Pyrolysis oil, derived from the thermal decomposition of organic materials, holds significant promise as an alternative fuel source and feedstock for various industrial applications. Its future is shaped by its versatility, potential for upgrading, and alignment with sustainability goals. Currently, pyrolysis oil is used in stationary applications such as power generation, cement factories, and iron plants, and it can be reprocessed into diesel for broader applications. However, its future lies in advancements in refining and upgrading techniques, which will enhance its quality, economic viability, and suitability for transportation and chemical production. As industries and governments prioritize renewable energy sources, pyrolysis oil is poised to play a critical role in reducing reliance on fossil fuels and achieving decarbonization goals.
Key Points Explained:
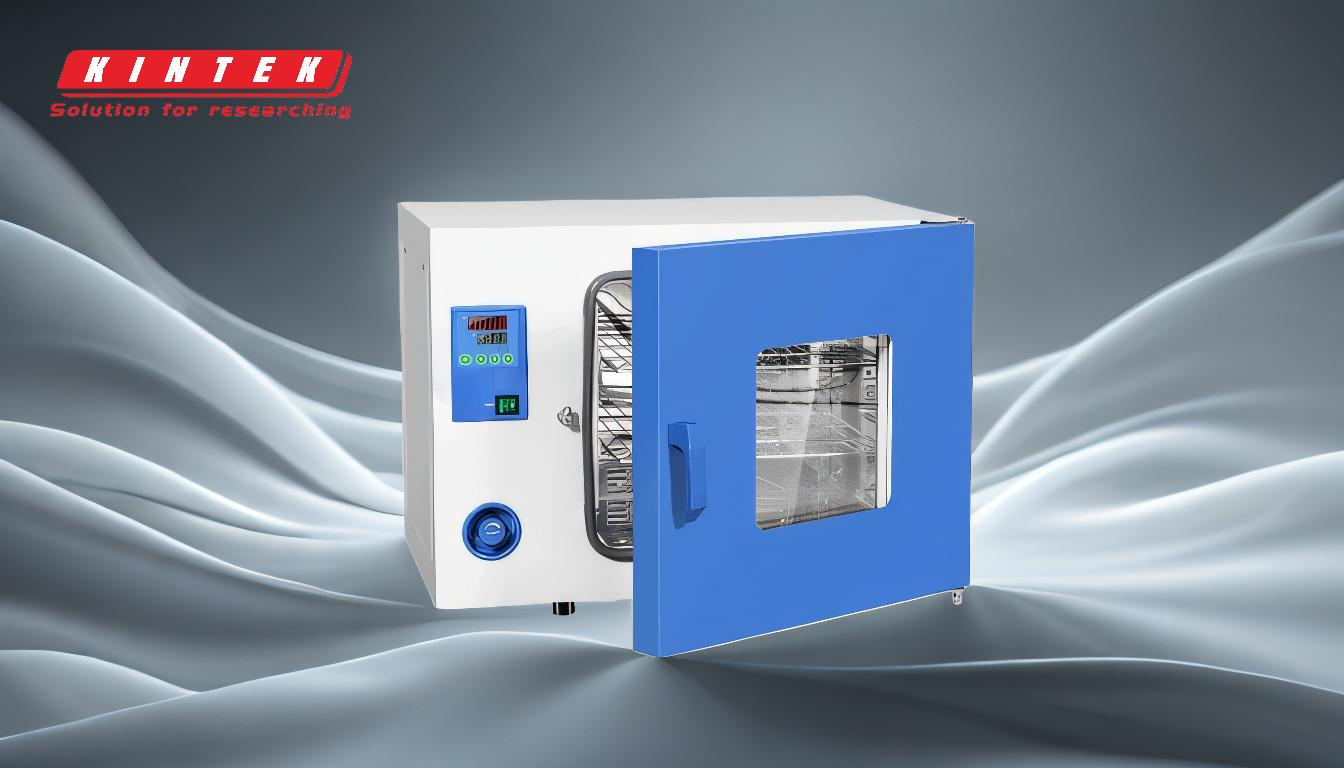
-
Current Applications of Pyrolysis Oil:
- Pyrolysis oil is already being used in several industrial sectors, including:
- Iron plants: As a substitute for conventional fuel oils.
- Power plants: For electricity generation.
- Cement and brick factories: As a cost-effective and renewable fuel source.
- These applications are regulated by standards such as ASTM D7544, ensuring its safe and efficient use in stationary settings.
- Pyrolysis oil is already being used in several industrial sectors, including:
-
Potential for Upgrading and Refining:
- Pyrolysis oil can be further treated and refined to improve its quality and expand its applications:
- Hydrocarbon fuel production: Upgraded pyrolysis oil can be integrated into existing refinery infrastructure to produce diesel and other hydrocarbon fuels.
- Chemical and material production: It can serve as a feedstock for producing chemicals and advanced materials, such as carbon nanotubes.
- These advancements will enhance its economic competitiveness and make it suitable for broader commercial uses.
- Pyrolysis oil can be further treated and refined to improve its quality and expand its applications:
-
Future Applications in Transportation:
- With continued advancements in refining techniques, pyrolysis oil has the potential to be used as an engine fuel:
- Diesel engines: Reprocessed pyrolysis oil can be used in diesel engines, offering a renewable alternative to traditional diesel.
- Transportation sector: Its use in vehicles and other transportation systems could significantly reduce greenhouse gas emissions.
- With continued advancements in refining techniques, pyrolysis oil has the potential to be used as an engine fuel:
-
Sustainability and Decarbonization:
- Pyrolysis oil aligns with global sustainability and decarbonization goals:
- Renewable energy source: It is derived from organic waste and biomass, making it a sustainable alternative to fossil fuels.
- Waste reduction: The production of pyrolysis oil helps reduce organic waste, contributing to circular economy principles.
- Carbon neutrality: When produced and used efficiently, pyrolysis oil can have a lower carbon footprint compared to conventional fuels.
- Pyrolysis oil aligns with global sustainability and decarbonization goals:
-
Challenges and Opportunities:
- While pyrolysis oil has significant potential, several challenges must be addressed:
- Quality improvement: Current pyrolysis oil has limitations in stability, energy density, and compatibility with existing infrastructure. Ongoing research aims to overcome these issues.
- Economic viability: The cost of production and refining must be reduced to make pyrolysis oil competitive with conventional fuels.
- Policy support: Government incentives and regulations will play a crucial role in promoting the adoption of pyrolysis oil.
- While pyrolysis oil has significant potential, several challenges must be addressed:
-
Role in the Circular Economy:
- Pyrolysis oil contributes to the circular economy by transforming waste into valuable resources:
- Waste-to-energy: Organic waste materials are converted into a usable fuel, reducing landfill use and environmental pollution.
- Resource efficiency: The process maximizes the utility of biomass and waste streams, supporting sustainable resource management.
- Pyrolysis oil contributes to the circular economy by transforming waste into valuable resources:
-
Technological Advancements:
- The future of pyrolysis oil depends on technological innovations:
- Catalytic upgrading: Advanced catalysts can improve the quality and stability of pyrolysis oil, making it suitable for more applications.
- Process optimization: Innovations in pyrolysis technology will enhance efficiency and reduce production costs.
- Integration with existing infrastructure: Developing methods to seamlessly integrate pyrolysis oil into current fuel and chemical production systems will be critical.
- The future of pyrolysis oil depends on technological innovations:
-
Market Potential and Economic Impact:
- The growing demand for renewable energy sources positions pyrolysis oil as a key player in the energy market:
- Industrial adoption: As industries seek sustainable alternatives, pyrolysis oil will see increased adoption in sectors like power generation, manufacturing, and transportation.
- Profitability: Reprocessing pyrolysis oil into higher-value products, such as diesel, can increase profitability and drive investment in the sector.
- The growing demand for renewable energy sources positions pyrolysis oil as a key player in the energy market:
In conclusion, the future of pyrolysis oil is bright, with its potential applications spanning energy, transportation, and chemical production. Continued advancements in refining and upgrading techniques, coupled with supportive policies and technological innovations, will unlock its full potential as a sustainable and economically viable alternative to conventional fuels. As industries and governments prioritize renewable energy and decarbonization, pyrolysis oil is set to play a pivotal role in shaping a more sustainable future.
Summary Table:
Aspect | Details |
---|---|
Current Applications | Power generation, cement factories, iron plants, regulated by ASTM D7544. |
Upgrading Potential | Hydrocarbon fuel production, chemical feedstock, advanced materials. |
Future Applications | Diesel engines, transportation sector, reduced greenhouse gas emissions. |
Sustainability | Renewable energy source, waste reduction, carbon neutrality. |
Challenges | Quality improvement, economic viability, policy support. |
Circular Economy Role | Converts organic waste into fuel, supports resource efficiency. |
Technological Advances | Catalytic upgrading, process optimization, infrastructure integration. |
Market Potential | Industrial adoption, profitability, renewable energy demand. |
Discover how pyrolysis oil can transform your energy strategy—contact our experts today!