Slow pyrolysis is a thermochemical process used to convert biomass into biochar, bio-oil, and syngas. The feedstock for slow pyrolysis primarily includes various types of biomass, such as wood, agricultural residues, forestry waste, municipal solid waste, and even algae. These materials are chosen based on their availability, composition, and cost-effectiveness. Wood, particularly from forest trees and branches, remains the most commonly used feedstock due to its widespread availability and consistent quality. Agricultural residues like sugarcane bagasse, rice straw, and wheat straw are also popular choices, especially in regions where these crops are abundant. Additionally, waste materials such as municipal solid waste and sewage can be utilized, making slow pyrolysis an environmentally friendly method for waste management. The choice of feedstock significantly impacts the quality and yield of the end products, making it crucial to select appropriate materials for specific applications.
Key Points Explained:
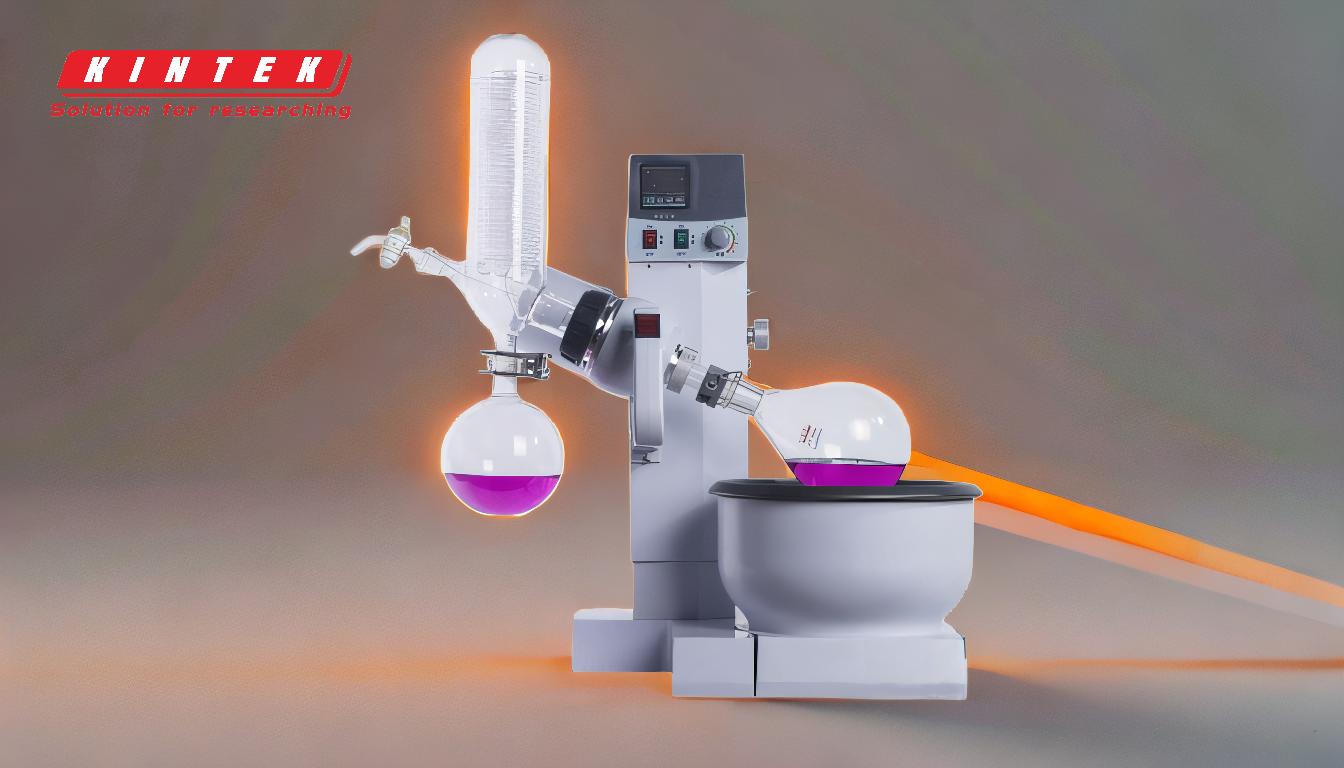
-
Types of Biomass Used in Slow Pyrolysis:
- Wood: Forest trees, branches, and wood processing residues are the most common feedstocks. Pine wood is particularly noted for its use in biochar production.
- Agricultural Residues: Materials like sugarcane bagasse, rice straw, cotton stalks, and wheat straw are widely used, especially in agricultural regions.
- Forestry Waste: This includes wood processing residues, branches, and bark, which are often by-products of the timber industry.
- Municipal Solid Waste: Organic domestic waste and municipal sludge can be processed, providing a sustainable waste management solution.
- Algae and Invasive Species: Dried algae and invasive species like phragmites and kudzu are also suitable feedstocks, offering an alternative to traditional biomass sources.
-
Factors Influencing Feedstock Selection:
- Availability: The feedstock must be readily available in sufficient quantities to ensure continuous operation of the pyrolysis plant.
- Composition: The chemical composition of the biomass affects the quality and yield of the pyrolysis products. High lignin content, for example, is desirable for biochar production.
- Cost: The cost of the feedstock is a critical factor, especially for large-scale operations. Waste materials and agricultural residues are often cost-effective options.
-
Environmental and Economic Benefits:
- Waste Management: Using municipal solid waste and sewage as feedstock helps in reducing landfill use and managing waste more sustainably.
- Renewable Energy: Slow pyrolysis converts biomass into biochar, bio-oil, and syngas, which can be used as renewable energy sources.
- Soil Improvement: Biochar produced from slow pyrolysis can be used as a soil amendment, improving soil fertility and carbon sequestration.
-
Applications of Pyrolysis Products:
- Biochar: Used in agriculture for soil improvement, carbon sequestration, and as a filtration medium.
- Bio-oil: Can be refined into biofuels or used directly in heating applications.
- Syngas: Used for electricity generation or as a chemical feedstock.
In conclusion, the feedstock for slow pyrolysis encompasses a wide range of biomass materials, each selected based on specific criteria such as availability, composition, and cost. The choice of feedstock not only influences the efficiency and output of the pyrolysis process but also contributes to environmental sustainability and economic viability.
Summary Table:
Feedstock Type | Examples | Key Benefits |
---|---|---|
Wood | Forest trees, branches, pine wood | High availability, consistent quality, ideal for biochar production |
Agricultural Residues | Sugarcane bagasse, rice straw, wheat straw | Abundant in agricultural regions, cost-effective |
Forestry Waste | Wood processing residues, bark | By-products of timber industry, sustainable use |
Municipal Solid Waste | Organic domestic waste, sewage | Reduces landfill use, eco-friendly waste management |
Algae and Invasive Species | Dried algae, phragmites, kudzu | Alternative biomass sources, environmentally sustainable |
Learn how slow pyrolysis can transform biomass into renewable energy and sustainable products—contact us today!