The evaporation process of semiconductors, specifically through thermal evaporation deposition, involves heating a target material in a low-pressure chamber to release vapor particles. These particles form a vapor stream that travels across the chamber and deposits onto a substrate, creating a thin film. A vacuum pump maintains a high-vacuum environment to ensure the vapor particles have a free path to the substrate. This process is critical for creating precise semiconductor layers used in various electronic and optoelectronic devices.
Key Points Explained:
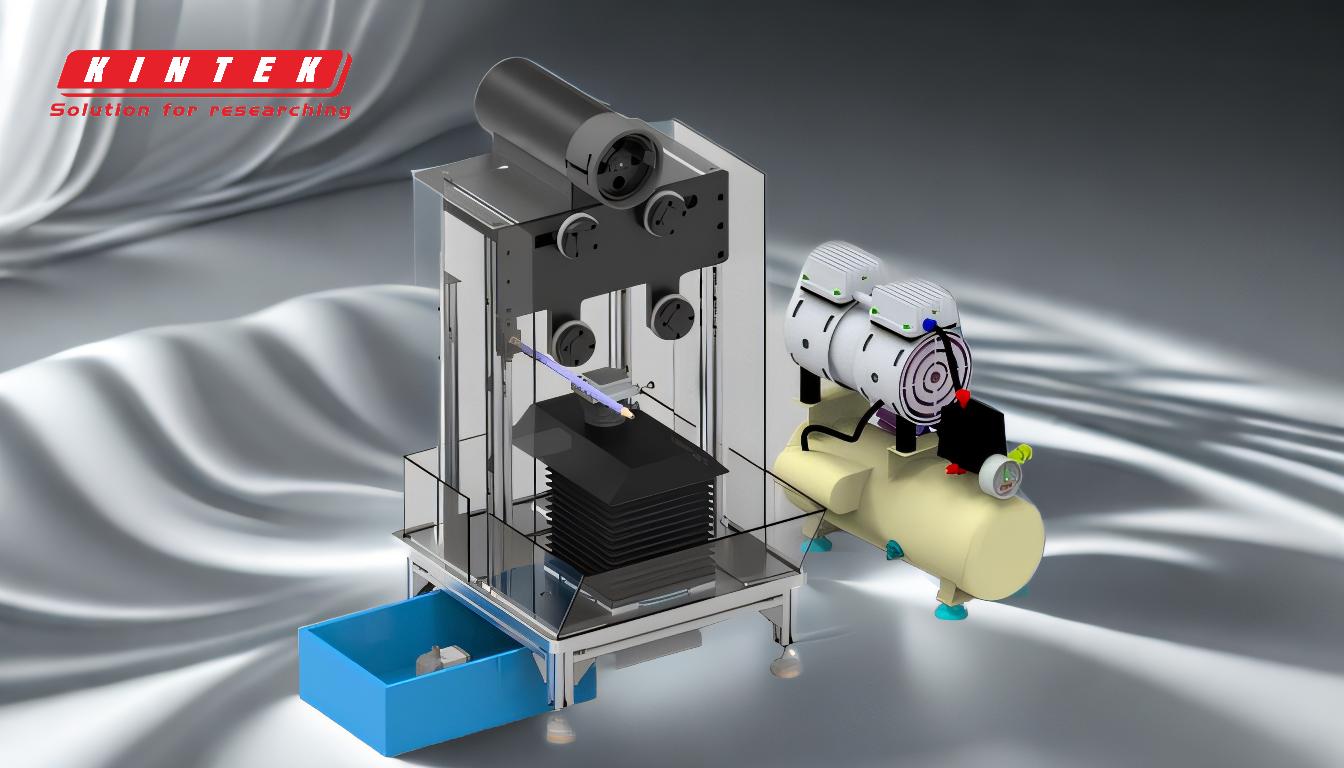
-
Thermal Evaporation Deposition Overview:
- Thermal evaporation deposition is a physical vapor deposition (PVD) technique used to create thin films of semiconductors.
- The process involves heating a target material (e.g., a semiconductor) in a vacuum chamber until it vaporizes.
- The vaporized particles then travel through the chamber and deposit onto a substrate, forming a thin, uniform layer.
-
Role of Low Pressure and Vacuum Environment:
- The process occurs in a vacuum chamber to minimize the presence of other gases or contaminants.
- A vacuum pump maintains a high-vacuum environment, typically in the range of 10^-6 to 10^-8 Torr.
- This ensures that the vapor particles travel unimpeded to the substrate, resulting in a high-quality, defect-free film.
-
Heating the Target Material:
- The target material is heated using a resistive heating source, electron beam, or laser.
- The heating process must be carefully controlled to achieve the desired vapor pressure and deposition rate.
- For semiconductors, the heating temperature is typically below the melting point to avoid damaging the material's properties.
-
Formation of Vapor Stream:
- As the target material heats up, it releases vapor particles into the chamber.
- These particles form a vapor stream that travels in a straight line toward the substrate.
- The vapor stream's directionality ensures uniform deposition across the substrate.
-
Deposition onto the Substrate:
- The vapor particles attach to the substrate's surface, forming a thin film.
- The substrate is often rotated or moved to achieve even coating thickness.
- The deposited film's properties, such as thickness and uniformity, depend on factors like deposition rate, substrate temperature, and chamber pressure.
-
Applications in Semiconductor Manufacturing:
- Thermal evaporation is widely used to deposit semiconductor materials like silicon, germanium, and compound semiconductors (e.g., GaAs, InP).
- The process is essential for creating layers in devices such as solar cells, LEDs, and integrated circuits.
- It is particularly valued for its ability to produce high-purity films with precise control over thickness.
-
Advantages of Thermal Evaporation:
- High deposition rates and efficiency.
- Ability to deposit a wide range of materials, including metals, semiconductors, and insulators.
- Minimal contamination due to the high-vacuum environment.
-
Challenges and Considerations:
- The process requires precise control over temperature, pressure, and deposition rate.
- Some materials may decompose or react during heating, requiring alternative deposition methods.
- The equipment can be expensive and complex, particularly for large-scale production.
By understanding these key points, equipment and consumable purchasers can make informed decisions about the tools and materials needed for semiconductor evaporation processes. This knowledge also helps in optimizing the process for specific applications and ensuring the quality of the final product.
Summary Table:
Key Aspect | Details |
---|---|
Process Overview | Physical vapor deposition (PVD) technique for creating thin semiconductor films. |
Vacuum Environment | Maintained at 10^-6 to 10^-8 Torr for minimal contamination and free vapor flow. |
Heating Methods | Resistive heating, electron beam, or laser for controlled vaporization. |
Vapor Stream Formation | Vapor particles travel in a straight line, ensuring uniform deposition. |
Substrate Deposition | Thin film forms as particles attach to the substrate; rotation ensures even coating. |
Applications | Solar cells, LEDs, integrated circuits, and other semiconductor devices. |
Advantages | High deposition rates, wide material compatibility, minimal contamination. |
Challenges | Requires precise control; some materials may decompose; equipment can be costly. |
Optimize your semiconductor manufacturing process with thermal evaporation deposition—contact our experts today for tailored solutions!