The deposition rate of a thin film is a critical parameter in thin film deposition processes, as it determines how quickly the film is produced. It is typically measured in units of thickness per unit of time (e.g., nanometers per second or angstroms per minute). The deposition rate depends on the specific deposition technology used, such as magnetron sputtering, chemical vapor deposition (CVD), or physical vapor deposition (PVD). For example, in magnetron sputtering, the deposition rate can be calculated using the formula: ( R_{dep} = A \times R_{sputter} ), where ( R_{dep} ) is the deposition rate, ( A ) is the deposition area, and ( R_{sputter} ) is the sputtering rate. Understanding and controlling the deposition rate is essential for achieving the desired film thickness and quality in various applications.
Key Points Explained:
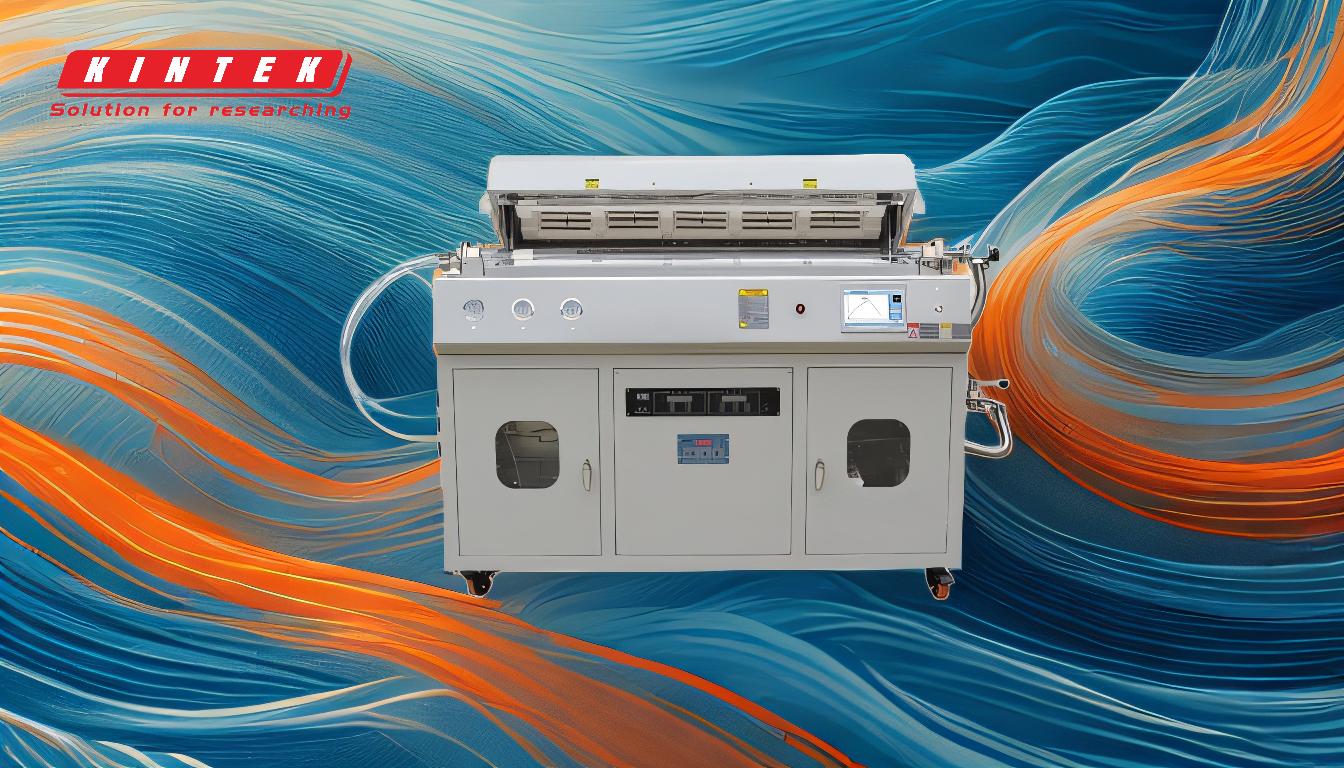
-
Definition of Deposition Rate:
- The deposition rate is a measure of how quickly a thin film is deposited onto a substrate. It is typically expressed in units of thickness (e.g., nanometers, angstroms) divided by time (e.g., seconds, minutes).
- This parameter is crucial for ensuring that the film is produced at an appropriate speed for the application, balancing the need for rapid production with the requirement for precise control over film thickness.
-
Units of Measurement:
- Deposition rate is commonly measured in units such as nanometers per second (nm/s) or angstroms per minute (Å/min). These units reflect the thickness of the film deposited over a specific time period.
- The choice of units depends on the specific application and the precision required in controlling the film thickness.
-
Deposition Rate Formula in Magnetron Sputtering:
- In magnetron sputtering, a common technique for thin film deposition, the deposition rate can be calculated using the formula:
[
R_{dep} = A \times R_{sputter}
]
where:
- ( R_{dep} ) = Deposition rate
- ( A ) = Deposition area
- ( R_{sputter} ) = Sputtering rate
- This formula indicates that the deposition rate is directly proportional to both the deposition area and the sputtering rate. The sputtering rate is influenced by factors such as the power applied to the magnetron, the type of target material, and the pressure of the sputtering gas.
- In magnetron sputtering, a common technique for thin film deposition, the deposition rate can be calculated using the formula:
[
R_{dep} = A \times R_{sputter}
]
where:
-
Factors Influencing Deposition Rate:
- Power Applied: Higher power levels in sputtering systems generally increase the sputtering rate, leading to a higher deposition rate.
- Target Material: Different materials have different sputtering yields, which affect the deposition rate. For example, metals typically have higher sputtering rates than insulators.
- Gas Pressure: The pressure of the sputtering gas (e.g., argon) can influence the deposition rate. Optimal pressure levels are necessary to achieve the desired deposition rate and film quality.
- Substrate Temperature: The temperature of the substrate can also affect the deposition rate, as higher temperatures may enhance the mobility of adatoms on the substrate surface.
-
Importance of Controlling Deposition Rate:
- Controlling the deposition rate is essential for achieving the desired film properties, such as thickness, uniformity, and adhesion.
- In industrial applications, a high deposition rate may be desirable to increase throughput, but it must be balanced with the need for precise control over film thickness and quality.
- In research and development, precise control over the deposition rate is often necessary to study the effects of film thickness on material properties.
-
Applications of Deposition Rate Control:
- Semiconductor Manufacturing: In the production of semiconductor devices, precise control over the deposition rate is critical for creating thin films with specific electrical properties.
- Optical Coatings: For optical coatings, such as anti-reflective coatings, the deposition rate must be carefully controlled to achieve the desired optical performance.
- Protective Coatings: In applications where thin films are used for protective purposes, such as corrosion-resistant coatings, the deposition rate must be optimized to ensure adequate coverage and durability.
In summary, the deposition rate is a fundamental parameter in thin film deposition processes, and its control is essential for achieving the desired film properties in various applications. The formula for calculating the deposition rate in magnetron sputtering, ( R_{dep} = A \times R_{sputter} ), provides a clear relationship between the deposition rate, deposition area, and sputtering rate. Understanding and controlling the factors that influence the deposition rate is key to optimizing thin film deposition processes.
Summary Table:
Key Aspect | Details |
---|---|
Definition | The rate at which a thin film is deposited onto a substrate. |
Units | Nanometers per second (nm/s) or angstroms per minute (Å/min). |
Formula (Magnetron Sputtering) | ( R_{dep} = A \times R_{sputter} ) |
Influencing Factors | Power applied, target material, gas pressure, and substrate temperature. |
Applications | Semiconductor manufacturing, optical coatings, and protective coatings. |
Optimize your thin film deposition process—contact our experts today for tailored solutions!