The evaporation theory of thin films revolves around the process of heating a source material until it evaporates in a vacuum environment, allowing the vaporized particles to travel unimpeded and condense onto a substrate, forming a thin film. This method is widely used in microfabrication and industrial applications due to its ability to produce uniform and high-quality coatings. The process relies on thermal energy, typically generated by heating elements or electron beams, to vaporize the material. The vacuum ensures that the vaporized particles travel directly to the substrate without interference, enabling precise control over film composition and thickness. This technique is essential for creating functional coatings in electronics, optics, and packaging industries.
Key Points Explained:
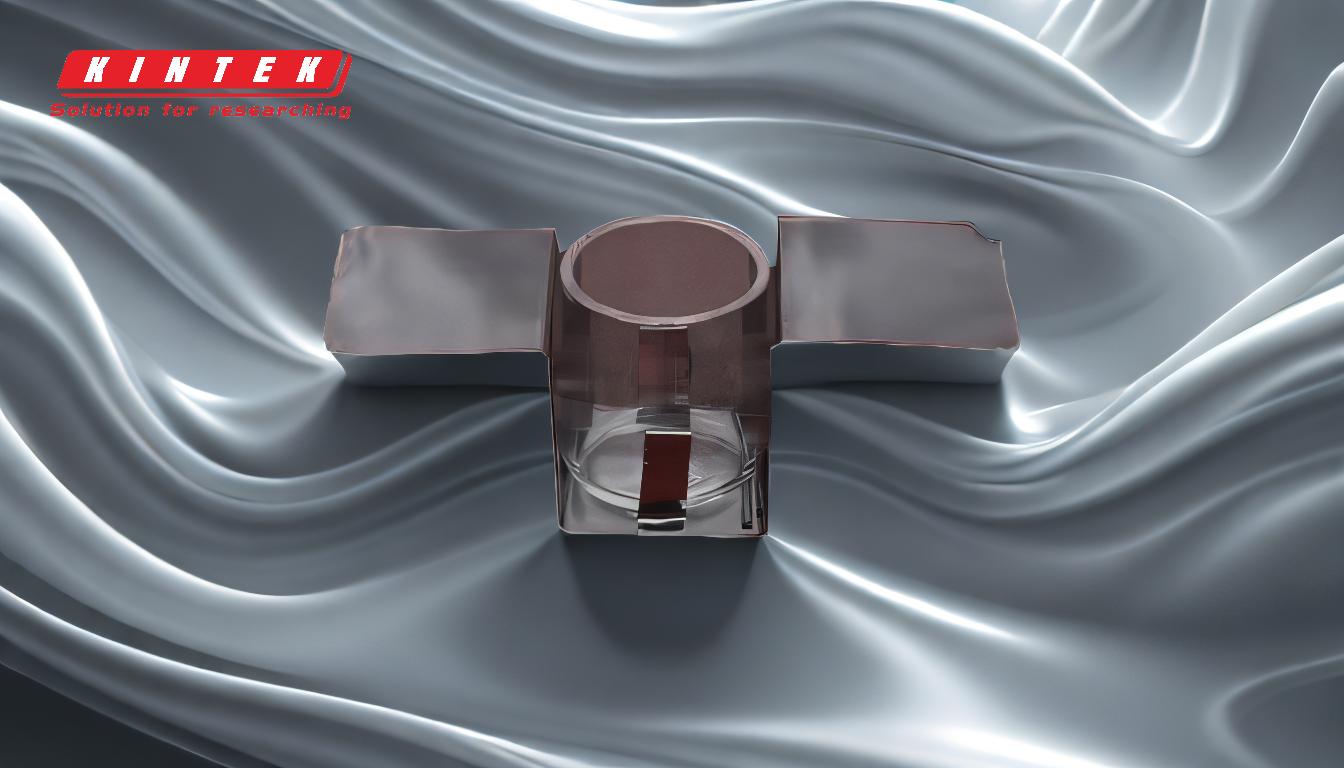
-
Evaporation Process in Thin-Film Deposition:
- The core of the evaporation theory lies in transforming a solid source material into a vapor phase and then condensing it onto a substrate to form a thin film.
- This process occurs in a vacuum to prevent contamination and ensure that vaporized particles travel directly to the substrate without reacting with air or other gases.
- The analogy of steam condensing on a ceiling illustrates how the vaporized material transitions back to a solid state upon contact with the cooler substrate.
-
Heat Sources for Evaporation:
- Thermal energy is required to vaporize the source material, and this is typically achieved using:
- Heating Elements: Tungsten wires or crucibles are commonly used to heat the material to its evaporation point.
- Electron Beam Evaporation: A focused electron beam provides high-energy input, allowing the evaporation of materials with very high melting points.
- The choice of heat source depends on the material's properties, such as its melting point and thermal stability.
- Thermal energy is required to vaporize the source material, and this is typically achieved using:
-
Vacuum Environment:
- The vacuum is critical for maintaining the purity and integrity of the deposition process.
- It ensures that vaporized particles travel in a straight line to the substrate, minimizing collisions with gas molecules that could alter the film's properties.
- The vacuum also prevents oxidation or other chemical reactions that could degrade the film quality.
-
Condensation and Film Formation:
- Once the vaporized material reaches the substrate, it condenses and forms a solid film through nucleation and growth.
- The film's properties, such as thickness, uniformity, and adhesion, depend on factors like substrate temperature, deposition rate, and the material's inherent properties.
- This step is analogous to water vapor condensing into droplets on a cold surface.
-
Applications of Evaporation-Based Thin Films:
- Microfabrication: Used in the production of semiconductors, optical coatings, and sensors.
- Macro-Scale Products: Applied in the creation of metallized plastic films for packaging and decorative purposes.
- The versatility of the evaporation method allows for the deposition of a wide range of materials, including metals, alloys, and compounds.
-
Advantages of Evaporation Techniques:
- Material Flexibility: Suitable for depositing a variety of materials, including those with high melting points.
- Precision and Control: Enables precise control over film thickness and composition, making it ideal for high-performance applications.
- Scalability: Can be adapted for both small-scale laboratory setups and large-scale industrial production.
-
Challenges and Considerations:
- Material Limitations: Some materials may decompose or react under high temperatures, limiting their suitability for evaporation.
- Uniformity and Adhesion: Achieving uniform film thickness and strong adhesion to the substrate requires careful control of process parameters.
- Cost and Complexity: The need for vacuum equipment and specialized heat sources can increase the cost and complexity of the process.
By understanding these key points, one can appreciate the fundamental principles and practical considerations of the evaporation theory of thin films, making it a cornerstone of modern material science and engineering.
Summary Table:
Aspect | Details |
---|---|
Evaporation Process | Transforms solid material into vapor, condensing onto a substrate in a vacuum. |
Heat Sources | Heating elements (e.g., tungsten) or electron beams for high-melting materials. |
Vacuum Environment | Ensures purity, prevents contamination, and enables direct particle travel. |
Condensation | Vapor condenses into a solid film, controlled by substrate temperature. |
Applications | Semiconductors, optical coatings, sensors, and packaging materials. |
Advantages | Material flexibility, precision control, and scalability. |
Challenges | Material limitations, uniformity, adhesion, and cost considerations. |
Discover how evaporation-based thin films can enhance your applications—contact our experts today!