The evaporation method in Physical Vapour Deposition (PVD) is a process where a source material is heated to high temperatures, causing it to melt, evaporate, or sublimate into a vapor. This vapor then condenses onto a substrate, forming a thin film. The process is conducted in a high-vacuum environment to minimize gas collisions, reduce unwanted reactions, and ensure a free path for the vaporized atoms or molecules. The substrate temperature is crucial for uniform film formation and strong adhesion. This method is widely used in applications such as mirror production and plasma spraying, where thick films are formed on substrates.
Key Points Explained:
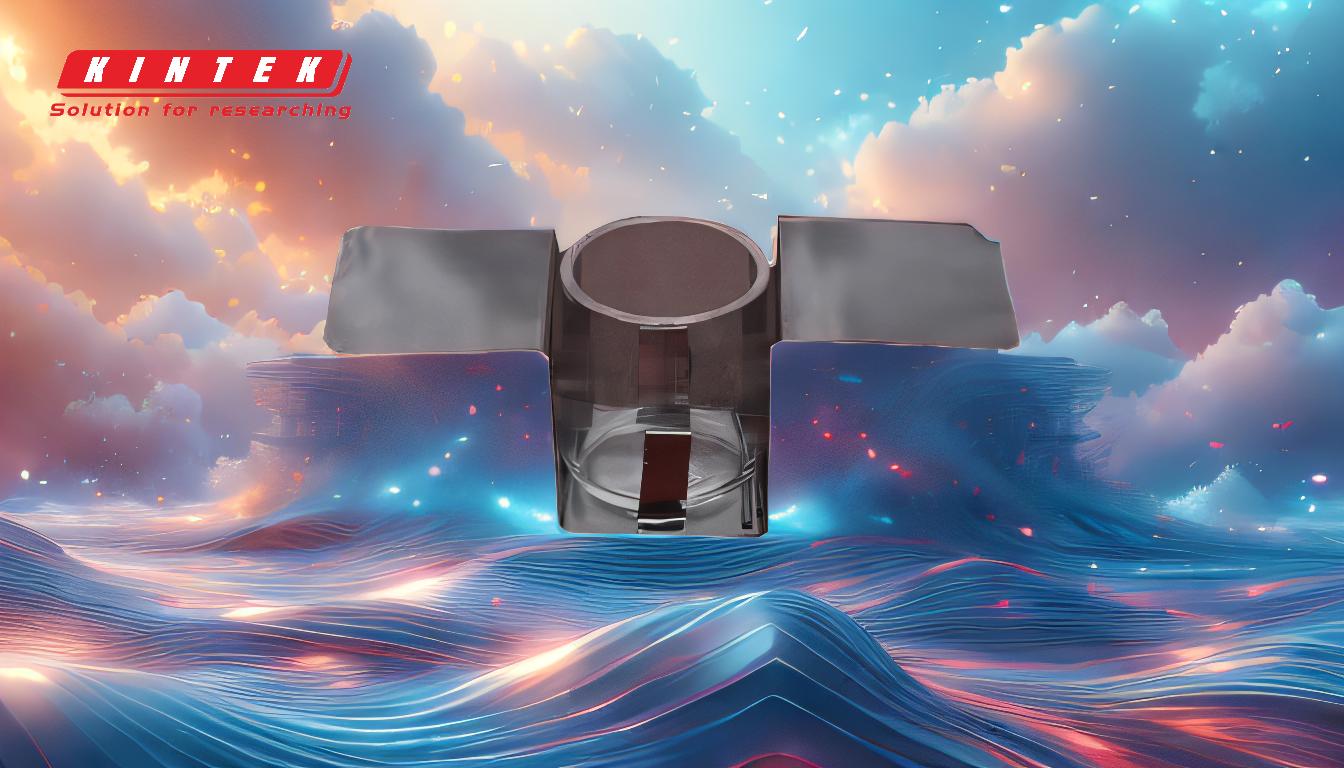
-
Heating the Source Material:
- The source material is heated to high temperatures, causing it to melt and then evaporate or sublimate into a vapor.
- This step is crucial as it converts the solid material into a gaseous state, allowing it to be transported to the substrate.
-
High-Vacuum Environment:
- The process is conducted in a high-vacuum chamber to minimize gas collisions and reduce unwanted reactions.
- A vacuum pump maintains the high-vacuum environment, ensuring a free path for the vaporized atoms or molecules.
-
Transport of Vaporized Atoms:
- The vaporized atoms or molecules are transported to the substrate with minimal collision interference from other gas atoms or molecules.
- This ensures that the vapor stream crosses the chamber efficiently and coats the substrate uniformly.
-
Condensation on Substrate:
- The vapor condenses onto the substrate, forming a thin film of the source material.
- The substrate temperature is critical for uniform film formation and strong adhesion.
-
Applications of Evaporation PVD:
- This method is widely used in applications such as mirror production, where silver is evaporated and coated on glass sheets.
- A special form of evaporation PVD is plasma spraying, where a hot plasma flame is used to melt or evaporate coating material into thick films on the substrate.
-
Thermal Evaporation Deposition:
- Thermal evaporation deposition occurs in a chamber under low pressure.
- The target material is heated, releasing vapor particles that create vapor pressure.
- The vapor stream crosses the chamber, and coating particles attach to the substrate.
-
Resistive Heat Source:
- Thermal energy from a resistive heat source is applied to a solid-state material within a vacuum chamber.
- This causes the material to evaporate, and the resulting vapor condenses on a substrate, forming a thin film of the source material.
-
Diffusion Through Vacuum:
- In the evaporation method of PVD, material is heated to a gas phase, where it then diffuses through a vacuum to the substrate.
- This diffusion process ensures that the vaporized atoms or molecules reach the substrate efficiently and form a uniform coating.
By understanding these key points, one can appreciate the complexity and precision required in the evaporation method of PVD, making it a valuable technique in various industrial applications.
Summary Table:
Key Steps | Description |
---|---|
Heating Source Material | Material is heated to high temperatures, converting it into a vapor phase. |
High-Vacuum Environment | Conducted in a vacuum to minimize gas collisions and ensure efficient transport. |
Transport of Vapor | Vaporized atoms travel to the substrate with minimal interference. |
Condensation on Substrate | Vapor condenses to form a uniform thin film with strong adhesion. |
Applications | Used in mirror production, plasma spraying, and other industrial processes. |
Discover how the evaporation method in PVD can enhance your industrial processes—contact us today for expert guidance!