The evaporation method of deposition is a widely used technique in thin-film fabrication, particularly in physical vapor deposition (PVD). It involves heating a source material in a high-vacuum environment until it evaporates or sublimes, forming a vapor that travels through the vacuum and condenses onto a substrate, forming a thin, uniform film. This method is favored for its ability to produce high-purity coatings with precise control over thickness and composition. The process relies on thermal energy, often provided by resistive heating or electron beams, to vaporize the material. The vacuum environment minimizes contamination and ensures the vapor travels unimpeded to the substrate, where it adheres and solidifies. This technique is used in applications ranging from microfabrication to large-scale industrial coatings.
Key Points Explained:
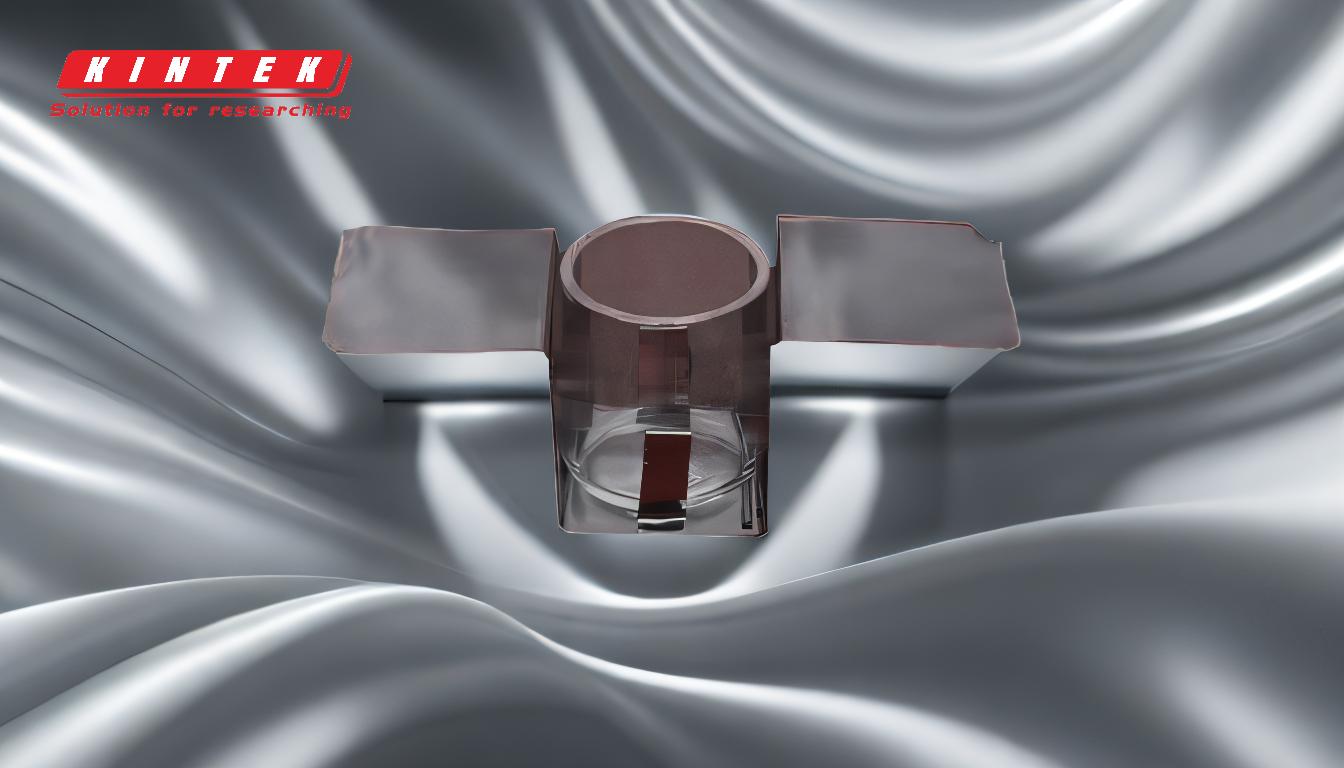
-
Basic Principle of Evaporation Deposition:
- The evaporation method involves heating a source material until it transitions into a vapor phase.
- The vaporized material travels through a vacuum and condenses onto a substrate, forming a thin film.
- This process relies on two key components: evaporation (phase change) and a heat source (thermal energy).
-
Role of Vacuum Environment:
- The process occurs in a high-vacuum chamber to minimize gas collisions and contamination.
- The vacuum ensures that vapor particles travel directly to the substrate without scattering or reacting with other atoms.
- This results in a uniform, high-purity coating.
-
Heat Sources for Evaporation:
- Resistive Heating: A tungsten filament or crucible is heated electrically to vaporize the source material.
- Electron Beam (E-Beam) Heating: A focused electron beam is used to melt and evaporate the material, ideal for high-melting-point materials.
- Both methods provide precise control over the evaporation rate and temperature.
-
Material Vaporization and Deposition:
- The source material is heated to its melting or sublimation point, transforming it into a vapor.
- The vapor forms a cloud in the vacuum chamber and travels to the substrate.
- Upon contact with the substrate, the vapor condenses and solidifies, forming a thin film.
-
Line-of-Sight Deposition:
- The process is directional, meaning only surfaces within the line of sight of the vapor source are coated.
- This limits the ability to coat complex geometries but ensures precise and uniform coatings on flat or simple surfaces.
-
Applications of Evaporation Deposition:
- Microfabrication: Used in semiconductor manufacturing to deposit thin films of metals, dielectrics, and other materials.
- Macro-Scale Products: Applied in the production of metallized plastic films, optical coatings, and reflective surfaces.
- Research and Development: Utilized in laboratories for creating high-purity thin films for experimental purposes.
-
Advantages of Evaporation Deposition:
- High-purity coatings due to the vacuum environment.
- Precise control over film thickness and composition.
- Suitable for a wide range of materials, including metals, alloys, and some ceramics.
-
Challenges and Limitations:
- Limited ability to coat complex or non-line-of-sight surfaces.
- High-energy requirements for vaporizing certain materials.
- Potential for uneven deposition if the substrate is not properly positioned or rotated.
-
Comparison to Other Deposition Methods:
- Unlike sputtering, which uses ion bombardment to eject material, evaporation relies solely on thermal energy.
- Evaporation is typically faster and more energy-efficient for materials with low melting points.
- However, sputtering may be preferred for materials with high melting points or for achieving better adhesion on certain substrates.
-
Process Control and Optimization:
- Parameters such as temperature, vacuum pressure, and deposition rate must be carefully controlled.
- Substrate preparation, including cleaning and preheating, is critical for achieving high-quality coatings.
- Monitoring tools, such as thickness sensors and rate monitors, are often used to ensure consistency.
The evaporation method of deposition is a versatile and effective technique for creating thin films with high purity and uniformity. Its reliance on thermal energy and vacuum conditions makes it suitable for a wide range of applications, from advanced electronics to industrial coatings. While it has limitations, such as its directional nature, its advantages in precision and material compatibility make it a cornerstone of modern thin-film fabrication.
Summary Table:
Aspect | Details |
---|---|
Basic Principle | Heating a material to vaporize it, forming a thin film on a substrate. |
Vacuum Environment | Minimizes contamination, ensures uniform and high-purity coatings. |
Heat Sources | Resistive heating or electron beam (E-Beam) for precise vaporization. |
Applications | Microfabrication, industrial coatings, optical films, and research. |
Advantages | High purity, precise thickness control, and material versatility. |
Limitations | Directional deposition, high energy for some materials, and complex geometries. |
Discover how the evaporation method can enhance your thin-film fabrication—contact our experts today!