The firing temperature of dental ceramics is a critical parameter that determines the final properties of the ceramic restoration, such as strength, translucency, and biocompatibility. Dental ceramics are typically fired at high temperatures ranging from 850°C to 1,400°C, depending on the type of ceramic and the specific application. Fine ceramics, which are used in dental restorations, often require precise temperature control to achieve optimal results. The firing process involves multiple stages, including heating, holding at the peak temperature, and controlled cooling, to ensure the ceramic material achieves the desired microstructure and mechanical properties. Understanding the firing temperature is essential for dental technicians and clinicians to produce high-quality dental restorations.
Key Points Explained:
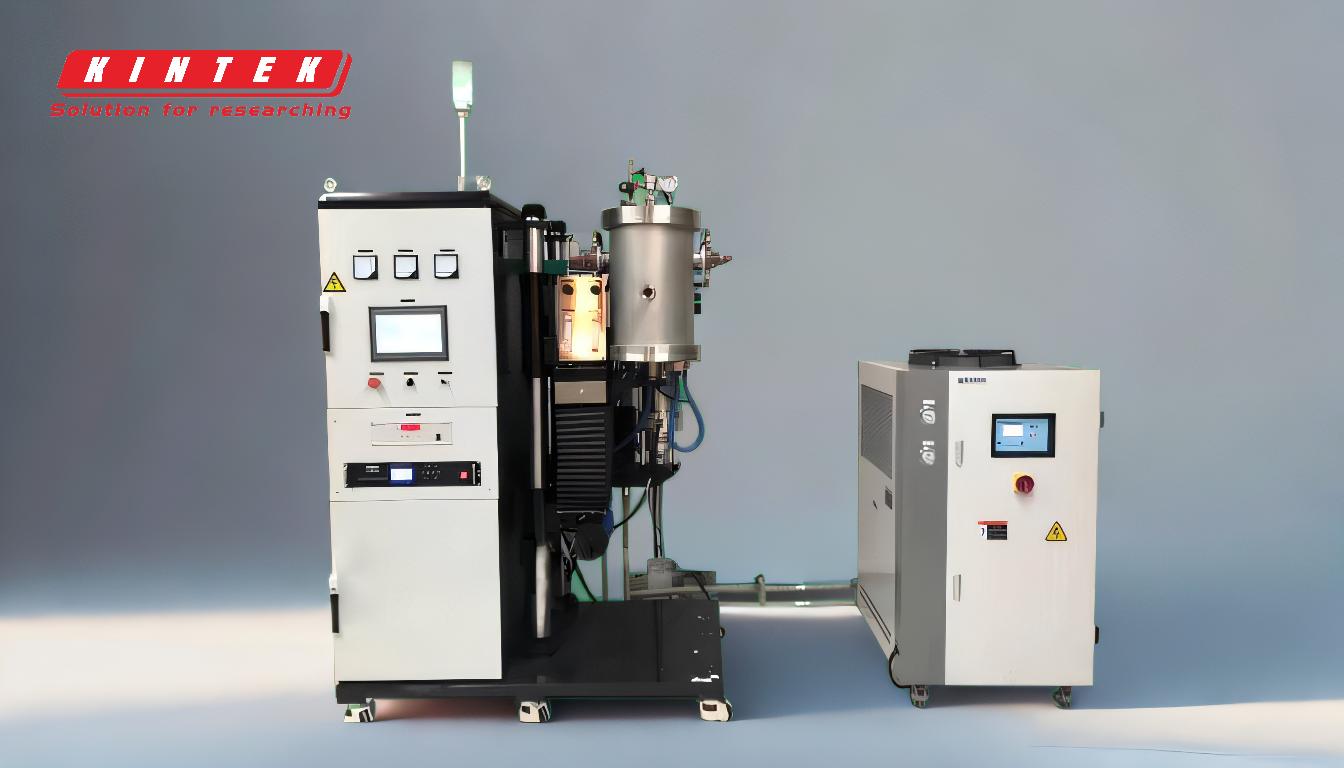
-
Types of Dental Ceramics and Their Firing Temperatures:
- Dental ceramics can be broadly categorized into porcelain, zirconia, and glass ceramics. Each type has a specific firing temperature range:
- Porcelain: Typically fired between 850°C and 1,100°C. Porcelain is commonly used for veneers and crowns due to its aesthetic properties.
- Zirconia: Fired at much higher temperatures, usually between 1,200°C and 1,400°C. Zirconia is known for its high strength and is often used for dental crowns and bridges.
- Glass Ceramics: These are fired at temperatures ranging from 850°C to 1,050°C. Glass ceramics are used for inlays, onlays, and some types of crowns.
- Dental ceramics can be broadly categorized into porcelain, zirconia, and glass ceramics. Each type has a specific firing temperature range:
-
Importance of Firing Temperature:
- The firing temperature directly affects the microstructure and mechanical properties of the dental ceramic. For example:
- Strength: Higher firing temperatures generally result in stronger ceramics due to better sintering and densification.
- Translucency: The temperature can influence the translucency of the ceramic, which is crucial for aesthetic restorations.
- Biocompatibility: Proper firing ensures that the ceramic is biocompatible and safe for use in the oral environment.
- The firing temperature directly affects the microstructure and mechanical properties of the dental ceramic. For example:
-
Firing Process and Stages:
- The firing process typically involves several stages:
- Heating: The ceramic is gradually heated to the desired temperature to prevent thermal shock.
- Holding: The ceramic is held at the peak temperature for a specific duration to allow for complete sintering.
- Cooling: Controlled cooling is essential to prevent cracking and to stabilize the microstructure of the ceramic.
- The firing process typically involves several stages:
-
Fine Ceramics in Dental Applications:
- Fine ceramics are a subset of dental ceramics that are engineered for high precision and performance. These materials often require very specific firing temperatures and conditions to achieve the desired properties. For example, fine ceramics used in dental restorations may require temperatures in the range of 1,200°C to 1,400°C to ensure optimal strength and durability. The use of fine ceramics in dental applications is growing due to their superior mechanical properties and aesthetic qualities.
-
Factors Influencing Firing Temperature:
- Several factors can influence the optimal firing temperature for dental ceramics:
- Material Composition: Different ceramic materials have different melting points and sintering temperatures.
- Desired Properties: The required strength, translucency, and biocompatibility can dictate the firing temperature.
- Furnace Type: The type of furnace used (e.g., muffle furnace, vacuum furnace) can affect the temperature uniformity and control, which in turn influences the firing process.
- Several factors can influence the optimal firing temperature for dental ceramics:
-
Practical Considerations for Dental Technicians:
- Dental technicians must carefully follow the manufacturer's guidelines for firing temperatures and schedules. Deviations from the recommended parameters can lead to suboptimal results, such as weak or discolored restorations. Additionally, the choice of furnace and the calibration of temperature controls are critical for achieving consistent results.
In summary, the firing temperature of dental ceramics is a complex and critical parameter that varies depending on the type of ceramic and the desired properties of the final restoration. Fine ceramics, in particular, require precise temperature control to achieve the high performance expected in dental applications. Understanding and controlling the firing process is essential for producing high-quality dental restorations that meet the functional and aesthetic needs of patients.
Summary Table:
Type of Ceramic | Firing Temperature Range | Common Applications |
---|---|---|
Porcelain | 850°C - 1,100°C | Veneers, Crowns |
Zirconia | 1,200°C - 1,400°C | Crowns, Bridges |
Glass Ceramics | 850°C - 1,050°C | Inlays, Onlays, Crowns |
Need precise temperature control for your dental ceramics? Contact our experts today for tailored solutions!