Ethylene crackers, also known as steam crackers, are industrial facilities that produce ethylene and other olefins by breaking down hydrocarbons through a process called pyrolysis. The feedstock for ethylene crackers typically includes light hydrocarbons such as ethane, propane, butane, and naphtha, which are derived from natural gas or crude oil refining. Ethane is the most common feedstock due to its high ethylene yield and cost-effectiveness, especially in regions with abundant natural gas resources. Other feedstocks like propane, butane, and naphtha are used depending on availability, cost, and desired product mix. The choice of feedstock significantly impacts the process efficiency, product distribution, and overall economics of the ethylene production process.
Key Points Explained:
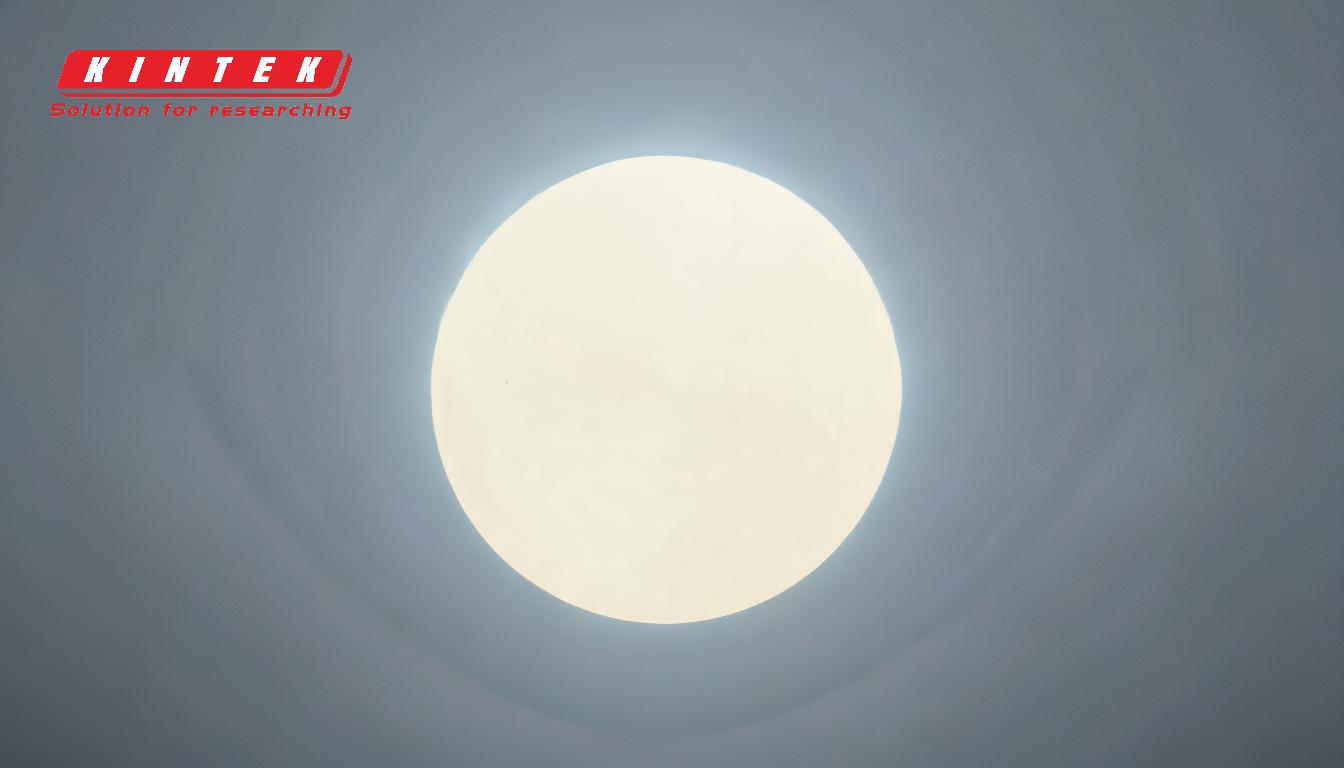
-
Primary Feedstocks for Ethylene Crackers:
- Ethane: Derived from natural gas processing, ethane is the most widely used feedstock for ethylene production. It offers a high ethylene yield (up to 80%) and is cost-effective in regions with abundant natural gas, such as the Middle East and North America.
- Propane: Often used as a feedstock in regions where ethane is less available. Propane cracking produces a mix of ethylene and propylene, making it suitable for dual-purpose production.
- Butane: Less commonly used due to lower ethylene yields compared to ethane and propane. However, it can be a viable option in specific scenarios.
- Naphtha: A liquid feedstock derived from crude oil refining. Naphtha cracking produces a broader range of products, including ethylene, propylene, and heavier olefins. It is commonly used in regions with limited natural gas resources, such as Europe and Asia.
-
Factors Influencing Feedstock Selection:
- Availability: The choice of feedstock depends on the availability of raw materials in a specific region. For example, ethane is preferred in regions with abundant natural gas, while naphtha is more common in areas reliant on crude oil.
- Cost: Feedstock cost is a critical factor in determining the economics of ethylene production. Ethane is often the cheapest option in gas-rich regions, while naphtha is more expensive but provides a wider product slate.
- Product Mix: Different feedstocks yield varying proportions of ethylene, propylene, and other byproducts. For example, naphtha cracking produces more propylene and heavier olefins compared to ethane cracking.
- Process Efficiency: Ethane cracking is more efficient in terms of ethylene yield, while naphtha cracking requires more energy and produces a more complex product mix.
-
Regional Variations in Feedstock Usage:
- North America: Dominated by ethane cracking due to the shale gas revolution, which has made ethane abundantly available and cost-effective.
- Middle East: Ethane is the primary feedstock, supported by large natural gas reserves and low production costs.
- Europe and Asia: Naphtha is the predominant feedstock due to limited natural gas resources and reliance on crude oil refining.
-
Impact of Feedstock on Ethylene Production:
- Ethylene Yield: Ethane cracking provides the highest ethylene yield, making it the most efficient feedstock for ethylene production.
- Byproducts: Naphtha cracking produces a wider range of byproducts, including propylene, butadiene, and aromatics, which can be valuable for downstream petrochemical processes.
- Energy Consumption: Ethane cracking requires less energy compared to naphtha cracking, making it more environmentally friendly and cost-efficient.
-
Future Trends in Feedstock Usage:
- Shift Towards Lighter Feedstocks: With the increasing availability of natural gas and the development of shale gas resources, there is a growing trend towards lighter feedstocks like ethane and propane.
- Integration with Refineries: Some ethylene crackers are integrated with refineries to utilize mixed feedstocks, optimizing the use of available resources and improving overall process efficiency.
- Sustainability Considerations: There is a growing focus on using renewable feedstocks and reducing the carbon footprint of ethylene production, which may influence future feedstock choices.
Summary Table:
Feedstock | Source | Ethylene Yield | Key Characteristics |
---|---|---|---|
Ethane | Natural Gas | Up to 80% | High yield, cost-effective, preferred in gas-rich regions (e.g., North America, Middle East). |
Propane | Natural Gas | Moderate | Produces ethylene and propylene; used where ethane is less available. |
Butane | Natural Gas | Low | Less common; viable in specific scenarios. |
Naphtha | Crude Oil Refining | Variable | Produces a broader range of products; common in regions with limited natural gas. |
Need expert advice on selecting the right feedstock for your ethylene production? Contact us today to optimize your process!