The heat source of a rotary kiln primarily depends on the application and the specific requirements of the process. Rotary kilns typically use either electric heaters or gas burners as their heat sources. Electric heaters are preferred for their precise control over heating rates and temperature distribution, making them suitable for various atmospheres such as air, oxygen, nitrogen, and argon. Gas burners, on the other hand, utilize the heat generated from the processed material as fuel, making them energy-efficient by recycling waste heat. The heat can be applied directly inside the kiln chamber or indirectly from the outside, depending on the process needs. Additionally, hot gases, generated either externally or by a flame inside the kiln, flow through the kiln to heat the materials as they move downward.
Key Points Explained:
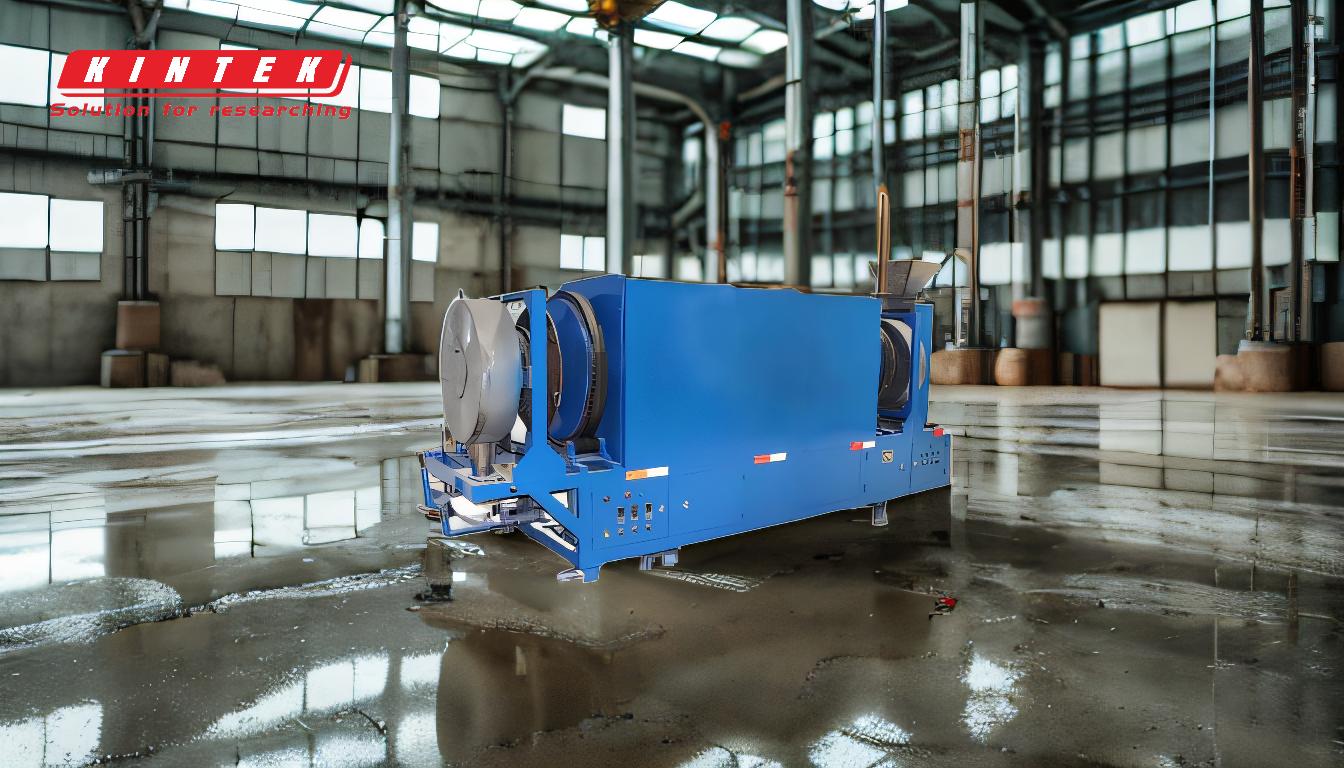
-
Primary Heat Sources in Rotary Kilns:
-
Electric Heaters:
- Provide precise control over heating rates and temperature distribution.
- Suitable for various atmospheres, including air, oxygen, nitrogen, and argon.
- Ideal for processes requiring consistent and controlled heating.
-
Gas Burners:
- Utilize the heat from the processed material as fuel, enhancing energy efficiency.
- Often recycle waste heat, making them cost-effective for large-scale operations.
- Commonly used in industries where high temperatures are required.
-
Electric Heaters:
-
Direct vs. Indirect Heating:
-
Direct Heating:
- Heat is applied directly inside the kiln chamber.
- Suitable for processes where direct contact between the heat source and material is necessary.
- Ensures rapid and uniform heating of the material.
-
Indirect Heating:
- Heat is applied from outside the kiln chamber.
- Used in applications where contamination from direct heat sources must be avoided.
- Provides more controlled and localized heating.
-
Direct Heating:
-
Role of Hot Gases:
- Hot gases flow through the kiln, either in the same direction (co-current) or opposite direction (counter-current) to the material flow.
- These gases can be generated externally in a furnace or by a flame inside the kiln.
- The flow direction of hot gases affects the heat transfer efficiency and the uniformity of material heating.
-
Internal Configuration and Heat Transfer:
- The kiln's internal configuration can be adjusted to optimize heat exposure and material tumbling.
- Adjustments ensure even heating and proper movement of materials toward the exit port.
- Heat transfer mechanisms include conduction, convection, and radiation, depending on the application.
-
Energy Efficiency and Waste Heat Utilization:
- Gas burners are particularly energy-efficient as they recycle waste heat from the processed material.
- This recycling reduces overall energy consumption and operational costs.
- Electric heaters, while not recycling waste heat, offer superior control and are suitable for specialized applications.
By understanding these key points, a purchaser can make informed decisions about the type of heat source and heating method that best suits their specific rotary kiln application. Whether prioritizing precise temperature control, energy efficiency, or process-specific requirements, the choice of heat source plays a critical role in the overall performance and cost-effectiveness of the rotary kiln.
Summary Table:
Heat Source | Key Features | Best For |
---|---|---|
Electric Heaters | Precise temperature control, suitable for various atmospheres (air, O₂, N₂, Ar). | Processes requiring consistent and controlled heating. |
Gas Burners | Energy-efficient, recycles waste heat, cost-effective for large-scale operations. | High-temperature industrial applications. |
Direct Heating | Heat applied inside the kiln chamber for rapid, uniform heating. | Processes needing direct heat-material contact. |
Indirect Heating | Heat applied externally to avoid contamination, controlled and localized heating. | Applications requiring contamination-free heating. |
Hot Gases | Flow direction (co-current or counter-current) affects heat transfer efficiency. | Optimizing heat transfer and material heating uniformity. |
Need help selecting the right heat source for your rotary kiln? Contact our experts today for tailored solutions!