphere, sintering bonds metal particles, reduces porosity, and enhances mechanical properties such as strength, hardness, and precision. This process enables the production of complex shapes and intricate geometries, making it invaluable in industries like automotive and tool manufacturing. Sintering also improves material microstructure, influencing grain size, pore distribution, and overall durability, while offering cost-effective and scalable production solutions.
Key Points Explained:
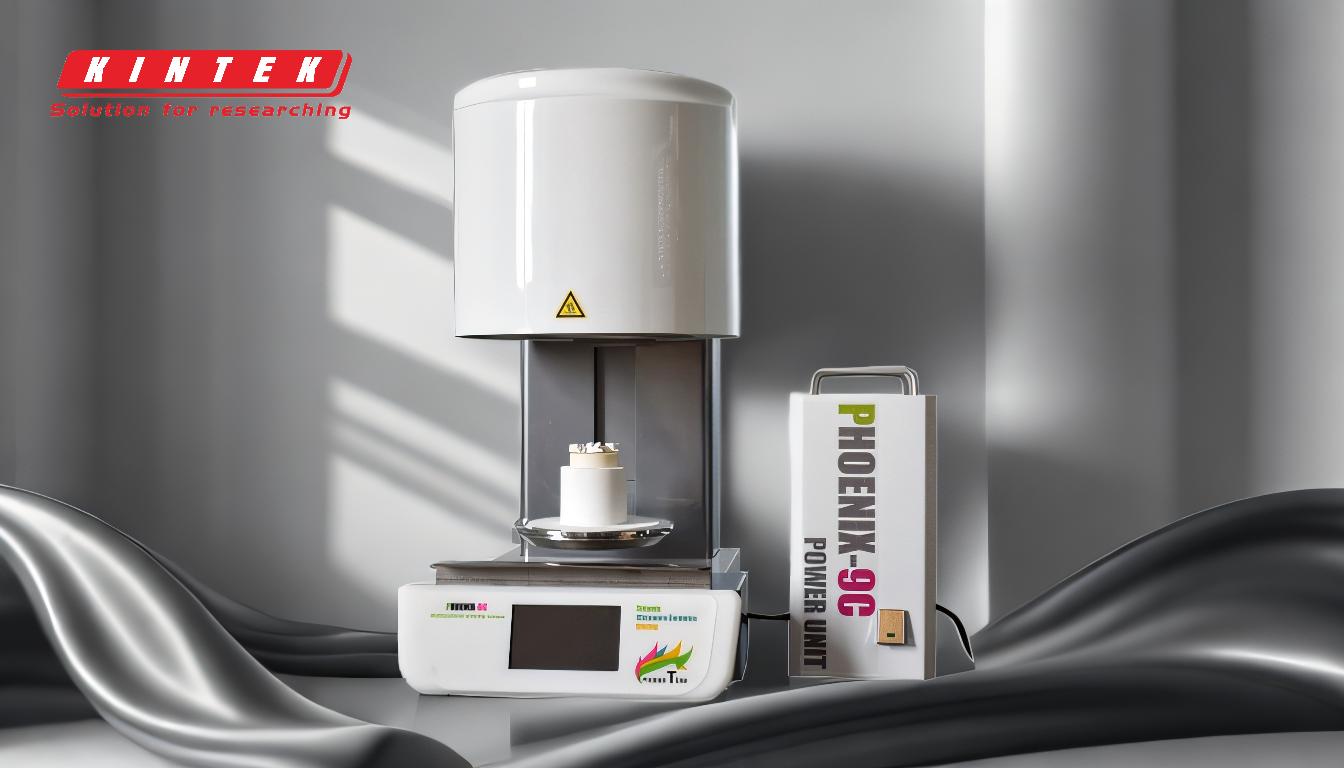
-
Definition and Purpose of Sintering:
- Sintering is a heat treatment process applied to compacted metal powders to enhance their strength, structural integrity, and final properties.
- It occurs at temperatures below the melting point of the primary material, ensuring the part retains its shape while achieving densification and bonding of particles.
-
Mechanical and Physical Property Enhancements:
- Strength and Hardness: Sintering bonds metal particles, reducing porosity and increasing material density, which improves tensile strength and hardness.
- Precision and Repeatability: The process allows for the production of intricate shapes and tight tolerances, making it ideal for components like gears, camshafts, and cutting tools.
- Toughness and Durability: By merging the properties of different materials, sintering combines toughness with abrasion resistance, enhancing the durability of the final product.
-
Microstructural Changes:
- Grain Size and Distribution: Sintering influences the grain size and grain boundary shape, which directly affect the material's mechanical properties.
- Pore Size and Distribution: The process reduces porosity, leading to a more uniform microstructure and improved material performance.
- Densification: Through diffusion and mass transfer, sintering achieves densification, resulting in a stable and homogeneous structure.
-
Applications in Industry:
- Automotive Industry: Sintering is widely used to produce components like gears, valve seats, and camshafts, which require high precision and durability.
- Cutting Tools and Filters: The process is essential for manufacturing cutting tools and sintered filters, where hardness and intricate geometries are critical.
- Advanced Ceramics: Sintering transforms ceramic powders into polycrystalline materials with specific properties, making it vital for advanced ceramic applications.
-
Economic and Production Advantages:
- Cost-Effective Tooling: Sintering allows for the production of complex parts with lower tooling costs compared to traditional manufacturing methods.
- Scalability and Mass Production: The process supports rapid mass production while maintaining precision and repeatability, making it highly efficient for large-scale manufacturing.
-
Process Parameters and Control:
- Temperature and Atmosphere: Sintering is conducted at carefully controlled temperatures and in specific atmospheres to ensure proper bonding and avoid oxidation or contamination.
- Material Compatibility: The process is tailored to the specific properties of the metal powders used, ensuring optimal results for each application.
-
Impact on Material Properties:
- Enhanced Mechanical Properties: Sintering improves properties like hardness, wear resistance, and fatigue strength, making the material suitable for demanding applications.
- Uniform Microstructure: The process results in a consistent and stable microstructure, which is crucial for achieving reliable performance in end-use parts.
By understanding the effects of sintering, manufacturers can leverage this process to produce high-quality, cost-effective components with tailored properties for a wide range of applications.
Summary Table:
Aspect | Key Details |
---|---|
Definition | Heat treatment process for compacted metal powders below melting point. |
Key Benefits | Enhanced strength, hardness, precision, and durability. |
Applications | Automotive parts, cutting tools, filters, advanced ceramics. |
Economic Advantages | Cost-effective tooling, scalability, and mass production. |
Microstructural Impact | Improved grain size, pore distribution, and uniform microstructure. |
Ready to enhance your manufacturing process? Contact us today to learn more about sintering solutions!